If a warehouse operation wants to trim costs, where should it start? A good place would be with order picking or warehouse picking automation.
According to Mckinsey, with proper operations analysis, warehouse companies can improve their cost profile with gains of up to 20% — and picking is a central source of labor cost. Additionally, there are other hidden costs associated with picking such as loss of customer satisfaction and brand reputation.
Picking automation in warehouse improves the outcomes in all cases. Let's find out how
Why Automate Picking In Warehouse?
The fastest, most effective way to improve efficiency in warehouse picking is through automated warehouse picking. The reasons are simple. Warehouse picking automation accelerates the process, conserves resources, and minimizes error.
Every warehouse order triggers a pick path. For large, complex facilities, these paths are increasingly difficult to optimize. When you add options, such as kitting and order assembly, the complexity skyrockets.
Specialized software platforms can organize and accelerate the automated warehouse picking process. Starting with ecommerce order fulfillment or placement, these platforms map the shortest pick path. Higher picking rates result in faster customer deliveries.
Warehouse picking automation incorporates the latest technology in warehousing to carry out order-picking operations in warehouses. Businesses are using a wide variety of solutions ranging from modern autonomous mobile robots (AMRs) to picking assistance devices (e.g., pick-to-light) and industrial robotic arms, which can be customized to fit any type of facility and item to enhance warehouse picking automation.
Automated Warehouse Picking Combines IoT and Software
The Internet of things (IoT) in the automated warehouse picking approach enables physical devices and equipment to be sensed and controlled remotely across an existing network infrastructure. IoT networks capture data about objects and devices to be analyzed and managed by computer-based systems.
For warehouses, convenient applications use the data to quickly determine things like the best pick path for any given order. Data can be visualized which further improves warehouse operations since it's much easier to identify choke points.
Top 6 Warehouse Picking Automation Strategies
In the ever-evolving landscape of warehousing and logistics, picking remains one of the most time-consuming and critical tasks. As businesses seek to meet the demands of a digital age where speed, accuracy, and efficiency are paramount, turning to automation becomes not just preferable but essential. Here’s how picking automation strategies are reshaping warehouse operations:
1. Robotic Picking Systems
Gone are the days when robots were limited to the realms of science fiction. Modern warehouses are leveraging robotic picking systems to retrieve items without human intervention. These robots are designed to navigate vast storage areas, select the required items with precision, and transport them to the packing zone. Integrated with inventory management software, they ensure rapid and error-free picking.
2. Voice-Directed Picking
Harnessing the power of voice recognition technology, voice-directed picking systems provide workers with audio instructions. Workers wear a headset that communicates which items to pick and where to find them. This hands-free method not only speeds up the process but also significantly reduces errors compared to traditional paper-based methods.
3. Pick-to-Light Systems
A game-changer in high-density storage environments, pick-to-light systems use LED lights to guide workers to the right storage locations. Upon reaching the highlighted spot, the worker can quickly see the quantity needed, reducing decision time and improving picking speed.
4. Advanced Barcode Scanning
With the integration of AI and machine learning, modern barcode scanners are more than just reading devices. They analyze, sort, and prioritize picking orders based on real-time data, ensuring optimal routing and efficient batch picking.
5. Automated Storage and Retrieval Systems (AS/RS)
These systems are a combination of equipment and controls that handle, store, and retrieve materials with precision, accuracy, and speed. By reducing human intervention, AS/RS systems minimize errors, enhance storage density, and streamline the picking process.
6. Smart glasses / Augmented reality / Pick by vision
Picking instructions and order location/info appear in visual displays on smart glasses. Pickers are free from carrying paper instructions or devices for improved, hands-free workflow.
