Anyone who runs a high-volume e-commerce business already knows the challenges behind packing and shipping. Every order is unique. Some orders might have single quantities of items that are fragile. At the same time, others might have multiple quantities of different items. Regardless, every order has to be packed securely to ensure customers get what they want, the way they want it.
Order volumes increase from time to time, products undergo improvements, and your inventory catalogs grow in number constantly. Keeping track of warehouse packaging practices and order safety in such a complex scenario is not easy. The packaging is more than just a cardboard box for online shopping. Poor quality or incorrect packaging can cost you lots of money and time wasted on handling returns due to damaged products. And that’s where a robust Cartonization Software comes in. In this article, we will be going over everything you need to know about Cartonization Software and how it can help you take your business to new heights.
What is Cartonization?
Cartonization is an advanced process that determines the best packaging configurations for an order to be shipped based on various parameters. These parameters can be the optimal carton size for a product based on its dimensions and weight, along with packaging material type and pricing. Other parameters like product type and order quantity are also taken into consideration. According to a report, Ikea saved $1.4 million just by optimizing the packaging for one sofa. Cartonization, in simple terms, is the most effective method of packing items for an order before shipping.
The Cartonization Software is often integrated within a Warehouse Management System that is specifically designed to automate the packaging process. The Cartonization Automation Software is very advanced; it employs intelligent algorithms to analyze every item in an order, straight down to its height, length, width, and weight, to strategically determine the best carton or packaging material to be used while packing. This analysis often includes material and labor costs to choose the most cost-effective option. In an e-commerce business, where everything is about speed and efficiency, implementing an Automated Cartonization Software can be very beneficial.
How does Modern Cartonization Software Work?
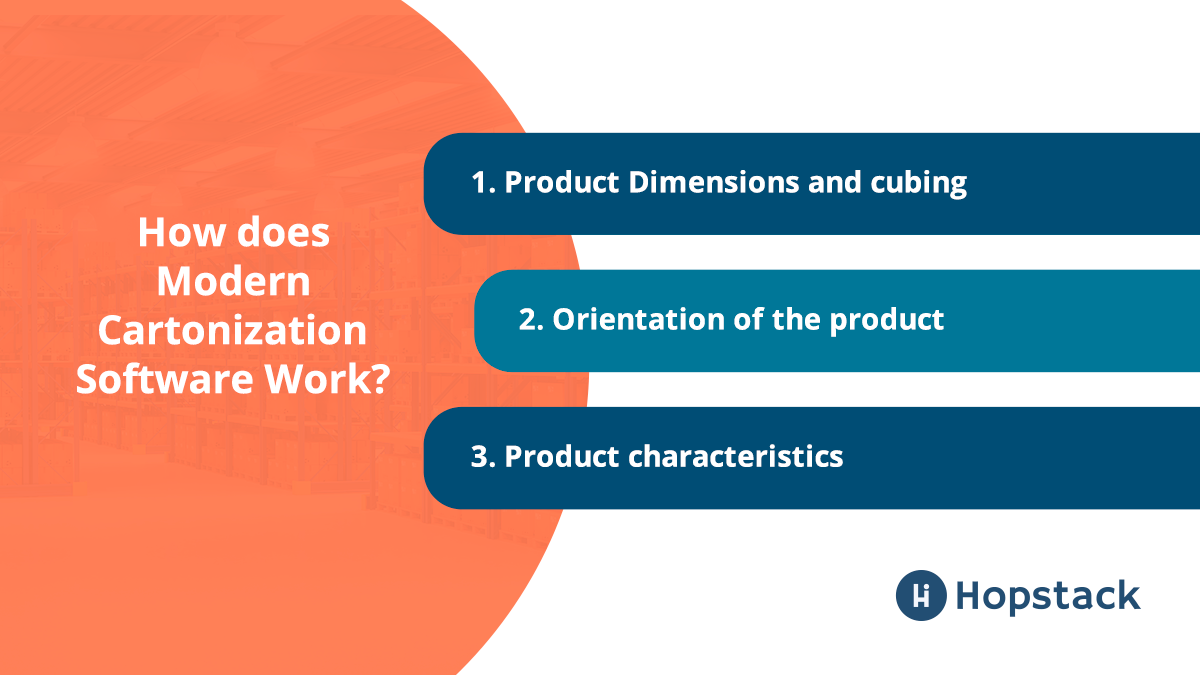
As mentioned above, the Automated Cartonization Software in a Warehouse Management System uses various parameters and factors to determine the most suitable packaging recommendations. It uses advanced algorithms to make this possible. Let us go over these factors to understand how Modern Cartonization Software works.
Product Dimensions and Cubing
One of the most crucial goals of Cartonization Software is to find the smallest cube size. The Cartonization Software analyzes the product dimensions and weight to calculate the smallest cube size using its intelligent algorithm. Knowing the most accurate cube size allows you to determine the most suitable carton box for packing orders quickly.
Orientation of the Product
In some scenarios, changing the orientation of the product can provide the most efficient method of packing. At the same time, it is essential to note that this is not as straightforward as it sounds. Say you are shipping a liquid product. You will have to be particularly mindful about the orientation, as failing to do so could result in leakage and damage when the product reaches the customer. When you use an Automated Cartonization Software, it takes away the guesswork in these scenarios and ensures the most efficient packaging.
Product Characteristics
Every product in your catalog has its unique characteristics. While shipping an order, it is critical to consider these characteristics, such as fragility, leakage, and durability. Your warehouse team will have to pack orders carefully, weighing each product and its attributes. Another vital characteristic of products is compressibility. Some products like clothing and apparel are more compressible when compared to tech and other appliances. When the warehouse team packs these products, the associate will have to consider all of these characteristics and attributes. A Modern Cartonization Software smartly suggests the best packaging materials and practices without you having to worry about these complex characteristics.
