Managing prep activity across multiple merchants while being Amazon compliant, driving cost and fulfillment efficiency, and ensuring no errors in operations is a challenge faced by all Prep Centers.
Prep Centers often have to deal with manual errors in labeling, prepping, packing, and exception handling that result in poor fulfillment speed and unhappy merchants/clients. Compliance errors can lead to penalties from Amazon, and/or returns, thus adding to the operating costs of the Prep Centers.
Most Common Errors in FBA Fulfillment Operations
Amazon has strict guidelines on Prepping and Packing individual units in boxes and in pallets to be shipped to an Amazon fulfillment center. Most of the Prep Centers face manual error challenges during these two steps of the FBA fulfillment lifecycle.
Prepping Errors
Most common errors at Prepping include: (a) improper prepping materials used (for products such as sharp items, liquids, etc. (b) prepping of exceptions including HAZMAT products, (c) incorrect FNSKU labels, or (d) FNSKU labels missing information such as expiration date. Most of these errors are driven by factors including incomplete or incorrect prep instructions, manual matching, and printing of the products and labels, respectively, or not complying with Amazon prep requirements.
Packing Errors
Common errors during packing include: (a) a mismatch between the actual number of units, boxes, and pallets and as specified in the Shipping Plan, (b) incorrect measurement and reporting of weights and dimensions of small parcels and pallets (for example Amazon typically sets an upper limit on weight for its partner carriers, for Small-parcel-delivery (SPD), weight upper limit is 50lb and for Less-than-truckload (LTL), the pallet weight should be in the range of 150-1500lb), or (c) manual errors involved incorrect labeling of items packed in cartons or pallets.
Labeling Errors
Labeling is a critical activity at all stages of outbound FBA fulfillment. Incorrect print, match, and/or placement of the labels is the primary driver of labeling errors. Amazon has strict compliance rules for label information and placement, For example, an FNSKU label should cover the UPC. Some of the labeling errors during the outbound prepping and packing processes are mentioned in the above sections.
How Hopstack Helps Prep Centers with Error Reduction
Hopstack’s platform helps Prep Centers digitize, automate, and optimize inbound storage and outbound operations end-to-end. Right from onboarding merchants, creating inbound orders, receiving, and putaway to generating shipping plans, order batching, picking, prepping, packing, and shipping.
Prep Centers can thus get rid of any spreadsheet-based processes and/or manual record-keeping for their operations, which in turn leads to improved fulfillment efficiency, manual error reduction, and lower operational costs.
Automated Prepping Instructions for the Prep Associate
Hopstack ensures accurate and clear prepping instructions for the prep associate depending upon Amazon’s product-specific guidelines, merchant requirements, and other business rules.
Hopstack synchronizes product class-specific (liquids, fragile, apparel, etc.) prepping guidelines from the Amazon Seller API. Alternatively, Hopstack also empowers Prep Centers and merchants to add product-specific additional prep instructions and unique guideline notes to the prepper.
