Overall, the benefits of digital warehouse automation include higher throughput, less human error, accident minimization, and reduced costs. Given that warehouse sorting is largely a mechanized process, all these benefits may be realized at higher levels with sorting automation. Let’s see how this works.
Considerations before implementing sorting automation
It’s critical to approach automated sorting with adequate foresight. Some questions to consider prior to implementation include:
- What are the throughput requirements?
- In the warehouse operations, at which stage is sorting automation needed??
- How much warehouse floor space is available?
- What will the system sort? (package type, dimensions, weight, fragility, variety, etc.)
- Will products be manually inducted or integrated with existing material handling?
- Are any other processes required (scan, dimension, weigh, label, etc.)?
- How many sort points (destinations are required?
- What type of bin (dimensions) will be used to collect sorted products?
- How is the product received or shipped? In pallets, cases, or individual packages?
- For put away, do items go to static or dynamic storage?
- How will shipping data be collected?
- Will new products be added in the future?
By answering these questions as accurately as possible, it becomes easier to choose the right sorting system. Another factor to consider is the need for future warehouse growth or adaptation as modular sorting systems have equipment that can be easily added on or swapped out.
Automated Sorter Types
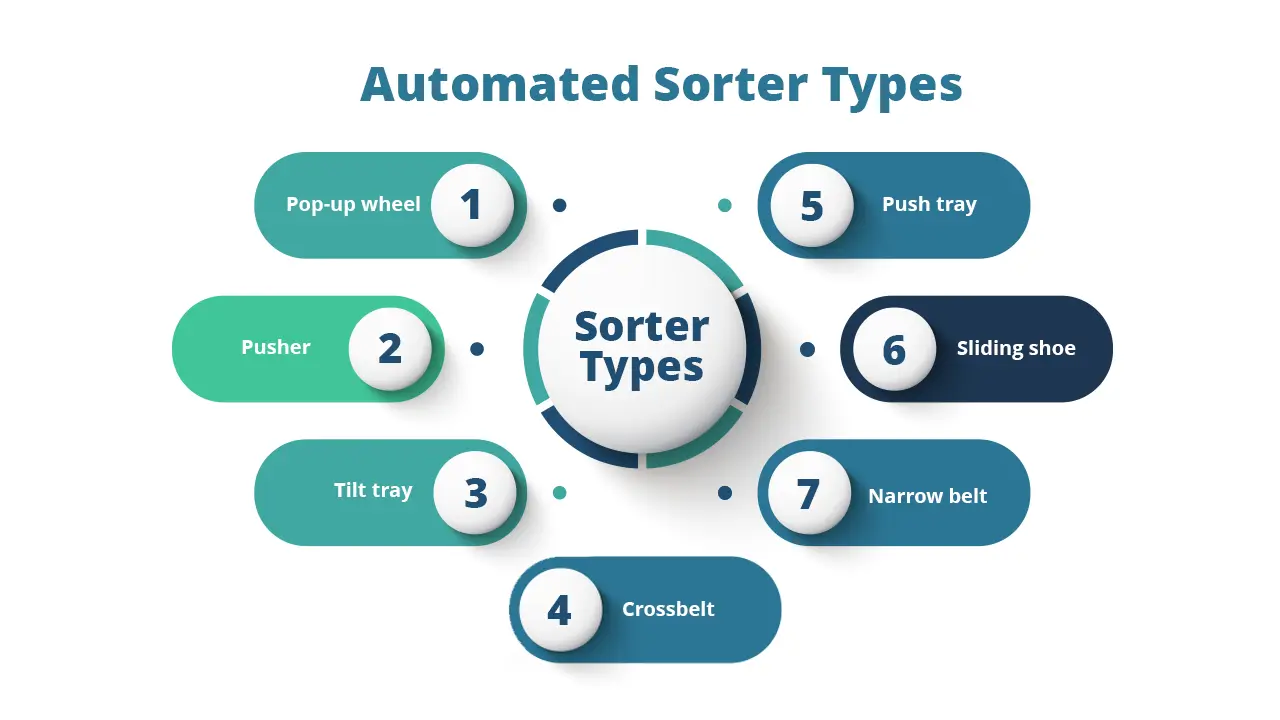
Automated sorting systems vary significantly in how their mechanisms work. Here are some of the more commonly available sorters:
Pop-up wheel - Wheels or rollers pop up to lift items off the conveyor surface for selective package diversion.
