In the fast-paced world of eCommerce, warehouse receiving plays a critical role in setting the tone for a smooth and efficient fulfillment process. As the first step in the supply chain, it involves the careful handling of everything from delivery and unloading to organizing and storing inventory.
When done right, it ensures that your products are ready to flow seamlessly through the rest of your operation—from picking and packing to shipping. However, even small errors during receiving can lead to significant disruptions down the line.
That's why it's essential to optimize this process for accuracy and efficiency, helping you avoid costly mistakes and ensuring customer satisfaction. In this guide, we'll dive into the key steps of warehouse receiving, show you how to optimize it, and share best practices that can transform your operations from the ground up.
What is Warehouse Receiving?
Warehouse receiving is the first and most crucial step in the supply chain process where incoming goods are delivered, unloaded, inspected, and stored in a warehouse or fulfillment center. It involves verifying that the quantity and condition of received items match the purchase orders and are free of damage or defects. This step ensures that the right inventory is accounted for and properly organized, setting the stage for the rest of the warehouse operations, such as picking, packing, and shipping.
In a well-organized receiving process, everything starts with receiving documentation, where records of incoming shipments are compared to purchase orders to confirm accuracy. Once verified, the goods are unloaded and often inspected to check for discrepancies, damages, or missing items. After this, items are sorted and moved to designated storage locations or shelves, ready for future fulfillment.
A well-executed warehouse receiving process not only minimizes errors but also enhances the efficiency of inventory management and order fulfillment. This step is critical to preventing stock discrepancies, ensuring inventory accuracy, and avoiding delays that can negatively affect customer satisfaction.
Typical Warehouse Receiving Process Flow
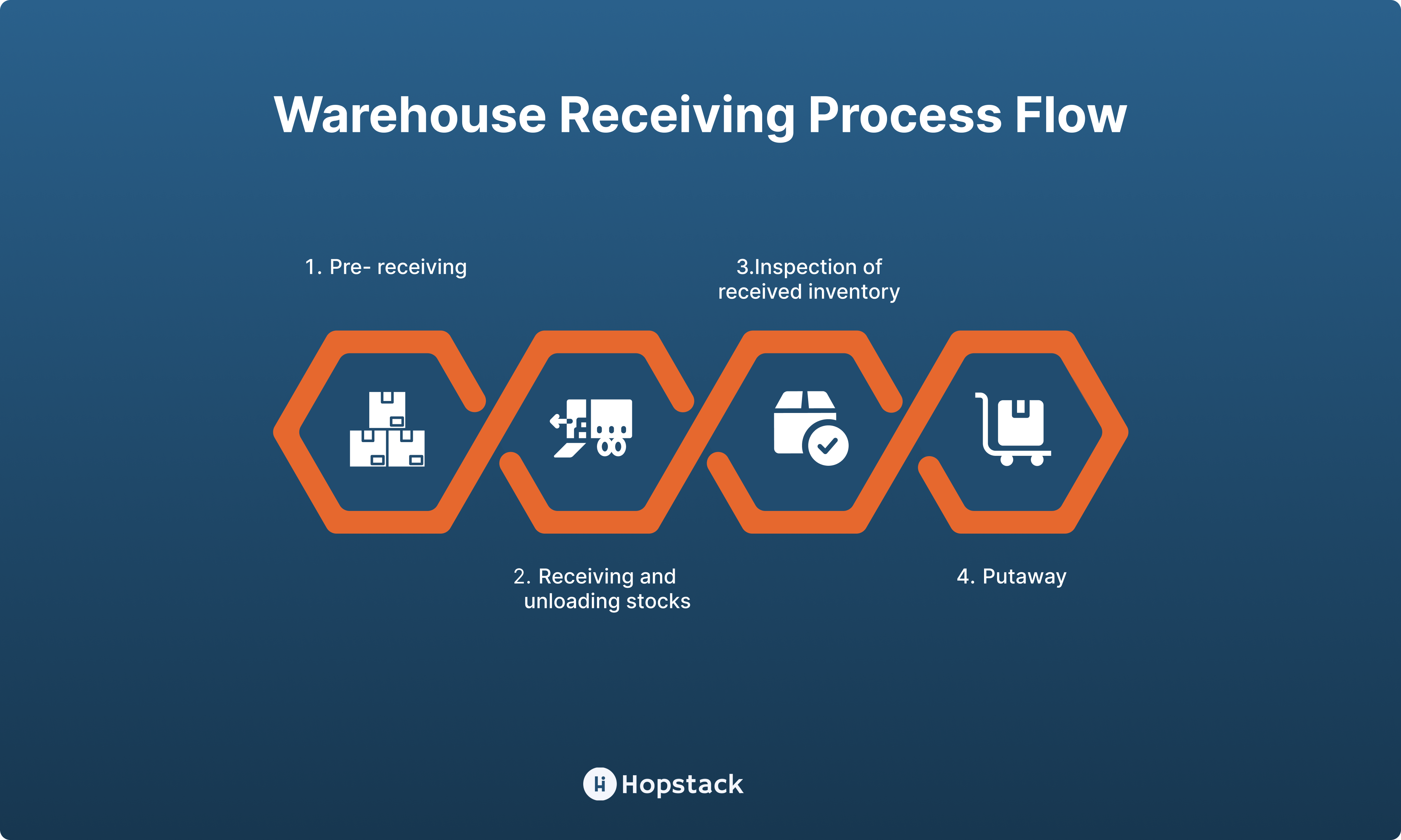
1. Pre-Receiving
Before receiving a shipment, business owners must complete pre-receiving tasks to ensure smooth movement and timely delivery of stocks to the warehouse. In most cases, a Warehouse Receiving Order (WRO) label is created containing essential package details.
These details are encoded in barcodes attached to every shipment, making it easier to scan and verify the received products through the receiving module of the Warehouse software.
2. Receiving and Unloading Stocks