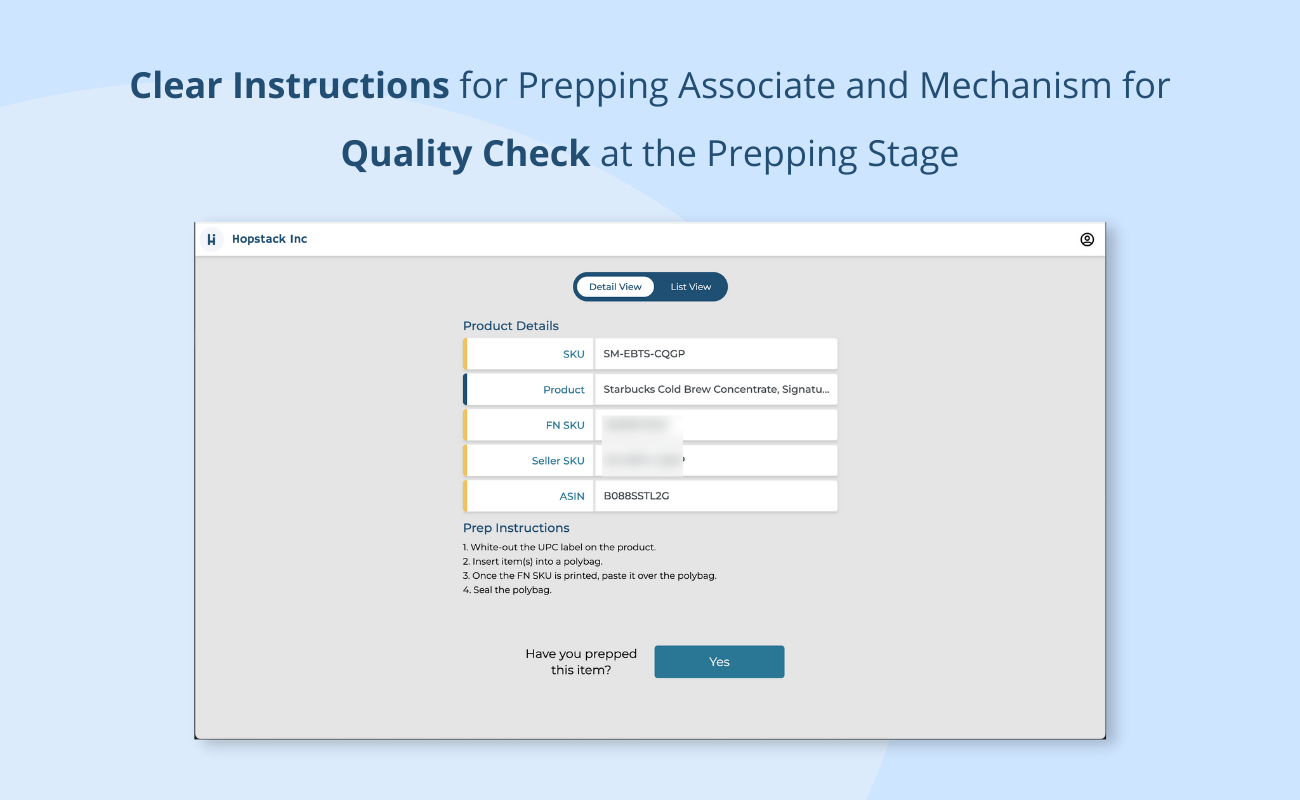
Weight and Dimensions Compliance
Hopstack ensures that every box, case, or pallet leaving a Prep Center complies with Amazon’s requirements for dimensional accuracy and weight limits.
The platform allows Prep Center operators to measure and/or define the box and pallet weights and sizes as a part of the packing process. Hopstack also recommends the appropriate size based on product type, dimensions, and other factors.
Hopstack’s plug-and-play integrations with dimensioning tools and weight scales such as FreightSnap, Cubiscan, and Dymo ensure that the box and pallet weight does not exceed or fall under the prescribed thresholds. Wherever the box/pallet weight falls outside of the limits, the platform automatically notifies the packer and recommends the addition of a new box or pallet to continue packing, as applicable.
