Warehouses do more than store goods—they're high-functioning systems that directly influence how fast and accurately products move through the supply chain. In fact, studies show that inefficient warehouse operations can account for up to 30% of total order cycle time. On the flip side, companies with streamlined warehouse processes report up to 25% faster order fulfillment.
But what exactly goes on inside a warehouse? And how do these processes quietly shape the success (or failure) of businesses?
This guide breaks down the 12 core warehouse processes—from inbound receiving to outbound dispatch—and shows how each one can be optimized to eliminate delays, cut errors, and improve flow. If you're involved in operations, logistics, or supply chain strategy, this is where meaningful gains begin.
What is Warehousing Process?
The warehousing process refers to the coordinated steps involved in receiving, handling, storing, and dispatching goods within a warehouse. It’s not just about storage—it's about controlling the movement and condition of inventory from arrival to exit.
Far from being just a storage function, the warehousing process supports critical supply chain goals like inventory visibility, order accuracy, and timely order fulfillment. Whether it's a high-volume distribution center or a specialized facility, the effectiveness of these internal processes directly impacts delivery performance and customer satisfaction.
Smart warehousing can take place in a variety of settings: large distribution centers, micro-fulfillment hubs, or even integrated spaces within manufacturing plants. Regardless of the scale, the goal is the same: ensure goods are accessible, organized, and ready for accurate and timely dispatch.
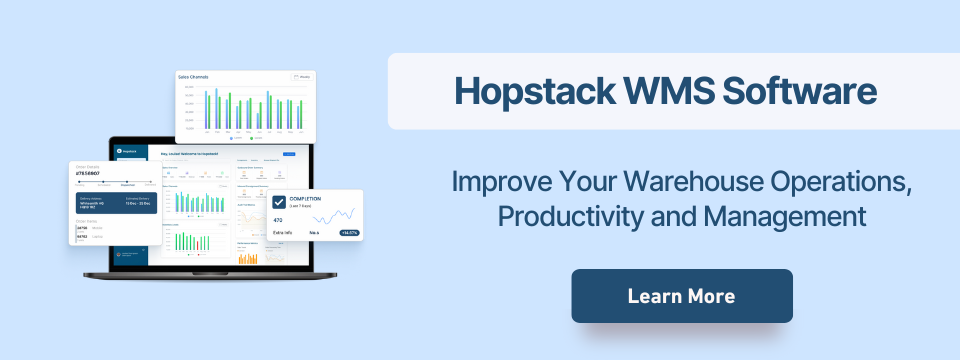
12 Key Warehouse Processes & How To Improve Them
Here we have listed the 12 most important warehousing processes to fulfill the orders efficiently and effectively and how you can optimize these warehouse processes.
1. Receiving
Warehouse receiving is the first step in the warehouse process workflow. It involves ensuring that all goods that have been ordered arrive in acceptable quality and quantity.
The warehouse receiving process entails delivering, unloading, and forwarding for storage of inventory in the warehouse. To ensure accuracy, a predetermined system can be used which will help track and compare what was received with what was originally ordered.
Having a well-defined and structured warehouse receiving process ensures stock count accuracy, lesser or no stockouts, and optimal inventory levels and storage. Flaws in the receiving process can lead to discrepancies in inventory records and actual inventory at hand causing issues and challenges in order fulfillment.
How To Improve Warehouse Receiving:
- Schedule inbound deliveries to optimize labor allocation and dock availability, reducing congestion and delays.
- Standardize inspection and counting protocols to ensure received goods match purchase orders and minimize discrepancies.
- Implement barcode scanners or RFID systems to accelerate data capture and reduce manual entry errors.
- Integrate a Warehouse Management System (WMS) for real-time inventory updates, automated alerts, and improved visibility across teams.
- Establish a structured exception handling process for damaged or missing goods, using digital tools for faster resolution and workflow continuity.
