In a survey, nearly 70% of organizations said they need better visibility into warehouse operations. Businesses strive to ensure that their records and data are maintained in the best possible way so that revisiting that data, as well as extracting it, is as easy as possible. Warehouses are one of the largest data generators of any business due to the complexity of their operations. A typical order line item gets handled at least 15-20 times throughout its fulfillment lifecycle, and each of these handling actions generates multiple data points. Most, if not all the data, around these actions, are not captured today. Lack of data, not only hampers the warehouse operators' ability to gain granular visibility into the fulfillment journey but also prevents them from sharing that data with external stakeholders such as end customers, audit teams, etc. Manually maintaining and tracking all of this data is cumbersome and if the warehouse’s existing WMS solution is not tracking this data, it is likely losing a lot of money and time. This is where the platform’s audit trail comes in.
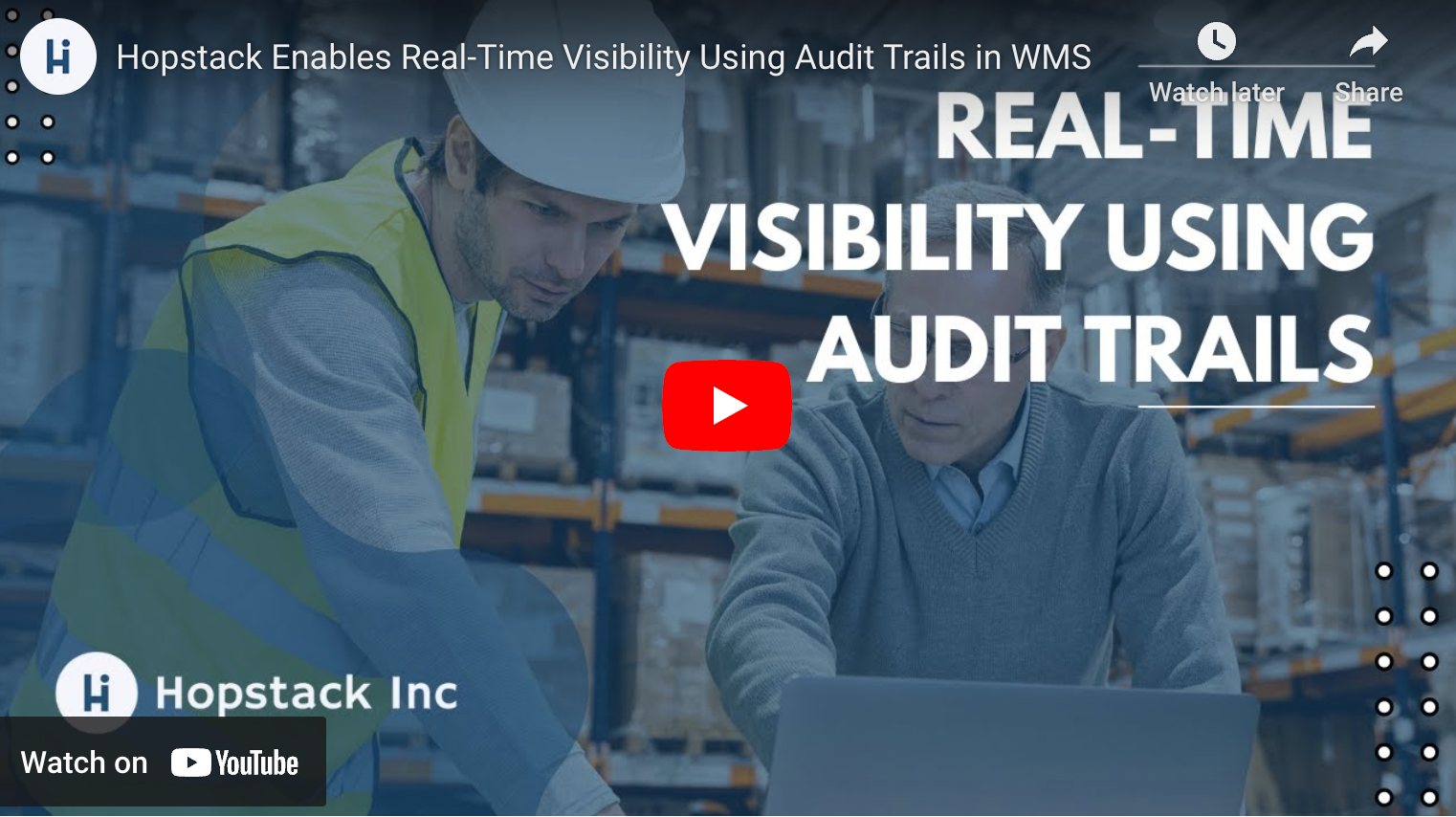
The audit trail allows warehouse managers and business owners to accurately track and maintain data about every single order line item that hits their system in the most efficient way possible. Interested in learning more? Here’s how it happens.
