Modern market conditions have forced businesses to adopt a leaner, more proactive approach to inventory management. Netstock estimates that nearly 80% of small to medium-sized businesses suffer from issues due to insufficient inventory planning, and overstocking or understocking. Optimizing your inventory is just like decluttering your closet; it’s all about making the most of your inventory while simultaneously juggling multiple suppliers, fluctuating demand, and random unpredictable disruptions.
What is Inventory Optimization?
Inventory optimization is the art and science of managing your stock levels to meet customer needs while minimizing costs. It's about striking the right balance between having enough products on hand to fulfill orders and avoiding excess inventory that ties up your cash flow.
How is inventory optimization different from inventory management?
Inventory management is a broader term that encompasses all aspects of controlling and overseeing inventory. It includes tasks such as tracking stock levels, placing orders, receiving shipments, and managing warehouse operations. Think of it as the overall blueprint for managing your inventory.
Inventory optimization, on the other hand, is a more specific strategy focused on fine-tuning your inventory levels to maximize efficiency and minimize costs. It focuses on balancing service levels, ensuring products are available when customers need them, and reducing excess inventory that ties up capital and increases holding costs.
For instance, a warehouse manager might use inventory management tools to track the quantity of a particular product in stock. However, an inventory optimization strategy would involve analyzing historical sales data to determine the optimal reorder point and order quantity for that product. This ensures that the warehouse always has enough stock to meet customer demand without overstocking and tying up capital.
The Importance of Inventory Optimization
Remember the great toilet paper shortage of 2020? That's a prime example of why you need to focus on inventory optimization techniques — it’s about staying agile in a rapidly changing market where supply chain disruptions, demand fluctuations, and evolving customer expectations are constant challenges.
Managing Supply Chain Disruptions
While businesses have always had to bear with supply chain disruptions, the competitive nature of today’s retail landscape offers very little headroom for mistakes. Whether it’s disruption due to global events, natural disasters, or transportation bottlenecks, inventory optimization helps you to not only weather these storms but also treat them as opportunities to get ahead of the competition.
Inventory optimization techniques help manage supply chain disruptions and mitigate these risks by ensuring you have enough buffer stock to handle delays without overstocking or understocking. With a WMS, businesses can gain real-time visibility into stock levels and supplier performance, allowing them to adjust inventory strategies on the fly when disruptions occur.
Handling Demand Volatility and Seasonality
Retailers know the drill: Christmas rush, summer sales, back-to-school frenzy. Demand doesn’t stay constant — it fluctuates based on market trends, seasonality, and even unexpected shifts in consumer behavior. While you can never really know where the demand will shift next, you can do the next best thing — analyze historical sales data and market trends to forecast demand more accurately.
This is where a cloud WMS comes in handy; by leveraging artificial intelligence and forecasting tools, your business can better predict demand patterns and adjust inventory levels accordingly. Whether it’s preparing for holiday season surges or adjusting for off-peak periods, inventory optimization ensures you’re always ready to meet customer needs without tying up capital in excess stock.
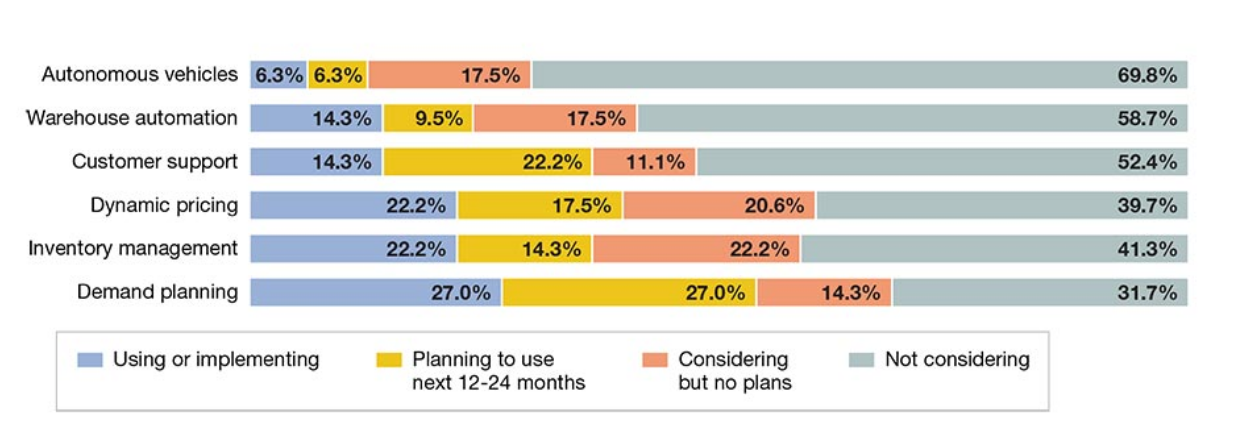
Navigating Supply Chain and Product Complexity
As supply chains grow more complex spanning multiple regions, suppliers, and transportation modes, managing inventory has become increasingly challenging. Add product complexity into the mix (think SKU proliferation or managing perishable goods), and the need for precise inventory control becomes even more critical.
