Warehousing operations have come a long way. There was a time when each activity in a warehouse was done manually, with pen and paper, and the ability of each warehouse employee to plan and manage tasks greatly influenced the outcomes.
This was certainly inefficient. Order fulfillment took weeks at times and fulfillment errors were commonplace. This led to the rise of the warehouse management system (WMS), often integrated into an ERP (enterprise resource planning) system. WMS was key in the first wave of warehouse digitization. This provided warehouses a better alternative over traditional spreadsheets and emails that didn’t particularly provide a uniform structure to warehousing activities. Some of the early players, as seen in the early 90s included SAP, Manhattan Associates, RedPrairie, and the likes. The spread of WMS’ helped companies standardize their processes, reduce errors significantly, and improve their warehouse productivity and throughput. Companies could now save costs and provide a better and improved customer experience.
The next big challenge to be solved was that of automation. Warehouses started deploying various kinds of devices and robots, right from simpler machines like automated printers to conveyor belts and complex sorters. This led to the need for a common control tower that could help send instructions and retrieve data from every device. Thus, warehouse control systems (WCS) came into the limelight. These systems would act as a one-point solution to all warehouse operations and would also connect with ERPs and WMS’.
The 2010s was the decade of eCommerce. Online shopping not only became the norm but also caused consumer expectations to become tremendously high. Many warehouses weren’t equipped to handle the surge in orders and fulfill them promptly. Warehouses and fulfillment centers now needed sophisticated warehouse management software that would learn from previous operations, create rules and priorities, provide algorithmic recommendations, and optimize every activity. This caused warehouse execution systems (WES) to gain popularity. A WES learns from a management system about how a warehouse is structured and helps optimize each activity carried out by the control system. It sits between a WMS and WCS.
Here is an explanation of the three types of warehouse software systems, WMS, WCS, and WES, their differences, and how the future calls for a unified platform.
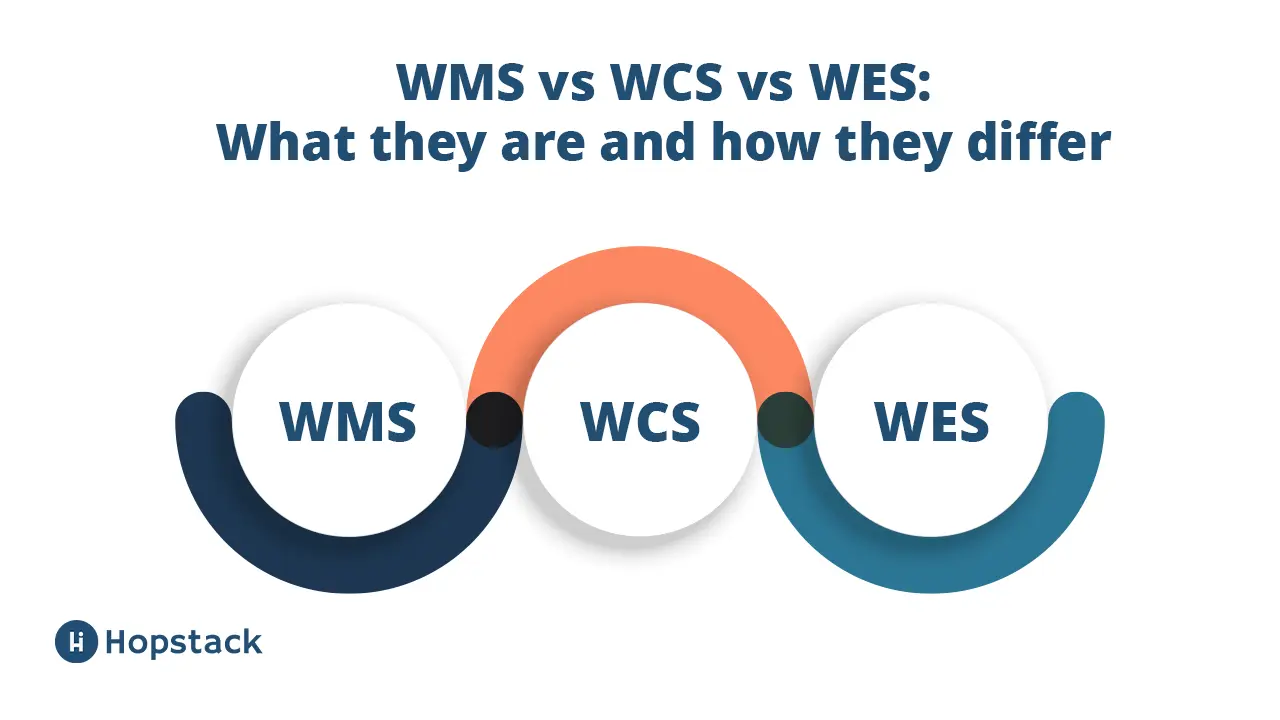
What is a Warehouse Management System (WMS)?
