Modern warehouses must operate at peak speed and precision to succeed and deliver value in today’s competitive landscape. At the heart of seamless order fulfillment lies warehouse efficiency, where every process — from inventory management to shipping — is optimized for maximum productivity. Let’s look at how increasing warehouse efficiency can turn your warehouse into a well-oiled machine capable of handling modern fulfillment needs.
What is Warehouse Efficiency?
Warehouse efficiency measures the ability to streamline operations to achieve optimal performance and productivity. Businesses must leverage the right technology and processes to effectively manage resources such as space, labor, equipment, and inventory to minimize waste and maximize output. Think less time searching for items, fewer errors, and faster order fulfillment, all contributing to a smooth-running supply chain.
From the moment goods enter the warehouse to their dispatch for delivery, every step has to be meticulously orchestrated to minimize waste and maximize output.
Why is Warehouse Efficiency Important?
Efficient warehousing markedly improves productivity, reduces costs across the board, and increases business agility.
How do you measure and increase warehouse efficiency metrics?
Warehouse efficiency metrics can be measured and quantified through various key performance indicators (KPIs) that offer insights into the effectiveness of operations.
1. Inventory Accuracy Rate
The inventory accuracy rate records the percentage of inventory items accurately recorded in the warehouse compared to the actual physical count.
Inventory accuracy rate =(Number of accurate inventory items / Total number of inventory items) x 100
High inventory accuracy ensures proper inventory management, minimizes stockouts and prevents overstock situations.
2. Order Picking Accuracy
Order picking accuracy (OPA) measures the number of orders picked accurately without errors or discrepancies out of the total number of orders picked for a specific period.
Order picking accuracy =(Number of accurately picked orders / Total number of orders picked) x 100
Warehouses should prioritize accurate order picking to improve fulfillment efficiency, reduce errors, enhance customer satisfaction, and mitigate the need for order corrections or returns. While it’s not possible to reach an order picking accuracy of 100 percent, best-in-class companies report an OPA of 99.8 percent.
3. Perfect Order Rate
Perfect order rate is the percentage of orders fulfilled without any errors, including accurate items, quantities, and on-time delivery.
Perfect order rate = (Number of perfect orders / Total number of orders) x 100
If your warehouse has a high perfect order rate, that means you have established operational excellence with the right balance of technology and processes. Perfect order rates help businesses boost customer trust and minimize costs associated with order discrepancies.
4. Order Cycle Time
Order cycle time is the time it takes for you to fulfill an order, from order placement to order fulfillment, including processing, picking, packing, and shipping.
Order cycle time = (Delivery date – Order date) / Total orders shipped
Monitoring order cycle time helps identify bottlenecks, improve warehousing efficiency, and meet delivery commitments.
5. Inbound Throughput
Inbound throughput is the rate at which your warehouse receives, unloads, inspects, and makes available for storage or processing any and all incoming goods. It’s a measure of the efficiency of your warehouse labor, existing procedures, and technology integration.
Inbound throughput = (Number of items received / Total receiving time)
Efficient inbound throughput ensures timely inventory availability, minimizes replenishment delays, and supports smooth warehouse operations.
To establish a baseline and benchmark your warehouse's current state, conduct an internal audit focusing on key areas like receiving, picking, and inventory management. Gather data from various sources, including inventory levels, order processing times, and employee productivity to reduce order cycle times and improve accuracy. Compare the collected data against industry standards or internal benchmarks to identify areas for improvement.
This exercise will help you then develop an action plan that outlines specific actions, responsibilities, and measurable goals for improvement. Then, it's simply a matter of implementing the plan, monitoring progress, and tracking the impact on warehouse efficiency KPIs.
Remember, an internal audit is an iterative process – the key lies in the continuous evaluation of warehouse efficiency metrics and regular refinement.