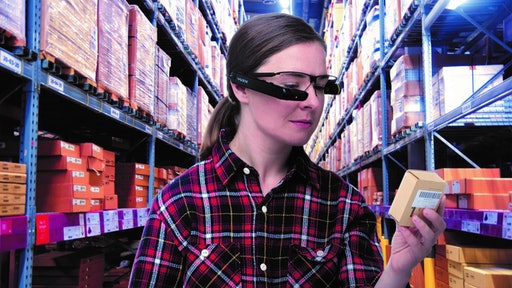
Key Metrics for Measuring Picking Automation Efficiency
One might imagine that this level of connectivity opens up many opportunities to measure warehouse performance with greater detail and precision. Consider these metrics.
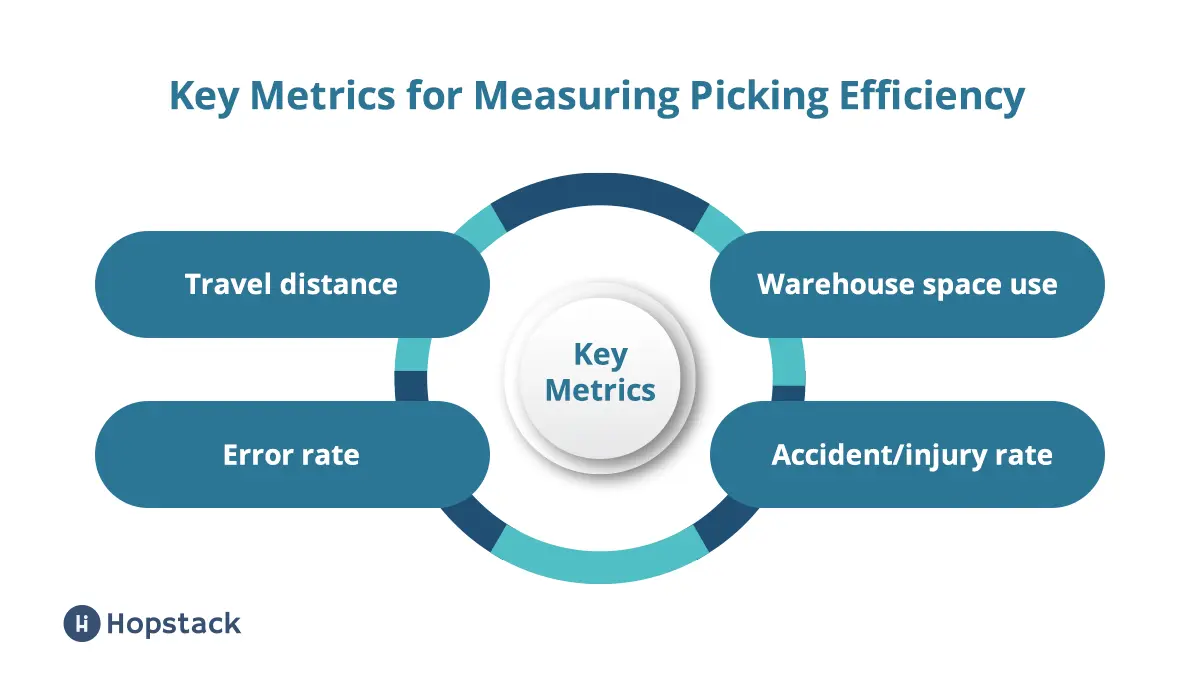
Travel distance - One of the crucial metrics for warehouse picking automation is the shorter the pick path distance, the faster goods get delivered. Spaces can be automatically measured with a high level of accuracy, and built-in programs reveal shorter routes.
Warehouse space use - IoT in warehouse and software can help optimize warehouse layout. This occurs along with two variables: maximize inventory per square foot/meter and ideal inventory placement for shorter picking times.
Error rate - Error tracking enables managers to improve process accuracy. Automated picking can even see error rates approach 0%. This translates into fewer returns and improved customer satisfaction
Accident/injury rate - By shortening pick paths, workers don't have to exert themselves as much. Hopstack's Digital Warehouse Platform's integration with smart wearables can even track workers' vital signs to ensure employees aren't exhausting themselves.
