According to McKinsey, e-commerce sales have increased more than 160 percent from 2014 to 2019, creating a $600 billion opportunity for businesses in the process. In the e-commerce sector, order fulfillment is one of the most important metrics when it comes to improving customer churn rate and brand loyalty.
However, in these densely populated sectors where every little bit matters, order fulfillment can become a strategic differentiator for your business to build customer loyalty through exceptional service.
Order fulfillment is one of the final stages of the customer purchasing journey; it begins when the customer places an order and concludes with the safe delivery of the product. It takes a combination of multiple processes to pull off effectively, namely picking, packing, and shipping. In instances when the customer wishes to return the product, it covers that aspect of the interaction as well.
Taking into account the overall impact of order fulfillment on warehousing and logistics operations, this article is going to share some best practices to reduce errors and improve accuracy in the overall process.
Common Errors During Order Fulfillment
The challenges of order fulfillment increase by orders of magnitude depending on the volume of orders being processed by your business on a day-to-day basis. However, it’s not simply a matter of picking and packing the right products and shipping them with the right labels. Speed and cost optimization are essential parts of the equation, with McKinsey reporting that more than 90 percent of online shoppers in the US expect free delivery within two to three days. Businesses struggle to balance these finer aspects of order fulfillment and end up making some common errors that damage their brands’ reputations in the long run.
Picking Incorrect or Damaged Orders
Picking the wrong product is one of the primary culprits when it comes to fulfillment errors. It can happen because of multiple reasons; human error, incorrect product description, incorrect order recording, and more. Errors can occur despite our best efforts and using automated order fulfillment systems can curb these errors to a large extent.
Delivering incorrect or damaged orders can quickly result in a lot of unhappy customers, product returns, and negative reviews. Approximately 23 percent of return orders are due to the delivery of incorrect items. Such a high number is alarming and businesses should prioritize the reduction of incorrect or damaged orders as much as possible.
Poor Inventory Management
Mismanaged inventory can result in misplaced products, unexpected delays, stockouts, and shipping hindrances. With advancements in embedded sensors and IoT devices, modern warehouse management systems (WMS) can provide a high level of visibility into inventory operations to streamline the picking and packing of products on time and in full without delays or errors.
Inventory management is not only about accurate order fulfillment but improving stocking operations to avoid out-of-stock or overstocking instances. Mismanaged inventory can further lead to inconsistent on-shelf availability and high inventory costs.
Inadequate Warehousing Capacity
To meet the accelerated delivery demands of today’s customers, having enough warehouse capacity is a must. In addition, the warehouse layout and space management is essential to optimize picking and packing operations by the warehouse workers.
Without real-time data on order volumes and current stock, the warehouse managers will lack the visibility needed to optimize the placement of high-volume products, save space for buffer stock or adapt to sudden excess demand.
Lack of Automation
While manual order management and fulfillment can be reasonable for businesses starting out, automation becomes a necessity as the volume of orders begins to grow over time. People make mistakes, and your order accuracy will continue to plummet with the more people you bring on board.
A persistent lack of automation in warehousing operations will inevitably result in incorrect or delayed order fulfillment because of unexpected complications at various stages of the pipeline.
Failure to Account For Customer Returns
According to Invesp, approximately 90 percent of customers are likely to place a repeat order if the return process is simple, while 67 percent of consumers check the return policy before making a purchase. In today’s e-commerce climate, the consumer is king and not having a clearly defined return policy with reverse logistics is a recipe for disaster.
The customers’ demands are continuously changing, and how you handle product returns is going to define how consumers interact with your business going forward. According to the National Retail Federation, returns account for $816 billion in lost sales; therefore failure to account for it can lead to operational and financial issues.