Once the inbound shipment reaches the warehouse, the receiving staff unloads the cargo. Having full details of the inventory beforehand helps optimize the warehouse receiving process. Depending on the size and volume of the incoming consignment, warehouse operators can allocate employees and heavy machinery like pallet jacks and forklifts efficiently.
Digital Warehouse software leverages data and advanced analytics to recommend the optimal allocation of workers and equipment needed for shortening the dock-to-stock cycle.
3. Inspection of received inventory
Damaged products, broken seals, lost items, a mismatch in product SKU, or other details are verified at the time of unloading. The products received should match the contents listed on the WRO, and any discrepancy or damaged product should be kept aside to be discussed with the manufacturer.
This is essential for preventing any faulty item from reaching the customer. It is also important to capture the details during the inspection process in the QA module of the warehouse software to identify patterns and prevent and minimize future errors.
Read Also: Digital Transformation of the Warehouse
4. Putaway
Once all the cargo is inspected and unloaded, the person in charge of receiving acknowledges the same. Inventory numbers are assigned to the products, after which they are segregated per size, category, expiry date, and other parameters.
They are then sent for storage in the warehouse. Details of the inventory received, damaged products, and where it is stored are updated in the system.
In warehouses that still need to be digitized, the putaway warehouse process tends to be inefficient since the warehouse associates spend time locating the storage shelves through a suboptimal path.
Such inefficiencies can be addressed through putaway optimization algorithms inbuilt into warehouse operating software. These algorithms can optimize the putaway route, sequence and handle FEFO compliance.
-bkc16.jpeg)
Common Flaws & Mistakes in Warehouse Receiving Process
A typical warehouse deals with several problems daily. Some of these include:
- Long waiting times for the inbound trucks to unload as docks are backed up.
- Forklift operators loading pallets prematurely, creating gaps in the inventory.
- Disorganized storage leading to suboptimal space utilization.
- Inefficient staffing of associates due to lack of system-driven work.
- Lack of awareness of the work processes amongst the workforce.
- Inaccurate inventory tracking, resulting in misplaced and lost inventory.
These issues cause the warehouse to spend more time and resources and slow the order fulfillment cycle, leading to decreased customer satisfaction.
Enforcing changes in the warehouse receiving process to make it streamlined and efficient can resolve most of these issues. Let us see how the receiving processes can be further improved using smart warehouse systems.