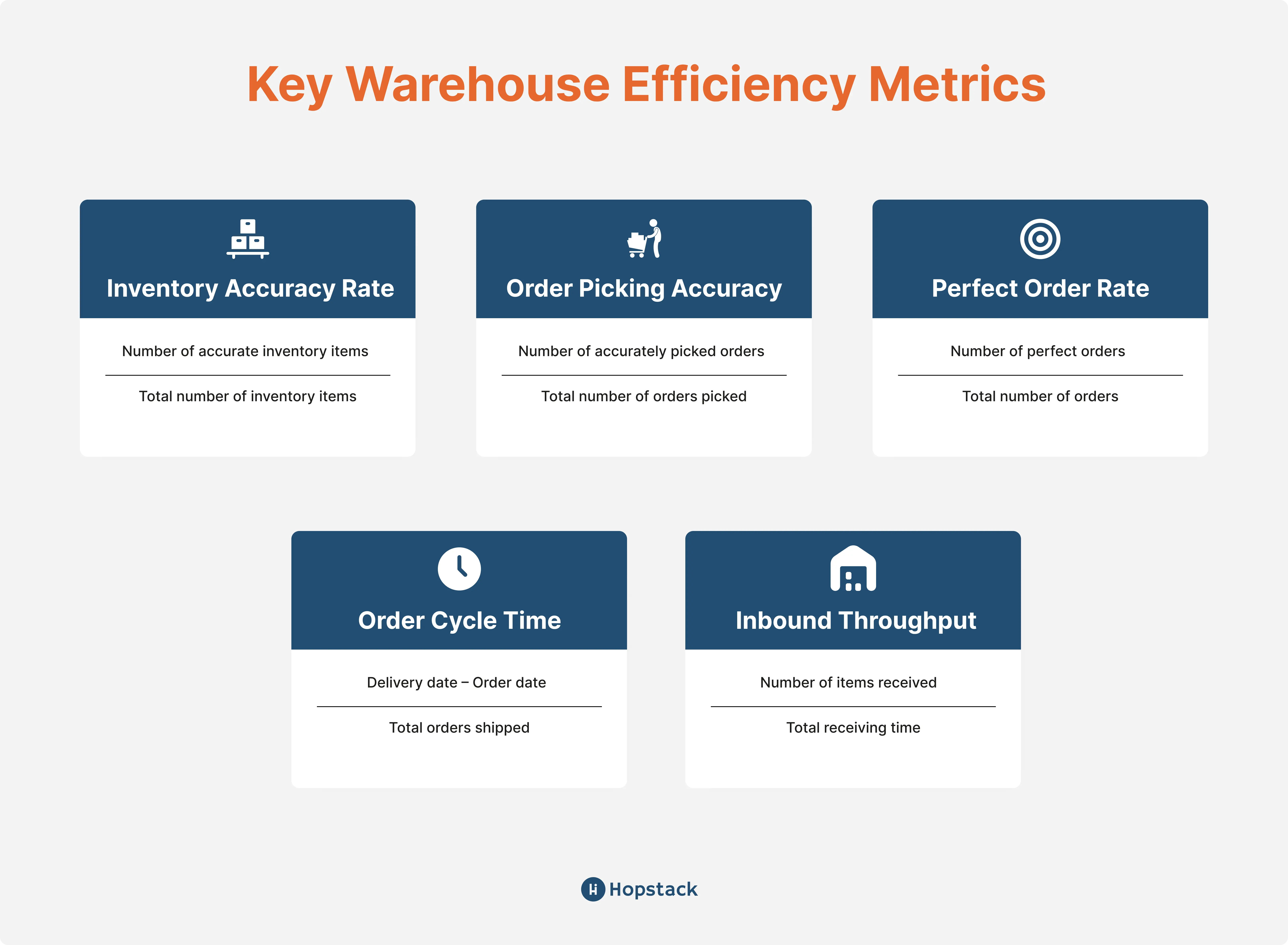
20 Tips and Strategies to Improve Warehouse Efficiency
Incremental improvements can go a long way in improving warehouse efficiency. Below are some common warehouse efficiency tips and strategies:
1. Optimize Warehouse Layout
Warehouses should prioritize making the most out of the warehouse layout to maximize space and improve floor productivity across the facility. Consider the following:
- Reconfigure the warehouse layout to minimize travel time and improve accessibility.