Best Practices for Error Reduction During the Picking Process
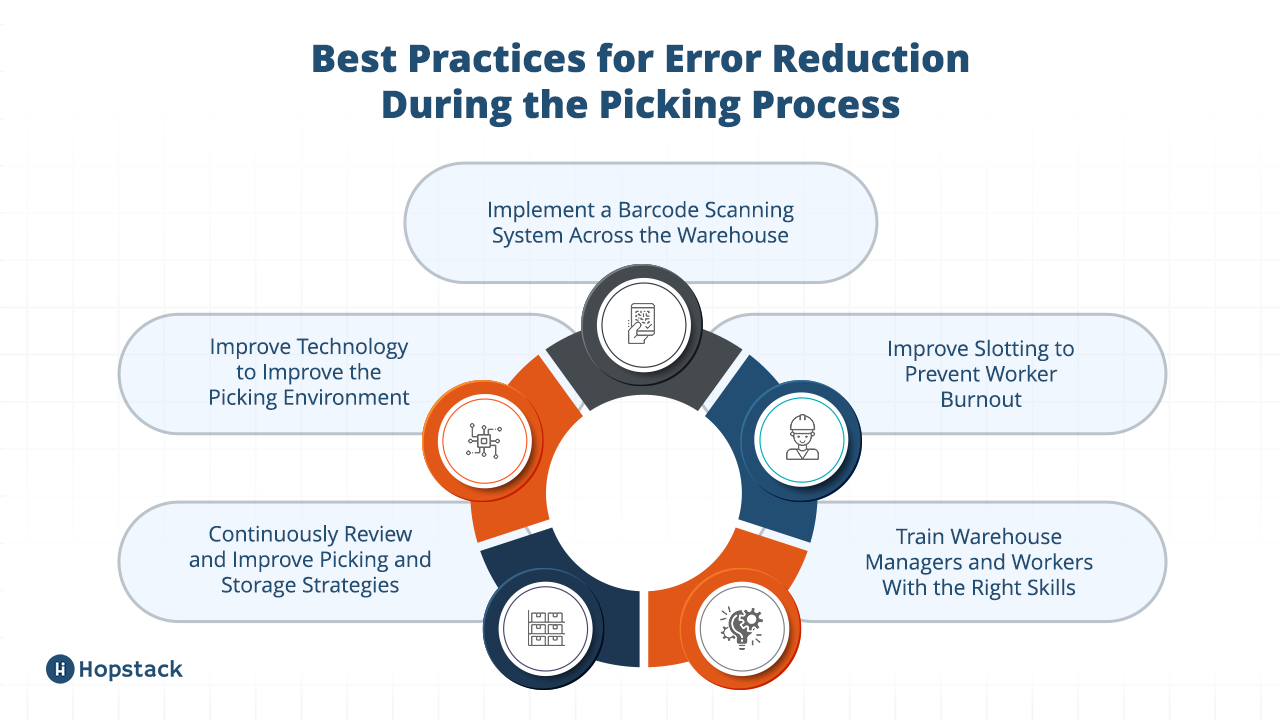
Most warehouses operate with an error rate of 1-3 percent during the picking process. However, a warehouse with an accuracy rate of 97 percent will incur losses bordering on unacceptable, especially for businesses processing large volumes of orders. Therefore, we have prepared a list of best practices to reduce errors during the picking process.
1. Implement a Barcode Scanning System Across the Warehouse
A barcode scanning system can drastically reduce fulfillment errors by electronically transmitting data tied to SKUs or purchase orders. Automated data entry limits the room for errors, enabling your floor workers to function at peak efficiency. When compared to manual processes, barcode scanning allows for faster and more accurate QC with near-instantaneous product identification and verification. In addition, they enhance visibility into item locations and inventory levels, further streamlining pickup tasks for the workers.
However, as a standalone capability, barcode scanning systems aren’t as effective and must be used in combination with ERP software or WMS. Barcode scanners have become an industry standard to empower warehouse managers with the visibility needed to take control of floor operations.
2. Improve Technology to Improve the Picking Environment
Assist the warehouse managers and workers as much as possible with their day-to-day activities. This can be accomplished in a number of ways:
- Pick-to-light and voice-picking systems: Pick-to-light and voice-picking systems guide the workers to the products that need to be picked once they scan the barcode on a shipping carton. Visual or auditory guidance delivered in this way significantly increases the speed and accuracy during the picking process.
- Improve document accessibility: Ensure any documents like labels, SKUs and more have a font style and size that is easily readable and accessible to all warehouse workers.
- Create smart pick lists: Integration with a WMS can help you prepare smart picklists using data-driven algorithms and optimization techniques. Smart picklists are essentially intelligent picking orders prepared for your floor workers to minimize pick time and distance travelled. It accounts for warehouse layout, order grouping, order importance, shipping deadlines, slotting characteristics, customer preferences and more to optimize the pick-path and streamline picking processes as much as possible.
3. Improve Slotting to Prevent Worker Burnout
Improvements to the warehouse layout, slotting routine, and picking regimen can go a long way towards reducing the physical and mental strain on the floor workers. There are multiple ways to approach slotting improvements in a warehouse:
- Slot items based on their pick rates or sales velocity, where faster moving items should be more accessible than slower moving products
- Adopt an ergonomic approach to product slotting to minimize instances where pickers have to reach, climb or bend
- Review and update present slotting practices to look for areas of improvement. Take feedback from warehouse managers and workers into account.