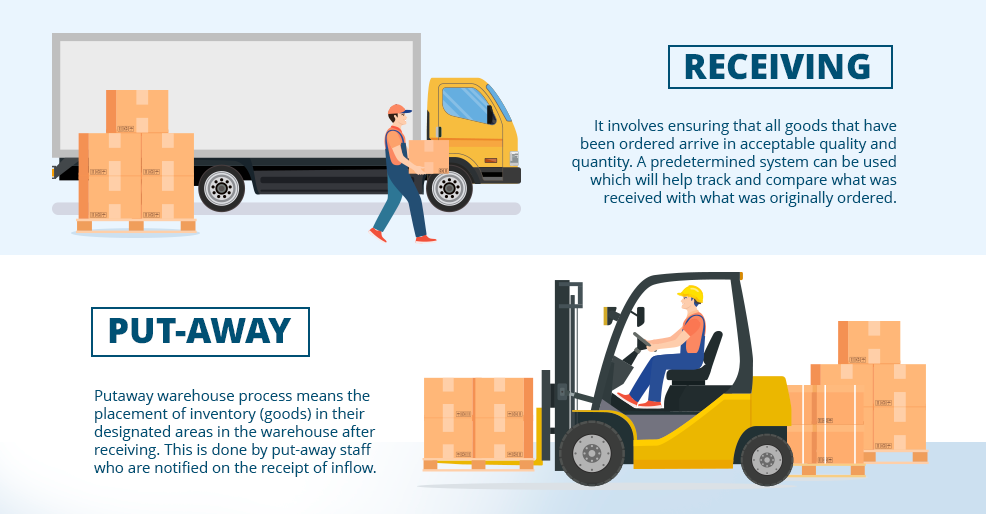
2. Put-Away
Putaway warehouse process is the second step which means the placement of inventory (goods) in their designated areas in the warehouse after receiving. This is done by put-away staff who are notified on the receipt of inflow.
An effective and efficient putaway process in warehouse helps your business by making the putaway easier for the next set of inventory batches. Also, it reduces the chances of inventory lost or misplacement.
Since your warehouse workflow becomes more organized and clean with a proper putaway process, it helps the picking process to become more seamless, quick, and easy, requiring lesser human and technological resources.
You can leverage different types of putaway methods like based on purchase orders or based on SKU or based on product types depending upon your business needs and orders. This leads to efficient use of storage space, cataloging, and prevents delays.
How to Improve the Putaway Process
- Use a Warehouse Management System (WMS) to automate putaway by directing staff to optimal storage locations based on real-time space utilization and item velocity.
- Leverage barcode or RFID technology to accelerate item identification, reduce manual entry errors, and confirm correct placement.
- Optimize warehouse layout by placing high-turnover items in easily accessible zones to minimize future retrieval time and travel distance.
- Implement a zone-based putaway strategy to enable multiple workers to operate simultaneously in designated areas, improving throughput and reducing bottlenecks.
It's crucial to standardize these processes to maintain consistency, reduce errors, and enhance overall warehouse productivity.
3. Picking
Picking is the warehouse process of selecting and collecting goods from the warehouse to fulfill a customer order. Order picking in a warehouse is one of the most labor intensive tasks and it constitutes to more than half of the warehouse operations cost.
Warehouse picking process directly impacts the customer satisfaction, business profitability, and brand image. Therefore, this warehousing process should be executed with accuracy and precision to make sure that the correct order and quantity of items reaches its destination on time.
Depending on the business, there are several picking methods such as batch picking, zone picking, wave picking, and more. You can choose the most appropriate picking method to reduce operational costs, enhance warehouse efficiency, boost customer satisfaction, and improve productivity.
How To Improve Warehouse Picking Process:
- Integrate autonomous mobile robots (AMRs) or automated guided vehicles (AGVs) to assist workers in picking multiple orders simultaneously, reducing manual effort and minimizing errors.
- Utilize a robust Warehouse Management System (WMS) to enable real-time inventory visibility, optimize picker routes, and support guided picking to reduce mis-picks and rework.