- Utilize techniques such as ABC analysis to categorize inventory based on the frequency of use and place high-demand items closer to shipping areas.
- Implement a logical flow design to streamline the movement of goods, minimize backtracking, and ensure smooth movement throughout the warehouse.
- Use a combination of warehouse slotting and shelving systems to plan your layout according to SKU number, product type, and characteristics.
2. Implement Lean Warehouse Practices
The lean revolution is all about delivering maximum value by focusing exclusively on essential processes, services, and resources. In the logistics industry, warehouses can embrace lean principles to eliminate waste, enhance workflow, and optimize resource utilization. Utilize techniques like 5S (Sort, Set in order, Shine, Standardize, Sustain) to organize workspaces and improve efficiency.
3. Use an Effective Warehouse Labeling System
Establish a comprehensive labeling system based on industry standards — warehouse labeling facilitates accurate inventory tracking and helps workers navigate the floor safely and easily.
Utilize barcode scanners or RFID technology for fast and error-free identification of items. Implement clear signage and labeling for aisles, racks, and storage locations to aid navigation and reduce picking errors. Ensure the labels are clear, consistent, and standardized for all products, locations, and equipment.
4. Streamline Order Picking Process
Optimize order picking processes based on the nature of products and order volume.
- Wave picking: Group multiple orders into "waves" to be picked at once, reducing travel time and picking errors.
- Waveless picking: Pick items for a single order at a time, ideal for low-volume warehouses or high-value items.
- Small batch picking: Pick smaller batches of items more frequently, reducing congestion in picking aisles.
- Zone picking: Assign specific zones to pickers, improving efficiency and reducing travel time.
- Discrete picking: Pick entire orders or specific items based on order requirements.
Leverage technology solutions like pick-to-light or voice picking to enhance accuracy and efficiency. Continuously evaluate and refine picking methods to minimize errors and maximize throughput.
5. Digitize Warehouse Management with a WMS
Implement a warehouse management system (WMS) to automate and optimize warehouse efficiency for critical operations such as inventory management, order processing, and labor allocation. A WMS positions businesses to take advantage of new and developing technologies and scale their operations accordingly. With machine learning, businesses can improve the accuracy of demand forecasting systems and spend less on inventory.
According to a survey by Supply Chain Management Review, an estimated 72 percent of respondents believe a WMS to be the software of choice within the industry. You can chalk this up to features such as real-time inventory tracking, automated replenishment, and task prioritization that directly contribute to streamlining operational workflows and improving warehousing efficiency.
Warehouse management systems provide real-time data into operational metrics to empower data-driven decision-making for continuous improvement of existing workflows and processes.
6. Increase Labor Productivity
Enhance labor productivity by providing adequate training, tools, and incentives. Labor makes up a significant chunk of any warehouse’s expenses — businesses should try and support the laborers to increase productivity.
Measure performance metrics such as:
- Key labor productivity KPIs include pick rate (orders picked per hour), dwell time (time spent non-picking), and utilization rate (percentage of time spent picking).
- Analyzing these KPIs helps identify areas for improvement, such as optimizing picking routes, providing better training, or providing ergonomic equipment.
- Increased labor productivity directly translates to higher throughput, lower fulfillment costs, and improved profitability for the warehouse.
7. Monitor Data and Analytics
Leverage data analytics tools to monitor key warehouse metrics such as inventory turnover, order accuracy, and cycle time. Increasing warehouse efficiency is a process, and regular monitoring will help you continuously tweak and adjust your existing workflow for incremental improvements.
Analyze trends and identify areas where performance is lagging to adjust strategies as per business needs. For example, analyze historical sales data to forecast demand accurately and optimize inventory levels, reducing stockouts and excess inventory costs.