- Implement autonomous mobile robots (AMRs) to help floor workers find the fastest routes to the products to be picked
You can also organize orders into batches and zones to pick items for multiple orders simultaneously before bringing them to the packaging area. This practice greatly reduces travel time and increases worker productivity.
4. Continuously Review and Improve Picking and Storage Strategies
Regularly review warehouse storage strategies and compare alignment with the latest consumer trends. Verify if the high velocity and most picked products are stored in the most accessible locations, close to the picking lanes. Use standardized identification and labeling systems for the products, including rack labels, aisle markers, discernable packaging, and unique SKUs.
Perform routine inventory checks to keep tabs on item placement throughout the warehouse. Products being on the wrong shelves can confuse floor workers at times, leading to avoidable errors. Regular checks can also help floor managers identify potential opportunities to improve the warehouse layout and inventory planning processes.
5. Train Warehouse Managers and Workers With the Right Skills
At the end of the day, for smarter and leaner warehouse operations, technology and workers need to be able to work side-by-side. Therefore, warehouse leaders need to provide warehouse managers and workers with the appropriate training necessary to operate intelligent machinery and skillfully interact with machine interfaces without errors.
To a large extent, error reduction in the picking process comes down to leveraging the right technology to optimize the manual tasks carried out by the pickers.
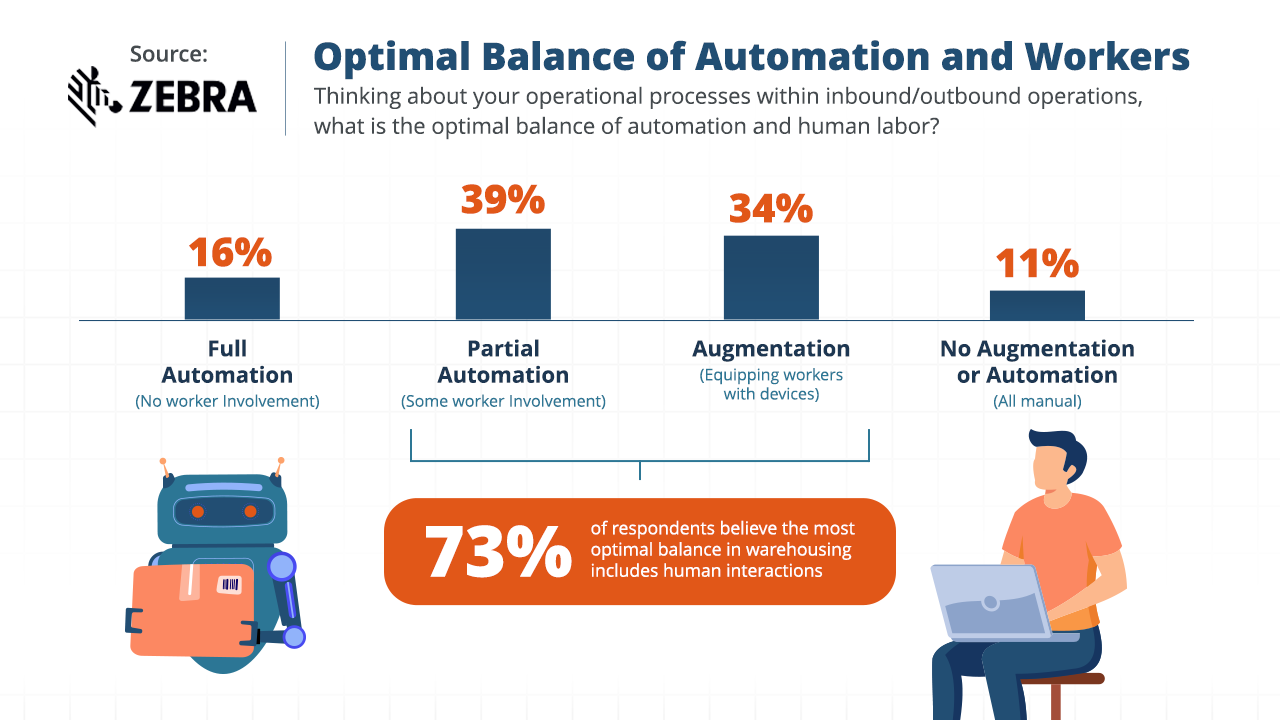
Best Practices for Error Reduction During the Packing Process