- Adopt picking assistance technologies, such as:
- Voice-directed systems for hands-free instructions via headsets
- Pick-to-light systems that illuminate item locations to improve speed and accuracy
- Apply efficient picking strategies:
- Batch picking to group multiple orders in one run
- Zone picking to assign workers to specific areas, minimizing travel and increasing throughput
Read More: Automated warehousing picking
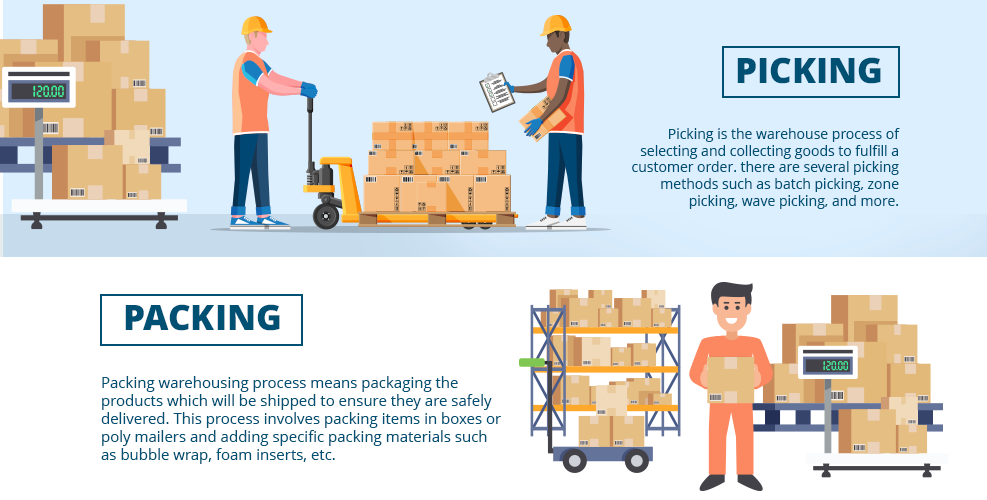
4. Packing
Packing warehousing process means packaging the products which will be shipped to ensure they are safely delivered. This process involves packing items in boxes or poly mailers and adding specific packing materials such as bubble wrap, foam inserts, etc.
Packing materials should be used judiciously so that the weight and size of packages remain within limits. Furthermore, items must also be labeled correctly with batch items and manufacturing codes using stickers.
There are numerous technologies that businesses need to invest in to make sure the proper packing guidelines are being followed as per Amazon or other marketplaces.
Having the right packing materials and procedures ensures that items reach undamaged to the customers. Packing can indirectly affect the customer satisfaction and brand reputation massively.
How To Improve Warehouse Packaging:
- Automated packaging systems can create right-sized custom-sized boxes for each order, reducing the need for additional filler material and decreasing package weight.
- Implement a robust package quality control system to inspect, identify and rectify packing errors before the package leaves the warehouse.
- Develop and enforce clear packing guidelines to standardize the process like specific instructions on how to pack certain items, use of packaging materials, etc.
- A culture of continuous improvement, where staff are encouraged to suggest improvements to the packing process, can help identify opportunities for efficiency gains.
5. Dispatching
The dispatch process in warehouse is the loading and sending of goods out of a warehouse. The dispatch warehouse process usually begins with picking the right goods for shipment. The warehouse manager needs to make sure that all items in an order are present and accounted for before dispatching it.
Once the items have been selected, they must be safely loaded onto delivery trucks or other transport vehicles. This requires proper coordination between different departments such as shipping, loading and inventory control.
After loading is complete, the driver needs to be given detailed instructions about their route and any special instructions relevant to the delivery.
Dispatch process requires effective communication with customers and drivers alike in order to ensure accurate and timely delivery of goods. Delays in dispatch can ultimately result in delays in delivery which is a negatively impacting element for your business and its growth.
How To Improve Warehouse Dispatch Process:
- Enable real-time scheduling and tracking of outbound shipments to improve coordination between packing, loading, and carrier departure.
- Use automation tools, such as conveyor systems or automated guided vehicles (AGVs), to accelerate the transfer of packed goods to dispatch zones and reduce manual handling.
- Integrate a Transportation Management System (TMS) for intelligent route optimization, carrier selection, and shipment consolidation—minimizing delivery times and logistics costs.
- Establish clear loading protocols and staging zones to avoid last-minute confusion and ensure timely departures.