A WMS or warehouse management system is the system level that operates at the most macro scale. Traditionally, a WMS was mainly concerned with inventory flow and storage. It helped warehouses manage the receiving process, putaway, location/SKU-bin tracking, and shipping management. It helped warehouse associates understand where the inventory was stored, when to replenish it, and more.
Additionally, WMS’ evolved into more sophisticated systems that could also assist in transportation and shipping management, advanced reporting, inventory allocation logic, and labor management. This lets WMS’ give users a lot more visibility into operations and the overall fulfillment lifecycle.
Comparing the three systems, a WMS is the most comprehensive and mature software since it can manage inventory flow, labor tasks, and even multi-channel orders. Inventory control is the key feature of any WMS that is absent in both WCS and WES.
Benefits of WMS
Enhanced inventory management: The WMS delivers precise and real-time visibility into inventory levels, locations, and movements, resulting in minimized stock-outs, elevated order accuracy, and improved control over inventory.
Efficient order processing: The WMS automates and streamlines the order fulfillment processes, leading to reduced cycle times, heightened order accuracy, and an overall improvement in customer satisfaction.
Optimized labor management and resource utilization: The WMS aids in labor planning, task allocation, and productivity tracking, optimizing the allocation of labor resources and enhancing workforce efficiency.
Data analysis and reporting: The WMS provides analytical capabilities and reporting tools, empowering data-driven insights into warehouse operations. This facilitates continuous process improvements and supports strategic decision-making.
What is a Warehouse Control System (WCS)?
While a WMS manages the larger overarching activities like inventory management, labor management, and the receiving process, a warehouse control system (WCS) takes charge of individual activities and processes. A WCS carries out plans and activity sequences created by a WMS by integrating with automated hardware such as pallet conveyors, pick-to-light systems, printers, AMRs, etc.
A WCS’ key focus is on error-free communication, speed, and execution. A WCS software is well-suited for highly automated and digitized warehouses and fulfillment centers that involve different machinery and moving parts. WCS’ functionality is limited in comparison to a WMS, however, some of the new-age systems have started adopting WMS features as well.
Benefits of WCS
Effective equipment control: WCS oversees and regulates automated material handling equipment, ensuring optimized routing, minimized downtime, and heightened system reliability.
Visibility and real-time monitoring: WCS offers real-time monitoring of equipment and systems, enabling prompt identification and resolution of issues, ultimately leading to improved efficiency and reduced bottlenecks.
Seamless integration: WCS seamlessly integrates with higher-level systems like WES and WMS, facilitating the smooth flow of information and optimizing the movement of goods within the warehouse.
Scalable and adaptable: WCS has the capacity to adapt to evolving warehouse requirements and effortlessly incorporate new automation technologies, fostering scalability and flexibility.
What is a Warehouse Execution System (WES)?
A WES or warehouse execution system acts as a bridge between a WMS and a WCS. A WES’ main goal is to increase the efficiency of all activities carried out by the WCS and on the basis of the broad structure created by the WMS. Some of the most important WES features include workload planning and distribution, analytics and reporting, dynamic task allocation and order release, business intelligence, picking and packing optimization, and more.
WES’ role is becoming more crucial with each passing year as supply chain complexity grows and customers continue to become habitual of faster and more accurate order deliveries. Warehouses are being forced to improve their throughput as well as optimize for higher fulfillment accuracy. Thus having a stellar WES becomes a necessity in the current age.