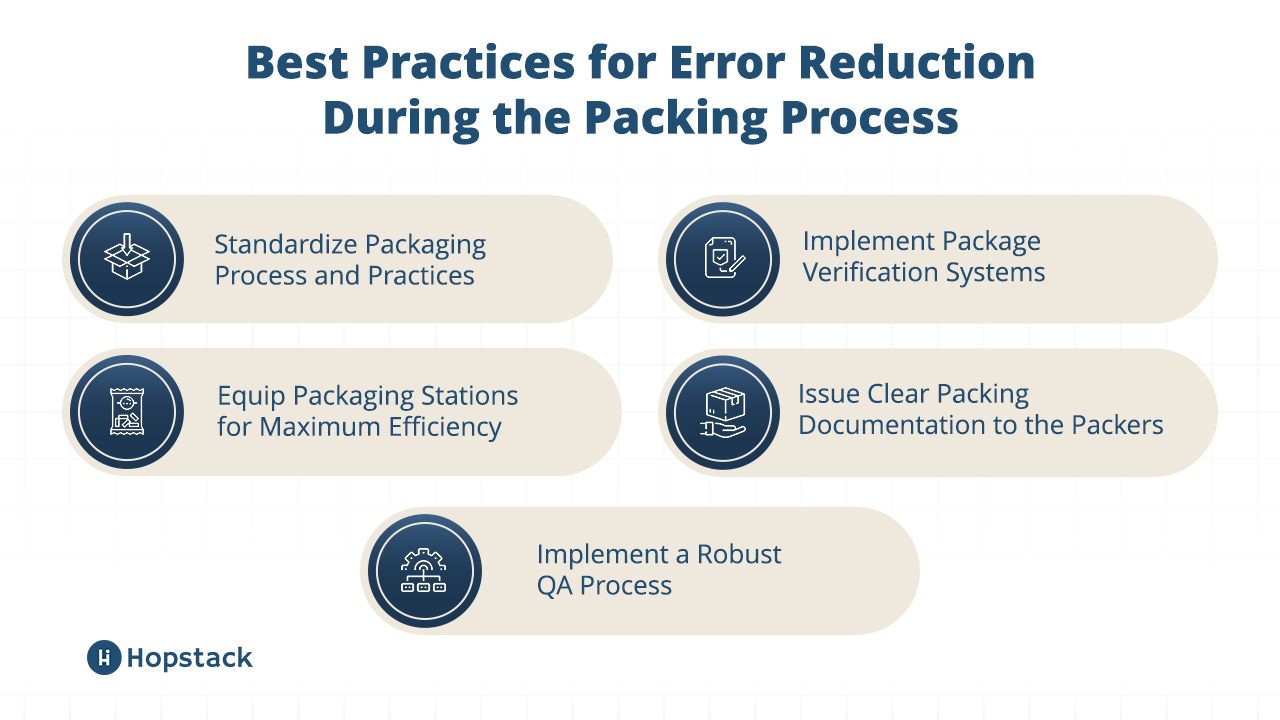
Apart from the picking stage, most of the errors during the order fulfillment process take place during the packing stage of the pipeline. Let’s discuss five best practices to improve order accuracy during the packing process.
1. Standardize Packaging Process and Practices
Establish standardized materials and processes to streamline the process for the packing floor workers. Clear guidelines for packing specific product types can help with package identification, packing consistency, and the use of appropriate materials to prevent any damage to the products during transit.
2. Implement Package Verification Systems
A barcode scanner or a weight-based verification system can verify the contents of any package. It’s one of the easiest ways to identify and correct packing errors prior to the shipping stage.
3. Equip Packaging Stations for Maximum Efficiency
Packaging stations are the heart of the warehouse packing process and usually have a lot of room for optimization and quality of life (QOL) changes. In order to increase productivity and reduce employee burnout, the packaging stations need to have proper lighting, ergonomic layout, adjustable surfaces, and access to any and all relevant tools like bubble wrap, label printers, box cutters, and more.
A first in, first out (FIFO) system is standard in most packaging stations to clear the older inventory first, maintain product quality and reduce the wastage of date-restricted items.
4. Issue Clear Packing Documentation to the Packers
Verify any and all packing and shipping documentation issued to the floor workers to prevent instances of shipping errors. This includes packing slips, shipping labels, delivery instructions, and more.