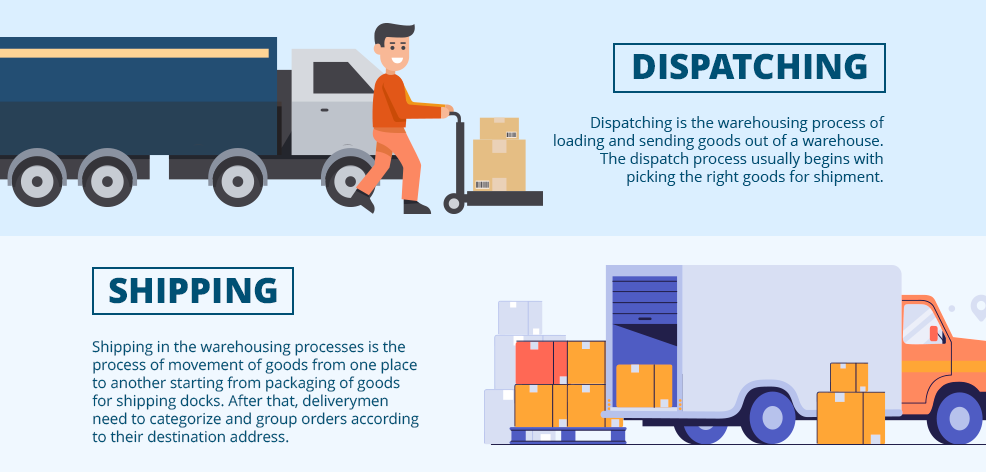
6. Shipping
Shipping is one of the final steps of warehousing processes. Shipping involves the movement of goods from the warehouse to their final destination. According to stats, more than 80% of the businesses use warehouse management systems (WMS) to manage their shipments.
For businesses, it is essential to ship the right products at the right time to the right destination for their shipping process to be successful, efficient, and effective. Therefore, businesses need to be vigilant about various factors like shipment picking and packing, courier partners, labels and transportation, and most importantly tracking.
Common challenges like Inventory shortages, higher fulfillment costs, no real-time visibility, human errors, equipment failure, courier partner related issues and other internal issues can cause damage to productivity, profitability, and growth.
How To Improve Shipping Process:
- Warehouse Management System (WMS) can significantly enhance shipping operations by providing real-time data about inventory levels and tracking outgoing shipments.
- With the help of Transportation management system (TMS), the route planning and carrier selection can be significantly optimized, improving efficiency and reducing costs
- Choose the right courier partner to seamlessly manage and meet customer requirements without any delays or damages
- Being strategic about fulfillment network and inventory placement can lead to faster shipping and shorter delivery times
7. Kitting/Dekitting
Kitting/Dekitting is the warehouse process of assembling and disassembling multiple products into a kit or single unit. This process is used in warehouses to streamline order management and fulfillment by combining items that typically belong together.
This involves the gathering of all parts of an order into a single box or unit, while also ensuring that their quantity and quality are correct before they are delivered to customers.
Kitting process helps reduce errors in orders as well as ensures that only complete orders are shipped out. Moreover, by bundling products together, warehouses can save on storage space and lower labor costs. It is important as it ensures accuracy when fulfilling orders and eliminates redundant warehousing processes.
How To Improve Kitting Process:
- Establish a dedicated area in the warehouse solely for kitting activities to minimize disruptions and allow workers to focus on assembling kits accurately and efficiently.
- Implement automated systems for kitting processes including conveyor systems, pick-to-light, or robotics, which can reduce human error
- Consider batch kitting, where multiple identical kits are assembled at the same time to increase efficiency by reducing the amount of time spent retrieving items.