8. Utilize Cross-Docking
Implement cross-docking strategies for warehouse storage efficiency — cross-docking enables businesses to bypass storage and directly transfer incoming goods to outgoing shipments. This tip is more relevant for warehouses that process high-volume, fast-moving goods and can benefit from reducing storage costs and expediting order fulfillment.
9. Invest in Automation
Consider automation wherever possible to increase efficiency, reduce labor costs, and improve accuracy in high-volume warehouses. G2 estimates the global warehouse automation market will surpass $ 30 billion by 2026.
Automate the internal flow of goods with the right technology — tools such as conveyor systems, electric monorails robotic picking systems, and automated guided vehicles (AGVs) streamline material handling processes, minimize manual labor, reduce errors, and increase throughput.
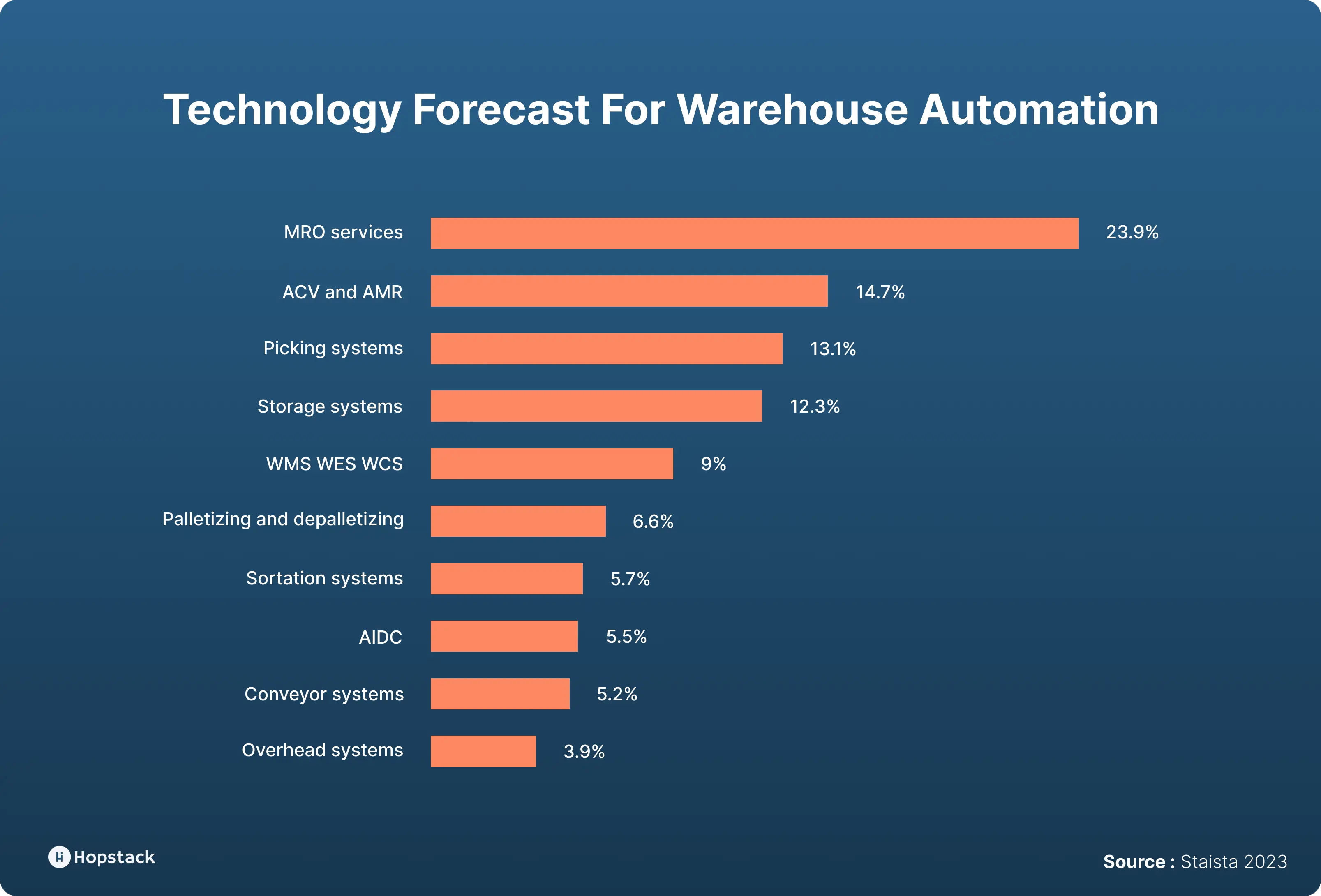
10. Invest in Ergonomic Equipment
Provide your employees with ergonomically designed workstations, tools, and lifting equipment to reduce fatigue and injuries. A healthy and comfortable workforce can be more productive and contribute to a safer work environment.