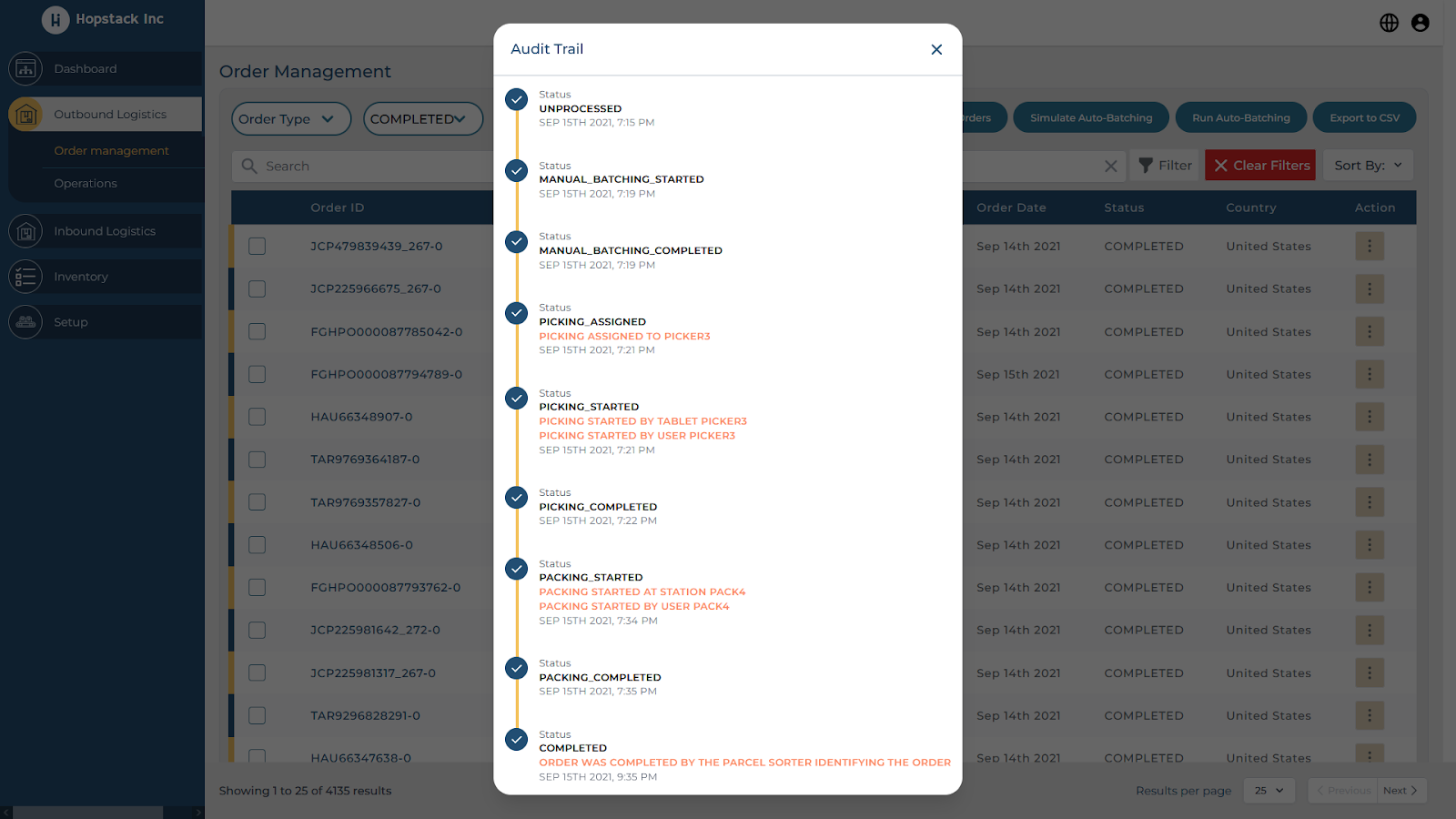
Granular Auditing
The audit trail feature in the platform highlights every single detail related to an order with a timestamp. Right from the time the order is received by the warehouse, to the time it is picked up to be delivered to a customer, everything is mapped and stored in the platform’s data stores. Because of this, auditing on a shipment and order level, warehouse personnel are empowered to store and track immutable records of their inventory at any time. Along with timestamp, warehouse managers can also see the personnel assigned to the order as well as the locations within the warehouse where fulfillment took place. If order number 19 was picked by Sam the picker (after being automatically batched by our batching algorithm) and taken to packing table 7, where Gregory the packer packed the order and placed it into shipping basket 4, then Jane the warehouse manager would know all of this as it is happening in real-time. Cool, right?
