Customer expectations have evolved to anticipate faster delivery of e-commerce products. According to a study by Statistia, nearly two-thirds of global shoppers anticipated receiving their items within 24 hours, with four in ten expecting delivery in under two hours. Order batching emerged out of this need to balance efficient warehouse operations with faster fulfillment.
At its heart, order batching is essentially the process of consolidating multiple orders into batches that can be fulfilled at the same time. It reduces the travel time within the warehouse, minimizing unnecessary movement and maximizing the number of orders fulfilled per hour. By consolidating orders into one pick route, warehouses can streamline operations, reduce labor costs, and enhance overall productivity.
What is Order Batching?
Order batching is an intermediary process in warehousing which improves efficiency by allowing pickers to collect items for multiple orders in a single trip. It involves grouping multiple orders together based on shared characteristics, such as similar items or destinations, to optimize the picking and fulfillment process. This method accelerates the picking process to process and ship orders faster, giving your business an edge when it comes to meeting customer expectations.
However, we must remember that this approach is not merely about grouping orders; it is about finding that perfect between strategic, operational, and tactical actions for maximum order fulfillment efficiency.
What is Fulfillment Batching?
Fulfillment batching takes the concept of order batching a step further by integrating it into the broader fulfillment process. While order batching focuses primarily on the picking phase, fulfillment batching considers the entire journey of an order—from picking to packing and shipping. This comprehensive approach ensures that the benefits of batching are realized throughout the fulfillment cycle, leading to a more synchronized and efficient warehouse operation.
In fulfillment batching, orders are not only grouped for picking but are also strategically managed through subsequent stages. This might involve coordinating packing stations to handle specific types of batches or optimizing shipping schedules to align with batch completion.
Types of Order Batching Strategies
To effectively optimize warehouse operations, it's essential to select the right order batching strategy. The most effective order batching solution will depend on a variety of factors, including:
- Order profile: The size, frequency, and complexity of orders.
- Warehouse layout: The physical arrangement of the warehouse and its storage systems.
- Labor availability: The number and skill level of available workers.
- Technology capabilities: The availability of advanced technologies like warehouse management systems (WMS).
Here are four common order batching strategies:
Wave Picking
Wave picking involves grouping orders into batches based on specific time windows or criteria, such as shipping deadlines or product similarity. This method allows for efficient picking runs by aligning order fulfillment with other warehouse processes like shipping schedules. Wave picking is particularly effective in high-volume operations where timing is critical, such as in retail or e-commerce warehouses needing to meet carrier deadlines.
Zone Picking
In zone picking, the warehouse is divided into distinct areas or zones, with each picker assigned to a specific zone. Pickers only collect items from their designated zones, which reduces travel time and minimizes congestion. This method is ideal for large warehouses with a high SKU count, such as those in the retail sector, where items are spread across vast areas.
Zone picking is beneficial for maintaining organization and reducing picking errors, although it may require coordination between zones for order completion.
Cluster Picking
Cluster picking allows workers to pick items for multiple orders simultaneously, typically using a cart or totes to separate different orders. This strategy minimizes travel and wait times, making it suitable for e-commerce fulfillment centers with a high volume of small orders. Cluster picking is efficient for facilities with a variety of SKUs, but it requires careful sorting and organization to avoid errors.
Hybrid Batching
Hybrid batching combines elements of wave, zone, and cluster picking to tailor the picking process to a warehouse's specific needs. This approach is adaptable and can be customized based on the type of orders, warehouse layout, and operational goals. Hybrid batching is particularly useful in versatile industries that require a flexible picking strategy to handle diverse order profiles and fluctuating demands.
Challenges of Order Batching
Implementing order batching solutions come with their fair share of challenges. By acknowledging and understanding these challenges, businesses can better prepare for the complexities of implementing an order batching solution.