Benefits of WES
Increased operational efficiency: WES streamlines workflows and orchestrates real-time material handling tasks, resulting in heightened productivity, shortened cycle times, and enhanced resource utilization.
Flexible and scalable: WES possesses the adaptability to meet changing warehouse requirements, accommodating expansion and supporting diverse material handling technologies, including automation.
Better decision-making: By offering insight into warehouse operations, WES facilitates data-driven decision-making, empowering managers to respond to evolving demands and allocate resources swiftly and with precision.
Seamless integration: WES seamlessly integrates with various systems, such as WMS and WCS, forging a unified ecosystem that elevates overall warehouse performance.
Dynamic Business Needs
So far, we have developed a sense of what the three different systems (WMS, WCS, WES) are and the role they play in warehousing and fulfillment operations. The three often work in tandem to provide end-to-end solutions to their customers. However, the business requirements are unique to each business. Not every business needs all three and may get through with only one or a couple of them.
A large enterprise warehouse may need all three - WMS, WCS, and WES. Think of Amazon or Walmart. Such large warehouses and fulfillment centers, where thousands of robots and devices work in harmony with thousands of warehouse associates in high probability, also process tens of thousands of orders on any given day and have complex interwoven operations to fulfill them. They need a WCS to take control of their deployed devices and a WES to algorithmically optimize every step in the fulfillment process for maximizing productivity. The WCS and the WES need to be tightly coupled with the WMS and transfer data in real-time to manage the complexity of such high-volume operations.
On the other hand, a smaller warehouse, say a new entrant in the 3rd Party Logistics (3PL) space may not deploy hardware automation but would still need a WMS to manage day-to-day flow and storage activities and a WES to operate at the maximum efficiency. A strong suite of software automation will enable a fulfillment center to optimally place inventory, optimize warehouse real-estate to every inch, dynamically allocate tasks, FEFO compliance and much more.
High Fragmentation of Warehousing Systems
Traditional warehousing systems (WMS, WCS, and WES) have always worked in silos, which has caused poor real-time data transferability and inefficiencies in operations. Different warehouses have different needs, so they have had to mix and match solutions available in the market. In most cases, a warehouse might need two semi-integrated or unintegrated software systems to power their warehouses. In other cases, to make matters worse, warehouses might go for a multi-vendor approach, which requires connecting existing systems with additional unrelated systems provided by multiple vendors.
Such a warehouse software stack often comes with its own set of disadvantages. Think deployment time. The deployment time, a metric seen as key by IT and warehouse managers is tremendously high in a situation involving multiple unrelated systems provided by multiple vendors. A few of the other shortfalls in such an arrangement are a high rate of errors and system failures, poor integrability of first and third-party applications, and lack of seamlessness in the data flow.
A Unified Approach
The business of warehousing is becoming increasingly complex with each passing minute. Omnichannel commerce, parallel functioning of B2B and B2C segments, one-day e-commerce fulfillment, and data analytics in warehouses are some of the phenomena that businesses are only learning about in real-time. Most of the legacy WMS’ and other systems are failing new-age warehouses by providing a closed ecosystem and having a singular approach to warehousing problems.
High fragmentation of warehouse software systems has always been a major concern for warehouse managers and associates alike. The distribution of operations is prone to both human as well as machine errors. The integration and data flow between the three systems, WMS, WCS, and WES, have always presented roadblocks and a lack of seamlessness. Modern-day warehouse systems need to provide a comprehensive experience where each function works in tandem, there are no errors in the data flow, and each activity right from labor optimization (WMS), to printing labels (WCS) to batching algorithms (WES) synchronize at every step in real-time without any delays.
Hopstack offers a comprehensive Warehouse Operating System that powers warehouses and fulfillment centers with automation and digitization at every step in the process. The platform offers extensive labor and inventory management modules, helps control and communicate with all devices and robots, and provides proprietary algorithms for batching and picking to improve operational efficiency.
Schedule a demo with our product specialist to learn more about the platform and how it can help automate different areas of your warehouse operations.