Prioritizing worker comfort and safety can, in turn, lead to lower attrition and help retain a highly specialized workforce that can perform at higher efficiencies.
11. Implement Slotting Optimization
As a warehouse efficiency tip, slotting strategies involve carefully analyzing product characteristics, demand patterns, and storage space layout for maximum warehouse storage efficiency. Warehouse managers can consider factors like size, weight, and demand frequency to effectively minimize travel time and maximize storage density.
For example, consider lightweight and frequently picked items — these products should ideally be placed near the picking areas to minimize travel time for warehouse staff. Conversely, heavier items must be placed closer to receiving areas or near material handling equipment to reduce the effort required for transportation.
12. Utilize Cubic Space
Apart from square footage, warehouses can extract a lot of mileage from the cubic space itself to accommodate inventory growth without expanding the physical footprint of the facility. Some strategies to utilize cubic space include:
- Double-Deep Racking: Double-deep racking involves placing pallets or storage units two deep within a rack structure, effectively doubling the storage density compared to traditional single-deep racking systems.
- Mezzanine Floors: Mezzanine floors provide additional storage space by utilizing the vertical space above existing floor areas. Mezzanines can be customized to accommodate various storage needs, including shelving systems, conveyor lines, or even office spaces.
- Automated Vertical Lift Modules (VLMs): VLMs are automated storage systems that utilize vertical height to store and retrieve items efficiently. By storing items vertically and retrieving them with precision, VLMs maximize storage density while minimizing the footprint required for warehouse storage efficiency.
13. Establish Quality Control Procedures
Implement rigorous quality control procedures to ensure the accuracy and condition of inbound and outbound shipments, reducing errors, returns, and customer dissatisfaction. There should be checks and measures in place to thoroughly inspect and verify the quantity, condition, and accuracy of the received goods.
Before shipping orders to customers, establish checklists and inspection protocols to perform final quality checks and ensure that the correct items are picked, packed, and prepared for dispatch.
Your warehouse managers should continuously review and analyze quality control data to identify trends, recurring issues, or areas for improvement. Try and implement a feedback loop extending from warehouse staff and suppliers to customers to identify potential quality issues and implement corrective actions. A centralized warehouse management system can take a lot of pain out of designing and implementing stringent quality control processes, tracking performance metrics, and facilitating continuous improvement.
14. Implement Demand Forecasting
Utilize demand forecasting techniques based on historical data, market trends, and seasonality to anticipate future demand. A WMS can analyze historical sales data to identify patterns and trends, such as peak seasons, product preferences, and demand variability, and adjust inventory levels accordingly. External factors such as economic indicators, industry developments, and competitor activities provide warehouses with valuable context to anticipate shifts in demand and adjust their inventory strategies proactively.
For example, retailers may experience increased demand for holiday-related products during festive seasons, while seasonal weather changes may impact the demand for certain goods. Seasonality adjustments enable warehouses to maintain the right inventory levels to meet customer demand during peak periods without overstocking or risking stockouts during slower periods.