Complexity of Implementation
Implementing an effective order batching system can be complex, often requiring significant software or system upgrades from traditional paper-based processes. For instance, a large e-commerce company might need to invest in a sophisticated warehouse management system to effectively batch several types of orders. The complexity of integrating new systems can lead to initial disruptions and require extensive training for staff.
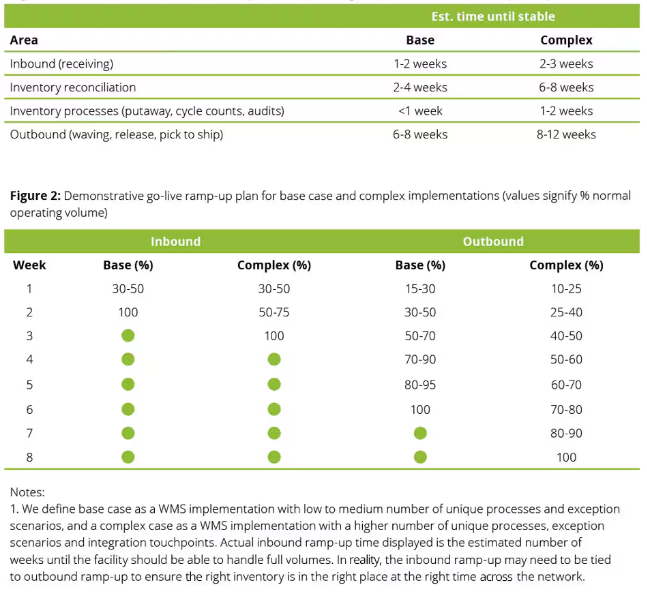
Figure 1: Estimated time to reach stable state for warehouse processes for base case and complex implementations. (Source: Deloitte)
Businesses need to plan ahead and ensure support for existing processes before committing to long-term efficiency gains.
Increased Need for Coordination
Implementing fulfillment batching or order batching software in a large enough warehouse requires precise coordination between different, including order processing, picking, packing, and shipping.
In a pharmaceutical warehouse, for example, the coordination between picking, packing, and shipping teams is critical to ensure that time-sensitive medications are dispatched promptly. Poor coordination can result in delays and inefficiencies. Implementing regular cross-departmental meetings and using collaborative software tools can help streamline communication and improve coordination.
Potential for Delays
If not professionally managed, batching can lead to bottlenecks, particularly when orders vary greatly in size or complexity. A fashion retailer with fluctuating seasonal demands might experience delays if large, complex orders are batched with smaller, simpler ones, leading to a slowdown in processing times.
To address this, businesses can implement dynamic batching rules that adjust based on order characteristics, ensuring smoother operations.
Batch Size Issues
Determining the optimal batch size is crucial; overly large batches can slow down processes or increase the risk of errors. A small batching error in a large batch can result in significant rework and delays. For example, if a few items are accidentally left out of a large batch, the entire batch may need to be repicked, causing significant disruptions to the fulfillment process.
In a consumer electronics warehouse, large batches might lead to longer picking times and picking errors, especially during peak periods like Black Friday. Regularly reviewing and adjusting batch sizes based on order volume and warehouse capacity can help maintain efficiency and accuracy.
Customization Limitations
Order batching software may struggle with unique orders that don’t fit easily into standard processes. A custom furniture manufacturer, for example, might face challenges when batching bespoke orders that require special handling or assembly.
Businesses can address these limitations by implementing flexible batching strategies to allow for exceptions and customization, ensuring that unique orders are processed without disrupting the overall workflow.
How to Implement Order Batching Solution in Your Fulfillment Center
Implementing order batching solutions in your fulfillment center requires a systematic approach to ensure successful integration and optimization. Here's a roadmap to guide you through the process:
Evaluate Current Processes
Identify bottlenecks: Begin by conducting a comprehensive assessment of your current order fulfillment workflows. Pinpoint areas where order fulfillment is slowing down or causing inefficiencies. This involves analyzing foundational warehouse metrics including order processing times, picking times, and travel distances.