How To Improve Warehouse Receiving Process?
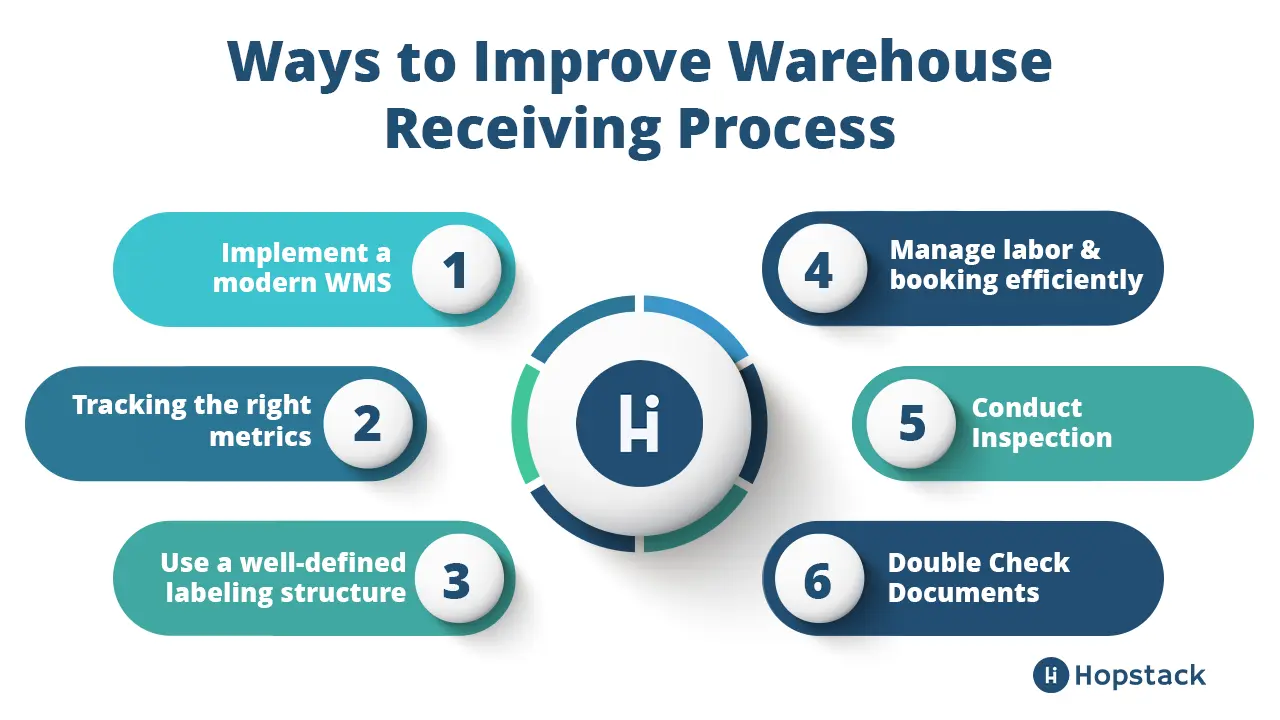
Improving the efficiency of the receiving warehouse process in a warehouse reduces the raw material to finished goods conversion cycles for manufacturing businesses. It can enhance the order lead times for retail and e-commerce businesses.
Here are some of the ways to improve the receiving process in warehouse and make it error-free:
1. Implement a modern warehouse management system
Many warehouse processes are involved in the goods receipt process that can be time-consuming and tedious to perform. Manually tracking and documenting tasks such as inventory movement, labor & equipment availability, and product details make them error-prone.
Modern warehouse software and hardware solutions can help businesses automate and optimize these mundane tasks and reduce unnecessary errors. Implementing a robust warehouse system can help plan the inbound inventory movement more efficiently to avoid overflow and excess inventory. On the other hand, it can also predict potential stockout situations and trigger replenishment orders.
2. Tracking the right metrics
Gathering data at every step of the receiving warehouse process is not good enough. The data should be analyzed to identify trends and patterns for the root causes.