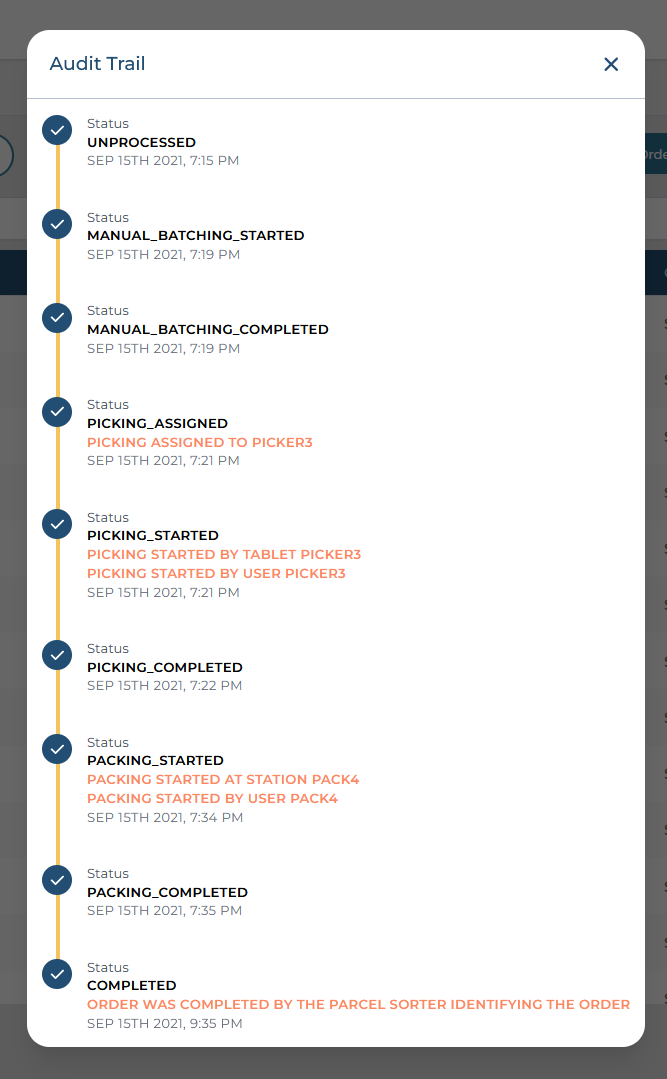
Beyond Fulfillment: Consolidating Shipping Details
What’s more, is that if warehouses have opted to harness the power of one of the platform's multiple shipping integrations, the audit trail will expand to include shipping details of the consignment and give you details about the transit status, delivery status, and other essential shipping information right within the platform. This ensures that fulfillment personnel can have a seamless experience in fulfilling orders and warehouse managers can easily look back at the journey of any order.
Hopstack’s audit trail feature allows warehouse personnel to leverage the power of immutable record-keeping to accurately track and maintain details about the journey of an order.
Learn more about how Hopstack’s audit trailing can help you get better oversight over your warehouse operations. To get in touch with a product expert, Schedule a demo.