- Continually monitor and analyze the kitting process data to help identify inefficiencies, track performance, and inform decision-making
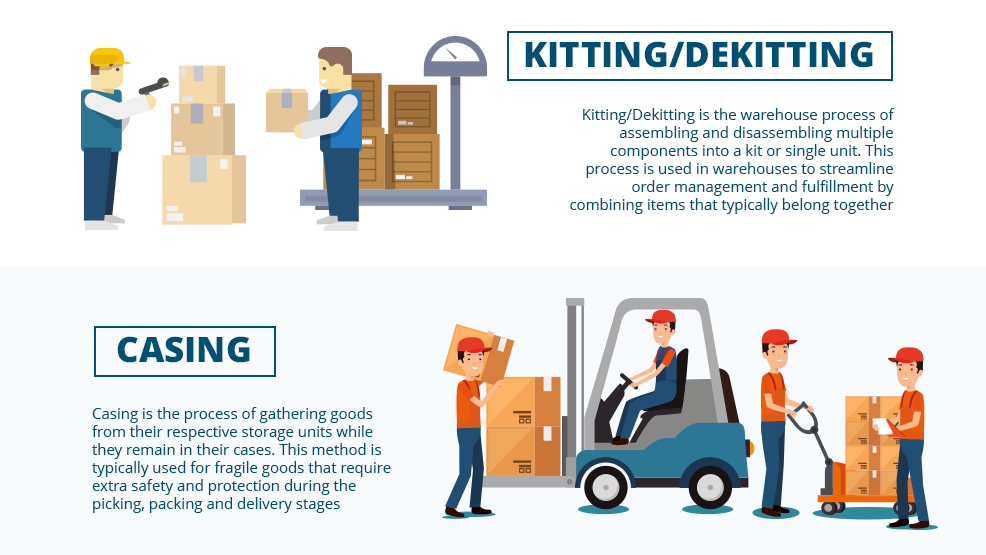
8. Casing
Casing is the process of gathering goods from their respective storage units while they remain in their cases. This method is typically used for fragile goods that require extra safety and protection during the picking, packing and delivery stages.
The traditional method of casing has been done by manual labor; however, modern warehouses have now adopted automated conveyor belts for this purpose.
Businesses or warehouses who are dealing with products that are fragile or are preferably best shipped in casing like glass products, electronic products, etc. should invest in both software and hardware to automate the process.
Casing helps to ensure accuracy when fulfilling orders as it eliminates potential errors that may occur during the manual pick-up stage. By using an automated warehousing picking conveyor belt system, a warehouse can speed up the entire process while also saving on labor costs. Moreover, using such a system will prevent damages to goods due to mishandling or incorrect packaging.
How To Improve Kitting Process:
- Identify the items or goods that will require casing to minimize product damages and losses
- Use a mix of manual and automated handling systems to ensure safer picking, packing, and shipping
9. Inventory Tracking
Inventory Tracking is the warehousing process of recording, managing and storing all items present in a warehouse. It is one of the most important warehouse processes in any logistics system as by tracking inventory, warehouses can prevent errors due to lack of stock and ensure that all items are available for sale.
The traditional method of tracking and managing inventory involved manual counting which was time consuming and had potential for errors. However, with modern technology, this process has become much more efficient by automating the entire process using software solutions.
The softwares like Hopstack help to provide real-time updates on the current status of inventory levels and leveraging inventory based model of ecommerce so that warehouses can quickly identify any discrepancies or shortages.
How To Improve Inventory Tracking Process:
- Regular cycle counting, which involves counting a portion of inventory in a certain area each day, can help ensure the accuracy of inventory records
- A WMS provides real-time visibility into inventory levels, movement, and location within the warehouse.
- Use automated systems to monitor stock levels and automatically reorder products when they fall below a certain threshold to prevent stockouts and excess inventory
- Internet of Things (IoT) devices, like smart shelves or drones, can automate inventory tracking and provide real-time visibility into inventory
- Standardizing inventory management procedures, such as receiving, putaway, and picking, can help ensure accurate tracking
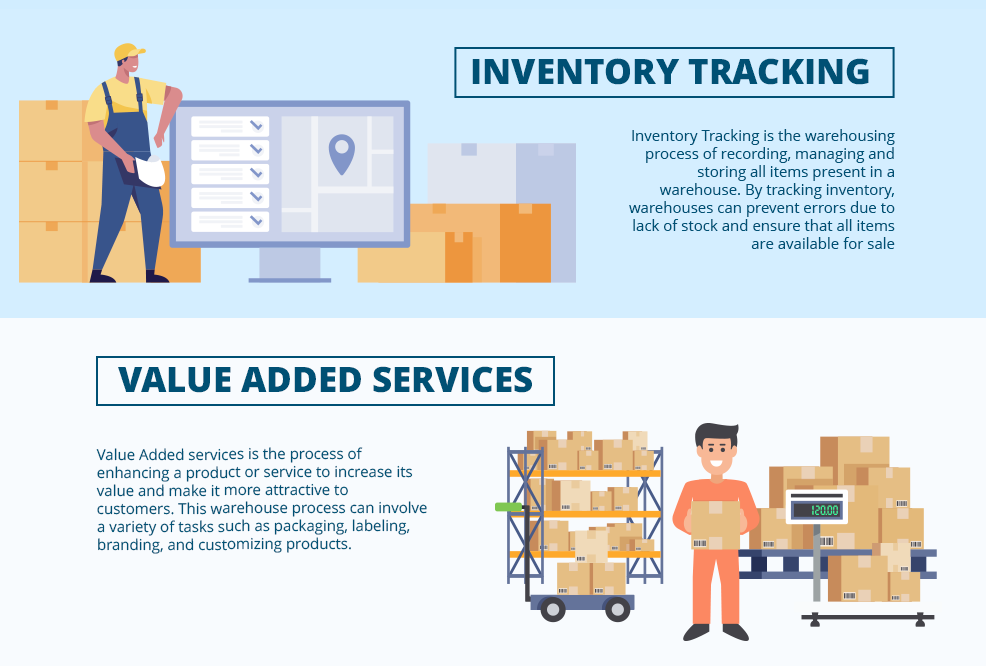
10. Value Added Services
Value Added services is the process of enhancing a product or service to increase its value and make it more attractive to customers. This warehouse process can involve a variety of tasks such as packaging, labeling, branding, and customizing products.
Value added services can give you competitive advantage, gain supply chain excellence, generate increased revenue and enhance customer satisfaction. These warehousing processes start with understanding customer needs and preferences so that warehouses can customize products accordingly.