Types of Cartonization Configurations

There are different configurations of Cartonization possible. In a Modern Warehousing Management System equipped with advanced Cartonization Automation Software, every step in the process can be customized and configured to match your business needs. In 2017, Dell optimized their packaging on its line-up of products to reduce the packaging size by over 49,000 pounds. It enabled Dell to fit 13% more laptops per pallet during shipping.
In packaging, every centimeter affects your overall packaging costs. Here are some of the types of Cartonization Configurations that could help you understand what’s best for your business:
Single Item Cartonization
When the warehouse receives an order containing only a single item, the Cartonization Software recommends packages or carton boxes to precisely match the specifications of that particular item. The Software also recommends cushioning materials as dunnage to ensure the order is securely packed. Single Item Cartonization is very straightforward and recommended for e-commerce businesses with a fixed set of products with fixed dimensions.
Multi-Item Cartonization
When an e-commerce business has a wide range of products and receives orders containing multiple items and quantities, the Warehouse Management System with modern Software checks each carton's dimensions and capacity restrictions against the items' dimensions and characteristics. The Cartonization Software then recommends packaging that suits the conditions of the order. Multi-Item Cartonization is particularly useful for businesses selling in high-volume categories such as groceries.
Custom Cartonization Configuration
Custom Cartonization Configuration is most suitable for companies and businesses who prefer defining their own Carton packing rules. These businesses can have products that require specific packaging, like pharmaceuticals, or could have inventory-specific packaging requirements. In any case, a robust Warehouse Management System enables warehouse managers and associates to Customize Cartonization Configurations to best suit their business needs.
Challenges Faced by Warehouses and E-commerce Businesses in Fulfillment Packaging
In today’s e-commerce age, there has been a strict standardization in packaging by major e-commerce marketplaces such as Amazon and Walmart. These marketplaces set strict labeling and packaging guidelines that e-commerce business owners need to adhere to if they want to sell on Walmart or Amazon or these other platforms smoothly. The warehouse challenges do not just end there. If your business has both an e-commerce storefront and a brick-and-mortar store, you will have to implement an Omnichannel Fulfillment Strategy. What is particularly challenging about this strategy is that you will have to keep track of packaging and shipping practices individually for each fulfillment point. You will have to ensure every Distribution Center in your e-commerce business network follows these strict guidelines before shipping an order to the customer. Anyone who has run an e-commerce business already knows keeping track of all these is not easy. In addition to that, if you have your custom e-commerce platform, things can get a lot messy.
According to Amazon’s Labeling and Packaging guidelines, if your business uses polythene bags for packaging purposes, you must ensure that these bags are as specified under applicable law. The plastic should be thicker than 50 microns. It should be recyclable, and it should have a logo for recycling. The polythene bag should include information about the manufacturer, including name, address, and license number. It should also include details such as thickness, buyback price, composability (if applicable), and the type of plastic.
It is essential to use adequate cushioning as dunnage to prevent damage during transportation for every order. All items in an order must be packed and shipped in one package. It is also essential to use only new packaging materials while packing for a new order. When packages containing dangerous goods or Hazardous Materials (Hazmat) are to be shipped, they should have the necessary labeling. The same rule holds even for fragile goods; packages containing fragile goods should have the required labeling.
When it comes to labeling, the label print must be clear and readable. The bar code and QR code on the label should be scannable. The label should clearly contain To and From addresses. The label should not be resized to more than four labels on an A4 sheet which is 4x6 inches in size for each label. This is because labels smaller than 4x6 inches cannot be scanned and can get packages lost during transit. The label should be printed with high-quality sticky paper and should be affixed on the visible side of the carton box or package.
In warehouses that implement traditional packing techniques, the warehouse associate must keep in mind all of the above things and packaging constraints associated with the product characteristics. Then the associate has to select the optimal shipping solution to ensure timely delivery of the product. As you might have guessed already, with so much happening, the associate might find this process difficult and even go wrong somewhere along the way. That is why Modern Software is highly recommended in these conditions.
A smart warehousing Management System equipped with advanced Cartonization Software gives real-time recommendations on the best packaging practices. The system considers dimensional weight, cubic size, product type, characteristics, and all the other items in an Order to ensure you select the most suitable packaging material every time.
Bottom Line
Implementing a Warehouse Management System with top-of-the-line Cartonization Software that automates everything from scratch has many benefits. To list a few:
- Increased Throughput - When the Cartonization Software effectively gives accurate recommendations on the best practices to pack orders, you spend time shipping more orders than figuring out what carton to use. A powerful Software increases your business’ productivity and throughput.
- Reduced wastage - According to research, around 140 million tonnes of packaging waste is produced every year. When you implement a Warehouse Management System that recommends precisely the right amount of packaging you need, you reduce wastage and contribute to a cleaner environment.
- Reduced Costs - This goes without saying. When you use the right-sized carton boxes and suitable packaging materials, you significantly reduce costs. In addition to that, smaller and optimal packages mean reduced shipping costs. Implementing Software helps you reduce costs and increase profits.
- Happy Customers - An intelligent Cartonization Software with its real-time recommendations help pack every item securely, meaning they reach your customers in the best conditions. This simply translates into reduced returns due to damages and improved customer satisfaction.
Hopstack’s Cartonization module, which is powered by the integration with Paccurate’s intelligent packaging recommendation system helps warehouses and fulfillment centers in saving costs by minimizing packaging waste and lowering shipping costs. By creating specific rules for certain product classes, warehouses can fix the packaging material and other parameters to ensure the product remains undamaged.
To learn more about Hopstack’s Digital Warehouse Platform and the integration with Paccurate, reach out to us by scheduling a demo.