Inventory optimization offers a way to navigate these complexities by way of centralized control over your entire supply chain. It allows you to keep a beat on multiple SKUs across various locations and manage different types of products with ease — whether they’re fast-moving consumer goods or temperature-sensitive items that require special handling. If you can accurately categorize your products into slow-moving and fast selling, then you can figure out how to store them and where to place them in your warehouse to maintain as lean an inventory as possible.
Adapting to Changing Business Models
The way we do business is changing. Subscription models, direct to consumer fulfillment (DTC), and omnichannel retailing are becoming the norm. Traditional inventory strategies no longer cut it when customers expect same-day delivery or click-and-collect options.
Inventory optimization techniques enable businesses to adapt to these new models by streamlining order fulfillment processes and strategically positioning stock in the right warehouse locations to meet demand quickly. The key here is to streamline inventory processes and reduce lead times as much as possible to meet modern customer expectations.
Meeting Evolving Customer Expectations
Retail giants like Amazon and Walmart have led customers to expect fast shipping, real-time order tracking, and seamless returns — all of which put pressure on warehouses to operate efficiently while maintaining high service levels. Inventory optimization strategies ensure that you always have the right products available when customers need them, reducing lead times and improving overall satisfaction.
With a warehouse management system, you can access real-time data on inventory availability across all channels, be it online orders or in-store pickups, so you can fulfill orders faster and with greater accuracy.
Benefits of Inventory Optimization
While inventory optimization is the key to improving warehouse efficiency and customer satisfaction, let’s take a look at how exactly this benefits your bottom line.
1. Cost Savings and Efficiency Gains
Stock optimization can significantly reduce your holding costs. Imagine a retailer who overstocks winter clothing. The excess inventory takes up valuable warehouse space, requires additional labor for handling and storage, and ties up valuable capital in storage fees, insurance, and obsolescence.
Optimized inventory levels can streamline your warehouse operations and avoid costly mistakes. When you know exactly what you have and where it is, you can pick, pack, and ship orders more efficiently. Fewer stockouts mean fewer lost sales opportunities, which directly contributes to a healthier bottom line.
2. Boosting Customer Satisfaction and Loyalty
Nothing frustrates customers more than out-of-stocks. By maintaining optimal inventory levels, you can reduce the risk of stockouts and keep your customers happy. Satisfied customers are loyal customers, and they're more likely to make repeat purchases.
3. Improving Cash Flow and Profitability
Efficient inventory management can free up your working capital. In our experience, we have seen when businesses maintain leaner inventories, they have more cash available to invest in other areas like technology upgrades or expanding product lines. Stock optimization can help you avoid costly markdowns and write-offs, reducing your cash-to-cash cycle time — improving liquidity and financial flexibility.
4. Building a Sustainable and Resilient Supply Chain
In the warehousing business, optimized inventory will always lead to smoother operations on the ground. With better demand forecasting and automated replenishment processes, you can streamline warehouse picking, packing, and shipping activities — further reducing labor costs and minimizing errors. According to a survey by Hai Robotics, the tipping point for an estimated 43% of companies to invest in automation was the need to simplify and improve inventory management processes.
In today's volatile market, where supply chain disruptions are a constant threat, inventory optimization techniques are the key to building a more resilient supply chain. By analyzing historical data and real-time trends, you can ensure there’s enough buffer stock to absorb disruptions while avoiding overstocking that could lead to waste.
As such, inventory optimization plays a key role in enabling sustainability initiatives by reducing waste from overproduction or expired goods (especially in industries like food or pharmaceuticals). By managing stock levels more effectively, businesses can minimize their environmental footprint while still meeting demand.
5. Informed Decision-Making
Inventory optimization is all about data. By analyzing your sales data, purchase orders, and other relevant information, you can make informed decisions about your inventory levels.
For example, you can use data insights from a WMS to switch to more sustainable suppliers or adjust order quantities based on actual consumption patterns, thereby reducing both waste and costs. Inventory optimization isn’t just about having the right amount of stock — it’s about driving cost savings, improving operational efficiency, enhancing customer satisfaction, and even contributing to sustainability goals.
How Does Inventory Optimization Work?
Inventory optimization strategies bring together various technologies and strategies to ensure warehouses operate efficiently while maintaining the right stock levels.
Data Collection and Analysis
The first step is to gather relevant data, including historical sales data, purchase orders, and supplier lead times. This is where a WMS plays a crucial role — it integrates with advanced analytics tools to provide real-time insights into stock.