5. Implement a Robust QA Process
A consistent and robust quality assurance process, applied at various stages of the packing process, can introduce a proactive approach to identifying and remedying errors. While the exact workflow will differ from warehouse to warehouse and depend on the warehouse managers themselves, it should include
- Clear objective and scope
- Inspection criteria
- KPIs
- Timeline
A top-down culture of quality can help significantly reduce errors during the packing process. Conduct regular audits to identify areas of improvement within the current workflow and maintain internal quality standards.
6. Leverage Automation to Streamline Operations
Fulfillment automation can significantly empower your packers and streamline the packing process by reducing manual labor. While automation is a broad term, it is widely used at various phases of the packing process to improve speed, accuracy and consistency while maintaining operational scalability. Some common approaches are:
- Automated packing machines can automatically pack products into the relevant boxes, reducing the need for human intervention
- Automated labelling systems can automatically print and attach labels to the appropriate packages with more consistency and accuracy
- Conveyor systems can automatically move products and packages throughout the packing process, reducing instances of lost, damaged or stolen products
- Warehouse managers can generate consistent packing instructions for particular product types
The Role of a Warehouse Management System (WMS) In Error Reduction
A warehouse management system (WMS) is an essential part of managing warehouse operations for outbound delivery. To understand why it’s an irreplaceable part of today’s supercharged, omnichannel e-commerce economy, let us first understand what a WMS is.
Definition:
A warehouse management system is a software platform that provides complete visibility into a business’s inventorying, warehousing, and distribution operations. It covers daily operations from the moment a product enters inventory till it has been safely delivered to the end customer. Most warehouse management systems come with built-in capabilities to optimize resource usage, picking and packing processes, space usage, routing, reporting and analytics, and more.
There are multiple benefits to having a WMS oversee warehousing and logistics operations over siloed, manual approaches or traditional OMS.
A WMS provides continuous visibility into logistics and warehousing operations which is essential for comparing KPIs for continuous improvement.
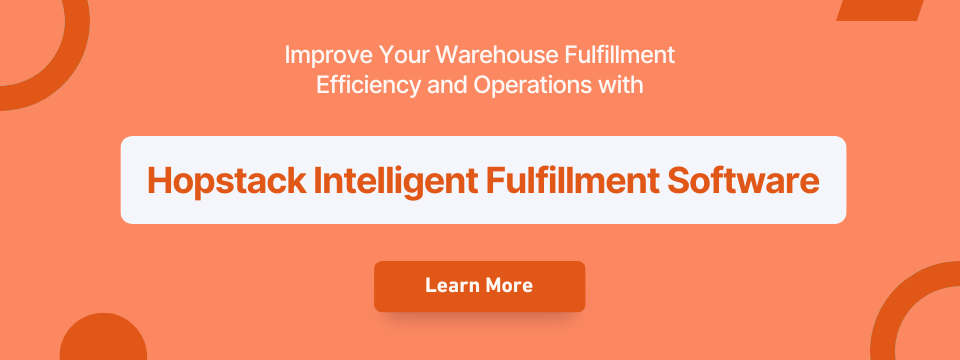
Leveraging Data and Analytics for Continuous Improvement
However, to make warehousing operations leaner and smarter with actionable insights, a WMS needs real-time data from various domains like shipping, picking and packing, order management, transportation, ERP systems, and more. Therefore, data integration is key to the success of a WMS in improving order fulfillment requirements.
The flow of information from these various data streams can then be used to monitor business-critical KPIs like:
- receiving efficiency
- picking accuracy
- inventory turnover
- backorder rate
Data analytics can further produce intelligent insights into how to improve the order fulfillment process through optimization of warehousing logistics like inventory management, workforce productivity, automation, product positioning, and shipment frequency.
A smart warehouse management system is essential to identify key areas for continuous improvement. Data and analytics can provide insights into demand forecasting, picking and packing errors, inventory optimization, workforce management, customer demographics, and resource utilization to streamline order fulfillment processes and operational expenses. With all the relevant data available in a centralized dashboard at the click of a button, a WMS is key to being data-driven in today’s fast-paced and extremely competitive e-commerce sector.
Bottom Line
Order fulfillment processes are at the heart of today’s warehousing and logistics operations. While an order accuracy rate of 100% is not achievable in the current retail climate, most successful distribution centers have an order accuracy rate of 99.5%.
Manual operations are simply not as effective when it comes to reducing fulfillment errors. A WMS can provide warehousing operations that deal with massive volumes of inventory with the data-driven insights necessary to improve order fulfillment efficiency with a high rate of success.