Pusher - Telescopic bars push items off the conveyor to shutes or secondary conveyors..
Tilt tray - The conveyor is equipped with tilting trays that dump products into lateral chutes or bins.
Crossbelt - Consists of a series of wide belts wrapped perpendicularly around the main conveyor belt. When the package reaches its destination chute, a cross belt is activated to transport the package to either side.
Push tray - Similar to pusher sorters, the conveyor has a series of trays each with its own push bar to divert items.
Sliding shoe - Shoe-like devices along the sides of the main conveyor slide across to push items off into chutes or bins.
Narrow belt - Items ride on top of long parallel belts with spaces in between them. To divert a package, rollers rise up between the belts to move the item to either side
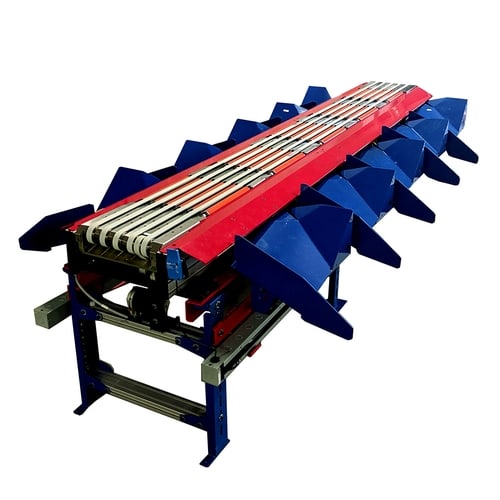
Enhanced Sorting Automation
Sensor technology enhances sorting performance. For instance, packages can be equipped with sensors that activate conveyor control mechanisms.
Beyond the more efficient physical movement of packages, automated warehouse/sorting solutions also enable precise digital inventory and expedited shipping tracking. Also, warehouse automation can optimize the movement and storage of items within the facility, especially for larger, more complex inventories.
Sorters can now also be retrofitted with labeling systems combined on a shipping sorter.
Key Sorting Metrics
The most direct measurable metric improved by automated sorting is the item throughput rate. Other metrics that can be improved include:
- Inventory turnover rate
- Lead time, order cycle time
- Order accuracy rate
- Time to ship
- Percentage of on-time shipments
Other Benefits of Sorting Automation
Additional benefits of sorting automation include:
- The sorting area is condensed for warehouse space optimization.
- Sort accuracy improvement due to less human error
- Sustained throughput as systems are less limited by staff shifts.
- Less package handling means safer work conditions and fewer accidents.
Cost benefits of sorting automation include:
- Fewer events result in damage to infrastructure or goods.
- Improvement of order accuracy which minimizes return costs.
- Reduced labor requirements.
- Increased order fulfillment capacity
End-to-end warehouse automation
When sorting is digitally integrated into the entire flow of automated warehouse operations, companies realize significant improvements to performance and their bottom line.
Intelligent software can automate, optimize, and track processes from end-to-end such as receiving, put away, storage, picking, packing, and shipping. Additionally, with automatically generated data insights, processes can be continuously improved.
Find out how Hopstack can move your warehouse sorting to an improved level of automation performance and cost-efficiency. Hopstack’s cloud-based Digital Warehouse software platform integrates with sorters at different operational stages to enable efficient automation workflows and, actionable data capture.
Warehouses can use the Order Audit Trail feature on the Hopstack Digital Warehouse platform to get a near-real-time view of their receiving and fulfillment activities.
Our partner Fluence Automation, provides sorting systems for parcels of different size and form factors.
Fluence (previously Bell and Howell mail and parcel sorting division) has provided solutions in the mail and parcels marketplace for nearly 50 years. As a full integrator of material handling solutions, Fluence combines its strength in engineering design with Fluence-developed products as well as other 3rd party components to provide a complete integrated system solution.