15. Opt for Just-in-Time (JIT) Inventory
Just-in-time (JIT) inventory management practices strategically synchronize inventory levels with actual demand to minimize excess inventory holding costs, mitigate stock obsolescence, and optimize cash flow. JIT principles enable warehouses to procure and stock inventory only when it is needed, thereby reducing the need for excess inventory storage and associated holding costs.
An important point to remember here is that JIT inventory management requires businesses to maintain close relationships with suppliers to facilitate timely deliveries of goods in line with production schedules or customer orders. While this approach minimizes the need for warehouses to maintain large inventories on-site to replenish goods as needed, it increases dependency on third parties.
16. Utilize Cross-functional Teams
Collaboration between departments such as sales, procurement, and logistics helps break down silos and encourages cross-functional teamwork to meet customer needs. Sales teams, for instance, provide valuable insights into customer demand and market trends, which can inform procurement decisions and inventory planning.
By working closely with procurement teams, sales can communicate customer preferences and demand forecasts, enabling procurement to procure the right products in the right quantities and at the right time. With cross-functional alignment, businesses can improve warehouse efficiency as a whole to meet customer demand more aggressively.
17. Implement Vendor-managed Inventory (VMI)
Consider partnering with suppliers to implement vendor-managed inventory (VMI) programs — it's a strategic approach where suppliers are responsible for monitoring and replenishing inventory levels at the warehouse or retail location.
Businesses can share inventory data from a WMS and collaborate closely with the suppliers to align their interests and objectives. Suppliers gain insights into customer demand trends and preferences to adjust production schedules and inventory levels. In return, warehouses can rely on timely replenishment of stock, reduced administrative burden, and improved overall inventory management efficiency.
18. Implement Multi-channel Fulfillment
Depending on your business model, optimizing order fulfillment processes to accommodate multiple sales channels, including e-commerce, retail, and wholesale, can help strategically improve warehouse efficiency and reduce costs. Consider consolidating orders across various sales channels to streamline operations and minimize handling.
Businesses can integrate modern order management systems or end-to-end warehouse management systems to enable operators to aggregate orders from different sales channels into a single platform. A consolidated approach eliminates the need for separate handling of orders from various channels, reducing the risk of errors, duplication, and delays in order processing.
19. Implement Performance Incentives
Ultimately, technology in the warehouse must work in harmony with the warehouse workers. Implementing performance-based incentive programs can motivate and reward employees to achieve productivity targets, and nurture a culture of excellence and continuous improvement within the warehouse. Align employee incentives with warehouse efficiency KPIs such as order accuracy, picking speed, and inventory turnover to incentivize continuous improvement and skill development.
20. Utilize Real-Time Location Systems (RTLS)
Real-time location systems (RTLS) use RFID or Bluetooth beacons to track the real-time location of inventory and assets within the facility. RFID tags or Bluetooth beacons attached to inventory items, pallets, or assets emit signals that are picked up by receivers strategically placed throughout the warehouse to provide real-time visibility into the location and movement of items.
With RTLS technology in place, warehouses can take inventory management and warehouse efficiency one step further — it provides an additional layer of visibility to reduce the risk of errors, loss, or theft and supports just-in-time replenishment and inventory optimization.
Achieve Superior Warehouse Efficiency with Hopstack
Hopstack's warehouse management system (WMS) offers a comprehensive solution designed to streamline and optimize every step of the warehousing process. From inbound receiving and putaway to inventory synchronization and order fulfillment,
Hopstack's WMS software empowers warehouse managers to enhance efficiency and accuracy with features such as algorithmic ABC analysis for optimal inventory placement, automated back-order generation, and intelligent order fulfillment algorithms. We can configure our WMS with tailor-made workflows to suit specific warehouse networks and facilities, while integration with various hardware devices further enhances efficiency and accuracy.
Schedule a demo today to experience how Hopstack's WMS can transform your warehouse operations.