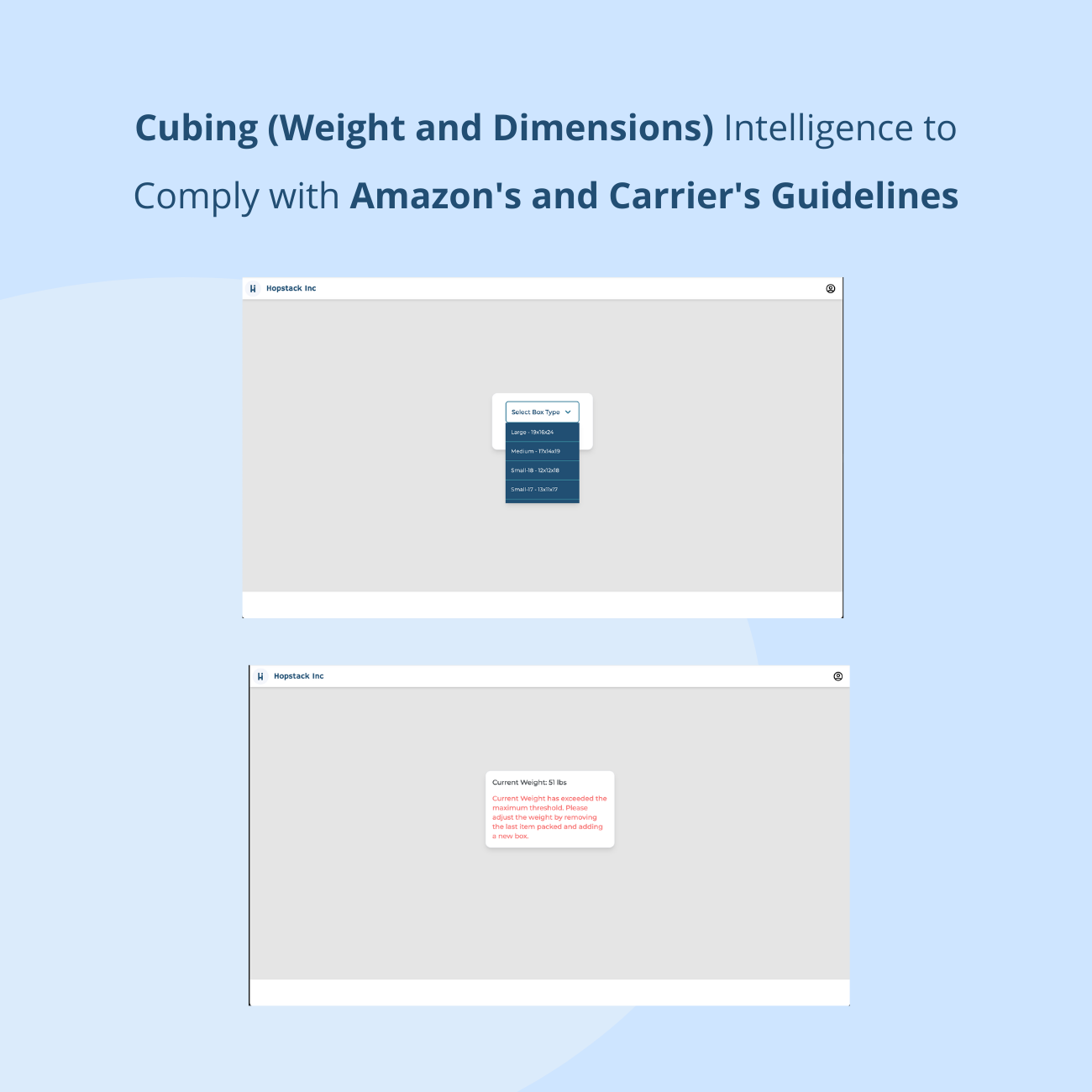
Automated Label Generation and Printing
Hopstack automates the process of label generation and printing at every stage of the fulfillment process.
At the prepping stage, Hopstack automatically retrieves the FNSKU label from the merchant’s/ client’s Amazon Seller Central and prints it using pre-built plug-and-play thermal printer integrations in Hopstack’s platform (such as Rollo, Zebra, etc.).
At packing, Hopstack automatically generates the shipping manifest and prints the necessary box/pallet and shipping labels.
These automations significantly reduce manual labeling errors and eliminate compliance errors during the outbound order fulfillment processes.
UPC-mismatch correction using License Plate Number (LPN)
More than often, there are mismatches between the UPC on the product and the UPC on the merchant’s Amazon Seller Central account. Hopstack’s customers have an option of generating their own LPN on Hopstack which then links the UPC code on the product to the UPC on the Seller Central within the Hopstack platform (Hopstack maintains this linkage for future inbound and outbound of the same product) to address this issue.