Warehouse systems with inbuilt analytics and reporting capability can help in tracking metrics such as:
- Dock to stock cycle time
- Inventory stored at every location
- Putaway items per hour
- Average storage cost per unit
- Truck turnaround times at the dock
The metrics are critical for designing and implementing effective systems that reduce cycle time and errors.
3. Use a well-defined labeling structure.
A well-defined labeling structure incorporating modern technologies like barcoding, RFID tags, and automated pallet management systems makes it easier for warehouse operators to instantly update stock information in the system as soon as they unload.
Having detailed information about your inventory gives you more control and insights into the supplier's performance regarding lead times, reliability, and quality.
4. Manage labor & booking efficiently
Labor expenses amount to 50 to 70 percent of the warehousing operating budget, making it the most significant cost line item.
Efficient system-driven workforce management prevents under or over-allocation of resources and helps balance workload.
Warehouse software can automate effective workforce management, thereby keeping up warehouse productivity levels and avoiding injuries and safety incidents.
5. Conduct Inspection
Regular inventory audits, including physical counts and cutoff analyses, can assist in spotting inventory imbalances before they become a problem. It will help to plan the future warehouse receiving.
Hopstack's integrated inventory management solution assists with inventory audits and provides real-time updates on stock levels, damaged goods, and specific SKUs that simplify tracking inventory more effectively.
6. Double Check Documents
Double-checking the inventory received and the document for purchasing orders will help to receive the correct products. It is also simpler for staff to thoroughly review paperwork and spot missing stock by implementing a system for all receiving and shipping documents that assign numbers to each document type and labels various forms in a sequential sequence.
Benefits of an Optimized Warehouse Receiving Process
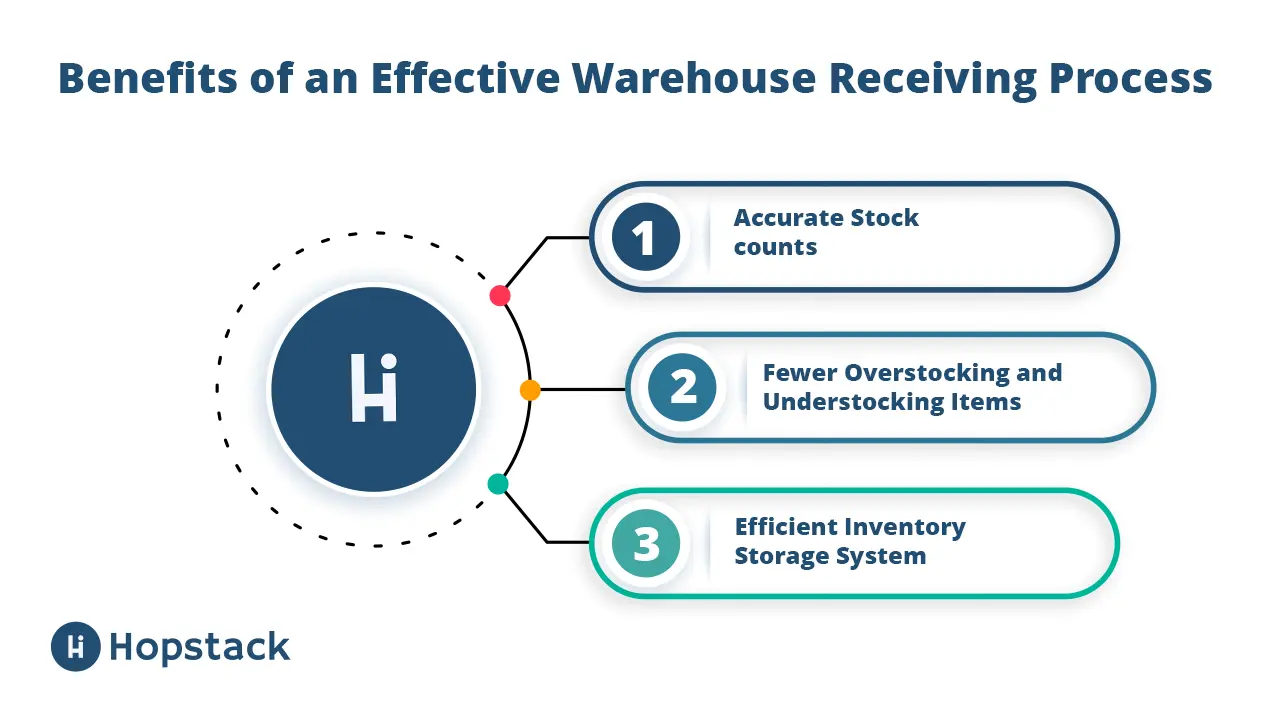
An optimized receiving warehouse process aims to guarantee that the suppliers deliver the specified goods in the appropriate quantities, in good condition, and on time.