Assess order types and volumes: Determine the variety and frequency of orders to inform your batching strategy. Consider factors such as order size, product complexity, and peak demand periods.
Analyze workforce utilization: Evaluate how your current staff is allocated and if there are opportunities for more efficient task distribution. This involves assessing labor costs, productivity levels, and skill sets.
Choose the Right Batching Strategy
Consider warehouse layout: Evaluate the physical arrangement of your warehouse to determine if zone or cluster picking would be more suitable. For example, if your warehouse has distinct zones for different product categories, zone picking might be a good fit.
Assess order characteristics: Consider the size, complexity, and frequency of orders to select the most effective batching method. For instance, if you have a high volume of small, similar orders, wave picking might be efficient.
Evaluate technology capabilities: Determine if your existing systems can support the chosen batching strategy or if upgrades are necessary. For example, if you want to implement wave picking, you might need to invest in a WMS that can handle time-based batching.
Integrate Batching with Warehouse Management Systems (WMS)
Ensure compatibility: Verify that your WMS can handle batching functionality or explore options for upgrading. If your WMS doesn't support order batching software, you may need to invest in a new system or customize your existing one.
Configure batching rules: Set up rules for grouping orders based on your chosen strategy. This might involve defining batch sizes, time windows, or other criteria.
Integrate with other systems: Connect your WMS with other systems, such as transportation management systems (TMS), to ensure seamless communication and coordination.
Integration is key — your WMS should seamlessly manage batch creation, tracking, and execution, providing real-time insights into order progress and inventory levels.
Use Automation Tools
Evaluate automation opportunities: Identify areas where automation can enhance batching efficiency, such as automated picking systems or robots. For example, if you have a high-volume, repetitive picking process, automated order management can significantly improve productivity and accuracy.
Select appropriate technology: Choose automation tools that align with your budget, scalability requirements, and specific needs. Consider factors such as the ROI of the technology, ease of integration, and maintenance requirements.
Integrate with existing systems: Ensure that automation tools can seamlessly integrate with your WMS and other systems. This might involve developing custom interfaces or using middleware solutions. An estimated 69% of decision-makers have or are planning to automate workflows by 2024.
Assess and Optimize
Conduct pilot tests: Implement batching in a controlled environment to evaluate its effectiveness and identify potential issues. Start with a small subset of orders and gradually expand the scope as you gain confidence.
Collect data: Track key performance indicators (KPIs) such as picking time, error rates, and labor costs. This data will help you measure the impact of batching and identify areas for improvement.
Make adjustments: Analyze the data and make necessary adjustments to the batching strategy or processes. This might involve modifying batch sizes, changing picking routes, or adjusting automation settings.
Train Your Team
Provide comprehensive training: Educate your warehouse staff on the new batching system, including its benefits, processes, and best practices. Use role-playing exercises, simulations, and hands-on training to ensure that employees understand how to execute the new processes correctly.
Address concerns and questions: Be available to answer questions and provide support to overcome challenges during the implementation and adjustment phases. Encourage employees to share their feedback and suggestions for improvement.
Foster a culture of continuous improvement: Create a culture where employees are empowered to identify and implement process improvements. This might involve implementing suggestion boxes, providing incentives for process improvements, or encouraging employees to participate in lean or six sigma initiatives.
Conclusion
A study by Zebra identified sorting and packing, order picking, and put-away operations as the top drivers of error rates in the warehouse. Under these circumstances, implementing order batching software in your fulfillment center offers tons of benefits — from increased efficiency and reduced travel time to significant cost savings and improved order accuracy in the long term.
We encourage businesses to take a closer look at their current fulfillment processes and consider how order batching software could address existing bottlenecks and inefficiencies. Whether it's wave, zone, cluster, or hybrid batching, avoiding common pitfalls and choosing the right strategy tailored to your specific needs can transform your warehouse operations.
Contact us to schedule a demo of Hopstack’s WMS with advanced support for order batching solutions. Consulting our experts to understand how our order fulfillment software can help position your business for success.