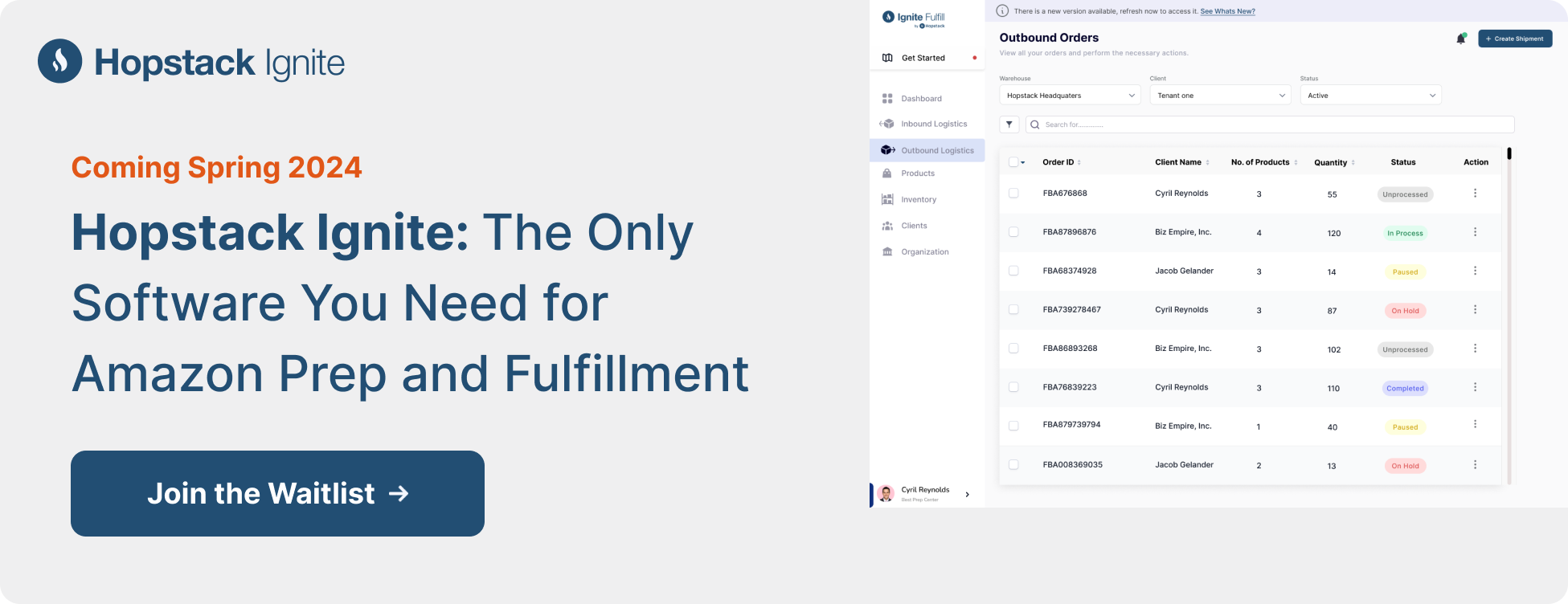
Bottom Line
Hopstack’s automation and digitization-first approach to managing prep operations has helped Prep Centers cut errors significantly. Most of Hopstack’s customers have noticed their outbound fulfillment errors drop close to 0% within two months of using the platform.
By minimizing errors in inbound, storage, and outbound activities, Prep Centers have been able to attain high fulfillment and cost efficiency, better resource utilization, and better merchant experience.
The platform has also helped Prep Centers improve average fulfillment throughput by > 111%, Prep > 350 line items per hour, and cut average space utilization to 47%.
Schedule a demo to learn more about how Hopstack can help transform your Prep Center operations!