Demand Forecasting
With a WMS, businesses can use historical sales data, market trends, and predictive algorithms to estimate future demand accurately. By anticipating demand, businesses can adjust their stock levels proactively, avoiding both overstocking and stockouts.
Inventory Level Optimization
Once you have a clear picture of future demand, you can optimize inventory levels. A WMS can automate the process of restocking by setting predefined reorder points and minimum stock levels for each SKU. When inventory dips below these thresholds, the system triggers automatic purchase orders or internal transfers, ensuring that stock is replenished without manual intervention.
With a WMS, you can coordinate technologies like Automated Storage and Retrieval Systems (AS/RS) and cobots to streamline operations help manage the physical flow of goods within the warehouse.
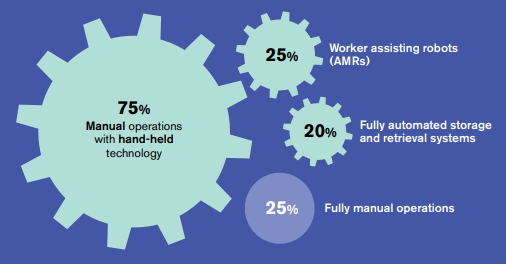
Real-time Inventory Tracking
To ensure that your inventory levels are always accurate, your warehouse needs hardware devices like Barcode and QR scanners, RFID and IoT devices to enhance inventory visibility across multiple locations. These technologies allow warehouses to monitor stock movement in real time, providing accurate data on inventory levels at any given moment.
For instance, RFID tags can track products as they move through the warehouse, while IoT sensors monitor environmental conditions for sensitive items like pharmaceuticals or perishables.
Continuous Monitoring and Optimization
Inventory optimization is an ongoing process. You need to continuously monitor your inventory levels and adjust your strategies as needed. A WMS can help you track key performance indicators (KPIs), such as inventory turnover and fill rates, and identify areas for improvement.
Key Metrics to Measure for Inventory Optimization
Which brings us to our next point — to ensure that inventory optimization efforts are successful, it's essential to track specific metrics that provide insights into stock efficiency, cost control, and overall warehouse performance.
Inventory Turnover Rate
It measures how often inventory is sold and replaced over a given period. A high turnover rate indicates that your warehouse has optimized stock and inventory levels, while a low rate may suggest overstocking or slow-moving items.some text
- Formula: Cost of Goods Sold (COGS) / Average Inventory
- What it measures: The speed at which stock is sold and replenished.
Carrying Cost of Inventory
This KPI calculates the total cost of holding inventory, including storage, insurance, and depreciation. Lower carrying costs indicate more efficient inventory management.some text
- Formula: (Inventory Holding Costs + COGS) / Total Inventory Value
- What it measures: The financial burden of storing unsold goods.
Stockout Rate
The stockout rate tracks the percentage of times a product is unavailable when needed. some text
- Formula: (Number of Stockouts / Total Orders) × 100
- What it measures: How often demand cannot be met due to insufficient stock.
Inventory Accuracy
This metric compares the recorded inventory in your system with the actual physical stock in the warehouse. High accuracy ensures that your data reflects reality, reducing errors in order fulfillment.some text
- Formula: (Recorded Inventory / Physical Inventory) × 100
- What it measures: The precision of inventory records compared to physical counts.
Days Sales of Inventory (DSI)
DSI shows how many days it takes for a company to convert its inventory into sales. A lower DSI indicates faster turnover and better liquidity.some text
- Formula: (Average Inventory / COGS) × 365
- What it measures: The average time products sit in storage before being sold.
Fill Rate
This metric measures the percentage of customer orders fulfilled from available stock without backorders or delays. A high fill rate reflects effective inventory management and customer satisfaction.some text
- Formula: (Orders Fulfilled on Time / Total Orders) × 100
- What it measures: How well you meet customer demand from current stock levels.
Shrinkage
Shrinkage quantifies the loss of inventory due to theft, damage, or administrative errors. Monitoring this metric helps identify inefficiencies or security issues within the warehouse.some text
- Formula: (Recorded Inventory − Actual Inventory) / Recorded Inventory × 100
- What it measures: The amount of lost or unaccounted-for stock.
Safety Stock Levels
Safety stock is the extra inventory that warehouses keep on hand to prevent stockouts during unexpected demand spikes or supply chain disruptions. Monitoring safety stock ensures you have enough buffer without overstocking.
- What it measures: The level of buffer stock needed to avoid disruptions.
How Hopstack helps with Inventory Optimization
Hopstack’s intelligent inventory management solutions help businesses optimize inventory and stock levels, achieve precise control, and get real-time visibility across all channels. Our WMS leverages automated processes, dynamic allocation, and real-time tracking to help businesses reduce stockouts, improve order fill rates, and streamline warehouse operations.
Contact us to schedule a demo and learn more about how Hopstack can transform your inventory optimization and enhance your operational efficiency.