Top Benefits of Automated Warehouse Picking
What are the business benefits of enable warehouse picking automation? Here are some key factors.
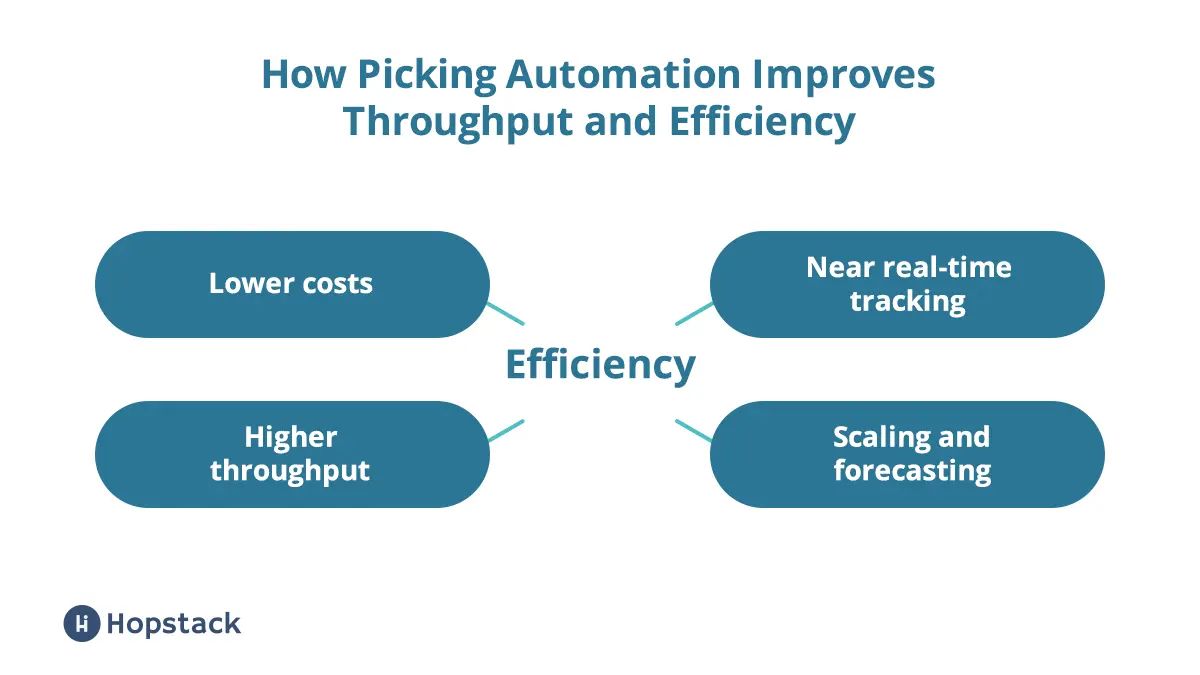
Lower costs - Warehouse picking automation optimizes the use of labor, equipment, and storage space. Management tasks are reduced as analysis and performance enhancement are automated. Order return costs shrink too (the cost of returns in the US is estimated at $550 billion per year).
Near real-time tracking. - Warehouse picking automation improves the handling of temperatures and time-sensitive goods, such as perishables and pharmaceuticals—the accurate visibility into storage and delivery results in better margins.
Higher throughput - With efficient warehouse picking software, more items reach their destination per day.
Scaling and forecasting - With improved space and resource use, warehouses can scale faster to meet demand spikes. With automatically collected data, managers make better predictions about inventory flow given seasonal or demand fluctuations.
Enable Picking Automation Now
Hopstack's Digital Warehouse picking automation software offers a fully integrated plug-and-play platform for picking automation. It seamlessly integrates with Voodoo Robotics wireless pick-to-light (PTL), to reduce businesses' onboarding friction.
Businesses can have free access for a month to Hopstack's trial platform enabling them to try out PTL solutions before deploying in production.