The inconsistency of the inventory data caused by inaccurate receiving processes makes it challenging to fulfill customer orders. Effective optimization of the warehouse receiving warehouse process provides businesses with multiple benefits discussed below.
1. Accurate Stock counts
Having accurate stock counts help in preventing issues like inventory stockouts and shrinkages. Inaccurate stock counts lead to customer disappointment as they cannot buy their preferred products. Hence, brands can provide superior customer experience by ensuring accurate stock counts as a byproduct of an effective receiving process.
It also helps companies to manage sales forecasts. For instance, a comprehensive receiving process allows companies to check whether they have received the items in the correct order and inventory level. Additionally, the brand can replenish an item on demand or notify the customers regarding product availability when it is out of stock.
2. Fewer Overstocking and Understocking Items
A brand experiences stockout when there is insufficient inventory to fulfill customer demand. On the other hand, the company sometimes needs a more accurate inventory count to stock products.
Sometimes retailers need the idea of the dead stock items that eat up the warehouse space. An effective warehouse receiving process helps brands determine which items to order more and ways to remove the dead stocks.
3. Efficient Inventory Storage System
An efficient receiving process can also affect managing and tracking inventory. It will help lower inventory management costs by reducing shipment costs and improving transit times.
Brands using a WMS can track their warehouse operations and inventory efficiently. WMS is used for scanning the list when received. It also marks and records the areas where the products are stored. WMS also provides warehouse order picking, packing, and shipping instructions to associates that induce error-free fulfillment.
What is a Warehouse Receiving Process Checklist?
A Warehouse Receiving Process Checklist is a structured list of tasks, checks, and verifications designed to guide warehouse personnel during the receiving process.
It serves as a roadmap for ensuring that all incoming shipments are received, inspected, documented, and stored accurately and efficiently. The checklist can encompass various stages, from pre-arrival preparation to post-receiving clean-up and continuous improvement.
The primary objective of this checklist is to maintain orderliness, ensure accuracy, uphold safety standards, and optimize the flow of goods within the warehouse. By providing a clear set of instructions and checks, it minimizes errors and oversights that can lead to inventory discrepancies, wasted resources, or delays.
Warehouse Receiving Process Checklist
1. Pre-Arrival Preparation
1.1. Review and confirm upcoming deliveries with suppliers.
Establishing clear communication channels with suppliers is key. Regularly reviewing and confirming the shipments ensures there are no unexpected surprises. This proactive approach allows the warehouse to allocate the necessary resources, ensuring efficient handling of goods upon arrival.
1.2. Update and maintain an organized schedule for incoming shipments.
With multiple shipments potentially arriving, a well-organized schedule is paramount. Leveraging modern scheduling tools can help in prioritizing shipments, balancing workload, and ensuring timely processing.
1.3. Ensure that receiving docks and areas are clear and ready.
Keeping the receiving area clear ensures there's ample space to move and inspect goods. A prepared area also reduces the risk of accidents, promoting a safe working environment and ensuring the integrity of the received goods.
1.4. Equip staff with required PPE (Personal Protective Equipment) and tools.
The well-being of the warehouse staff is crucial. Equipping them with the right safety gear, from helmets to safety shoes, ensures they're protected against potential hazards. Additionally, providing them with tools like barcode scanners, forklifts, or pallet jacks, can significantly expedite the receiving process.