This involves analyzing the target market and creating an effective strategy for product enhancement. Warehouses must then determine the type of value-adding services they will offer, such as customization, printing, labeling, etc., depending on their resources and capabilities.
11. Returns
Customer returns are one of the key aspects of the warehouse process where the warehouses have to pick up for restocking or disposal of returned items. With the increasing online shopping trend, this process has become even more important.
The returns process starts with customer requests, which must be taken into account and processed quickly and efficiently. Once a product is returned, warehouses must assess its condition to determine whether it can be reused or discarded. If it can be reused, then manual accounting may not be necessary as electronic systems can track its status and availability.
However, manual accounting is important to maintain accurate records if goods are damaged or need to be discarded. By properly managing their returns process, warehouses can ensure that customers remain satisfied while also minimizing losses due to damaged goods.
How To Improve Returns Process:
- Make sure your return policy is clear, concise, and easy for customers to understand to help reduce errors and misunderstandings
- Implement an effective Return Merchandise Authorization (RMA) system that provides a proper mechanism for managing returns and gives clear instructions to customers about the return process
- Using an automated system for returns management can speed up the returns process, reduce errors, and provide faster refunds or exchanges for customers
- Ensure a rigorous quality check process is in place to inspect returned items to identify recurring problems
- Develop a robust system for dealing with returned goods. This might include reselling items, recycling materials, or properly disposing of goods that can't be resold

12. Reporting and Analytics
Reporting and analytics are crucial as businesses can gain better insights and understanding of their warehouse operations and make better decisions based on data collection and analysis for operations.
Warehouse reporting and analytics powered by platforms like Hopstack provide detailed performance visibility into all key warehouse operations. Through granular reporting, real-time warehouse metrics, multi-level reports, and comprehensive audit trails, warehouse managers can develop deeper understanding of each and every warehouse process.
With the granular visibility into each and every process in the warehouse, you can manage productivity levels, forecast demands, review supplier performances, eliminate choke points, optimize warehouse layout, and enhance resource utilization.
How To Improve Returns Process:
- To make sense of large amounts of data, use data visualization tools that can present data in a clear and understandable manner
- Integrate warehouse management systems to track and analyze performance metrics and trends
- IoT devices can gather data continuously from various points in the warehouse, which can be used for predictive analytics, optimization, and proactive problem-solving
- Predictive analytics can help forecast future demand, optimize stock levels, and improve resource allocation
- Implement real-time monitoring systems to track key performance indicators (KPIs)
Remember that not every strategy will work for every warehouse, as they may depend on factors such as the size of the warehouse, the number of employees, the type of goods stored, and the specific needs of your business. It's important to regularly assess your warehouse management operations and adapt your strategies as needed.