1.5. Familiarize staff with special handling instructions.
Not all goods are the same. Some might be fragile; others might be hazardous. Briefing the staff on any special handling instructions for specific shipments ensures that goods are treated appropriately, reducing the risk of damage or accidents.
2. Shipment Arrival
2.1. Verify the identity of the delivery truck and driver.
Security and authentication are paramount in today's complex supply chains. Verifying the identity of the truck and driver ensures that the shipment is legitimate and reduces the risk of delivery complications.
2.2. Ensure safe parking of the delivery vehicle.
Proper vehicle positioning isn't just about efficiency; it's about safety. Guiding the vehicle to a designated parking spot ensures smooth offloading, reduces congestion, and minimizes potential hazards, especially in warehouses with continuous inflow and outflow of goods.
2.3. Review delivery documentation for accuracy.
The importance of accurate documentation can't be overstated. This initial check sets the tone for the entire receiving process. Validating the delivery notes, invoices, and other related documents against expected shipments can highlight discrepancies early on, allowing for timely resolution and ensuring inventory accuracy.
3. Unloading Goods
3.1. Start unloading process with care.
Each item in a shipment represents value to the business, to the supplier, and to the end customer. Ensuring a careful unloading process not only maintains the quality of the goods but also signifies a respect for that value.
3.2. Segregate items based on category.
Efficient categorization right from the start can streamline subsequent processes. Whether it's perishables, electronics, or textiles, segregating items based on their category ensures that they're processed, verified, and stored under optimal conditions.
3.3. Inspect for damages or discrepancies.
Prompt identification of damaged goods means faster resolutions, be it returns, replacements, or insurance claims. It also provides feedback on the shipment process – if damages are frequent, it might be time to review the shipping and handling processes with suppliers.
3.4. Tally items against the purchase order.
Tallying ensures that the warehouse receives exactly what was ordered, neither more nor less. It helps in maintaining precise inventory levels, and any discrepancies can be addressed immediately, ensuring a smooth flow in subsequent operations.
4. Goods Verification
4.1. Cross-check items with the purchase order.
It's vital to compare received items against the original order to maintain consistency and trust in the supply chain. This meticulous check safeguards against potential errors, whether they stem from the supplier's end or occur during transit.
4.2. Verify individual item details.
Beyond the broader verification, diving into the nitty-gritty details of each item – from SKU to manufacturing details – is essential. This granular level of verification ensures product authenticity, guarantees quality, and assures customers that what they receive is precisely what they ordered.
4.3. Report discrepancies promptly.
By immediately flagging and reporting discrepancies, warehouses can ensure faster resolutions, minimizing potential disruptions in operations. Immediate reporting also builds transparency with suppliers, fostering a collaborative approach to problem-solving.
5. Documentation & Data Entry
5.1. Update the Warehouse Management System (WMS).
A real-time, accurate update to the WMS is more than just an administrative task. It ensures that the entire supply chain operates cohesively. Accurate inventory data allows for better forecasting, optimizing procurement processes, and ensuring that the warehouse is neither overstocked nor understocked.
5.2. Systematically archive physical paperwork.
While digital systems are becoming the norm, physical documentation still holds significant importance. Storing these systematically ensures easy access during audits, stakeholder reviews, or when resolving disputes. Organized paperwork also ensures that any statutory or regulatory compliance is easily verifiable.
5.3. Document any anomalies.
Keeping a meticulous record of any irregularities, be it damage or deviations in delivery, forms the foundation for future actions. Whether it's a claim process with insurers, addressing supplier quality issues, or revising internal processes, such records are invaluable.
6. Goods Storage
6.1. Transfer items to their designated storage areas.
It's about ensuring that goods remain in optimal condition, are easy to retrieve, and are stored in a manner that complements the flow of operations. This approach reduces retrieval times, ensures FIFO (First-In-First-Out) practices where needed, and minimizes the risk of product obsolescence or spoilage.
6.2. Ensure appropriate storage conditions.
Ensuring that each item's specific conditions – be it temperature, humidity, or light sensitivity – are met is essential for maintaining product quality and integrity. Proper storage reduces wastage, guarantees product efficacy, and upholds the warehouse's reputation for quality and reliability.