Tips and Strategies to Improve Warehouse Processes
Enhancing warehouse efficiency doesn't always require large-scale automation—often, small, strategic changes can create significant impact. Below are proven strategies to streamline operations, reduce costs, and boost overall performance:
1. Standardize Processes and Workflows
Document and standardize key warehouse procedures (e.g., receiving, picking, dispatch) to ensure consistency, reduce training time, and minimize errors across shifts and teams.
2. Adopt a Scalable Warehouse Management System (WMS)
Even a lightweight WMS can automate routine tasks, track inventory in real time, generate accurate reports, and integrate with your ERP or e-commerce systems.
3. Use Slotting Optimization Techniques
Regularly analyze product velocity and reassign high-demand items to accessible zones. Smart slotting reduces picker travel time and increases throughput.
4. Implement Lean Warehousing Principles
Eliminate non-value-adding steps by streamlining layout, reducing touchpoints, and minimizing excess movement or overstocking—creating a more agile and cost-effective operation.
5. Cross-Train Warehouse Staff
Training employees across multiple functions (e.g., picking, packing, QC) enhances flexibility, reduces downtime during demand spikes, and improves resource allocation
6. Leverage Real-Time Data and KPIs
Track and act on metrics like order accuracy, pick rate, and space utilization. Use dashboards and alerts to spot inefficiencies and make proactive decisions.
7. Invest in Scalable Automation
Start small with conveyor belts, pick-to-light systems, or barcode scanning. Gradually expand automation based on ROI and operational maturity, avoiding over-investment.
8. Use Digital Twins for Simulation and Optimization
Advanced warehouses use digital twins (virtual replicas) to simulate process changes, layout shifts, or volume surges—helping identify bottlenecks before they happen.
9. Implement Cycle Counting Instead of Annual Stock Takes
Shift from disruptive, once-a-year inventory checks to rolling cycle counts. This improves inventory accuracy and helps detect shrinkage or misplacement early without halting operations.
10. Integrate Predictive Maintenance for Material Handling Equipment
Use IoT sensors or equipment monitoring software to predict breakdowns in conveyors, forklifts, or packaging machines—minimizing downtime and unplanned disruptions.
11. Establish Exception Handling Protocols with Automation Hooks
Build workflows for handling exceptions—like damaged goods, stockouts, or mispicks—and automate escalation, alerts, or re-routing with your WMS or ERP
12. Run ABC Analysis for Prioritized Operations
Classify inventory using the ABC method (A = high-value, fast-moving, C = slow-moving) and allocate resources accordingly—like priority lanes, faster pick zones, or climate control where needed.
Key Warehouse Processes [Infographic]
.png)
Feel free to share or publish this infographic on your social channels, blogs, and other digital mediums. However, do add the infographic source as hopstack.io/blog/warehouse-processes
FAQs
What are the main processes in a warehouse?
The main warehouse processes include receiving, putaway, inventory management, picking, packing, dispatching, quality control, and returns handling. Each step ensures goods move efficiently through the supply chain
How does technology help optimize warehouse processes?
Technologies like WMS, RFID, automated conveyors, robotics, and AI-based quality checks help streamline operations, reduce errors, and improve speed across warehouse functions.
What is warehouse process flow and why is it important?
Warehouse process flow refers to the sequence of operations from receiving to dispatch. A smooth flow minimizes delays, reduces handling costs, and improves overall efficiency.
How can small warehouses improve their processes without full automation?
Small warehouses can optimize workflows using barcode systems, digital checklists, lean layouts, and basic WMS solutions—without needing full-scale automation.
Can warehouse processes be optimized without investing in robotics?
Yes, many improvements can be made through process standardization, better staff training, lean inventory practices, and software-based tools like WMS or mobile picking apps
How often should warehouse processes be reviewed or updated?
Warehouse processes should be reviewed at least annually, or whenever there’s a major change in product volume, order profiles, customer expectations, or technology stack
How do warehouse processes differ between B2B and B2C fulfillment?
B2B warehousing often handles bulk orders with scheduled dispatches, while B2C requires faster, smaller, and more frequent order fulfillment—requiring different process flows and tech setups.