6.3. Label storage zones for clarity.
Clear, visible labels facilitate quicker identification of products. This is particularly beneficial during peak operational hours or when handling high volumes of goods. With well-labeled zones, staff can swiftly locate items, reducing lead times for order processing and increasing overall warehouse efficiency.
7. Post-Receiving Clean-Up
7.1. Maintain a neat receiving area.
A consistently clean receiving area not only improves safety by reducing trip hazards but also fosters a disciplined working environment. Regular cleanliness practices can lead to better warehouse hygiene, reducing the risks of contamination or pest infestations, especially vital for warehouses storing perishables.
7.2. Store tools in their designated spots.
Proper storage of tools and equipment not only extends their lifespan but also ensures they're readily available when needed. Time saved searching for tools can be better utilized in processing incoming shipments. Moreover, well-maintained tools reduce operational hiccups, leading to smoother warehouse functions.
7.3. Evaluate the day's receiving operations.
By evaluating the efficiency, speed, and accuracy of the receiving process daily, managers can identify bottlenecks, address staff concerns, and implement strategies for further optimization. Regular reviews also empower staff to voice their observations and suggestions, fostering a culture of collective growth.
.png)
Why is it Important to Have a Receiving Checklist?
1. Streamlining Operations
A checklist standardizes the receiving process, ensuring consistency and efficiency regardless of the team member handling the task.
2. Enhancing Accuracy
By following a structured list, warehouse staff can ensure they don't miss out on any critical steps, reducing the chances of errors or inventory mismatches.
3. Safety Measures
The checklist can incorporate safety protocols, ensuring that goods are handled safely and potential hazards are minimized.
4. Improved Accountability
A well-defined checklist makes it easier to track tasks, identify any lapses, and hold the responsible parties accountable.
5. Effective Communication
A standardized checklist facilitates better communication among warehouse teams, as everyone is aligned with the expected processes and protocols.
6. Reduced Training Time
New team members can be onboarded more quickly as they have a clear guideline to follow, which speeds up their training process.
7. Cost Savings
By minimizing errors, optimizing storage, and reducing damage or loss of goods, a receiving checklist can lead to significant cost savings.
8. Continuous Improvement
A checklist serves as a foundation that can be periodically reviewed and enhanced based on feedback, ensuring the warehouse operations continue to evolve and improve.
In essence, a Warehouse Receiving Process Checklist is not just a list—it's a strategic tool that boosts operational efficiency, reduces errors, and ensures smooth warehouse operations. It's an essential component for any warehouse striving for excellence in its operations.
To conclude
Receiving is one of the most critical processes in the warehouse goods movement process. Hence, efficient and error-free receiving is essential for smoothly functioning of an otherwise complicated order fulfillment process.
It is more critical than ever to automate and digitize the receiving process to sync with the changing business dynamics. This will translate into faster business growth and more revenue.
Interested in learning more about how to automate and digitize the receiving process?
Explore Hopstack's Digital Warehouse Software that leverages advanced machine learning algorithms to optimize the goods-receiving process.
FAQs on Warehouse Receiving
What does received by warehouse mean?
"Received by warehouse" refers to the confirmation that goods or shipments have been delivered to and accepted by the warehouse. This includes verifying the quantity, condition, and accuracy of the items against purchase orders or delivery documents.
What is the receiving area of a warehouse?
The receiving area of a warehouse is the designated space where incoming shipments are unloaded, inspected, and verified before being sorted and stored in the warehouse. This area is critical for ensuring the accuracy and condition of goods before they enter the inventory.
What is warehouse receiving cycle time?
Warehouse receiving cycle time is the total time it takes to process incoming shipments from the moment they arrive at the warehouse to the point they are inspected, verified, and stored. This metric helps evaluate the efficiency of the receiving process.
How to receive goods in a warehouse?
To receive goods in a warehouse, follow these steps:
1. Verify the shipment against purchase orders and delivery documents.
2. Unload and inspect items for damage or discrepancies.
3. Record the received items in the inventory management system.
4. Label, sort, and store the items in their designated locations.