Think about the last time you ordered something online. You clicked “Buy Now,” and within days—sometimes even hours—it arrived at your doorstep. But have you ever wondered what happens behind the scenes? That’s where warehouses, especially fulfillment centers, come in.
Warehouses are the unsung heroes of trade and commerce. Every order placed online sets off a chain reaction inside these massive storage hubs—products are picked, packed, and shipped with precision.
With the rapid growth of e-commerce and advancements in technology, warehouses have evolved beyond just storage spaces. Today, there are various types, each designed to serve different needs:
- Distribution centers act as temporary storage hubs, ensuring products get to retailers or customers quickly.
- Fulfillment centers are the lifeline of e-commerce, handling everything from order processing to packaging and shipping.
- Micro-fulfillment centers bring products even closer to customers, speeding up delivery times in urban areas.
- Dark stores operate behind the scenes, dedicated entirely to online shopping fulfillment.
But no matter the type, one thing remains constant: efficiency is everything. The way products are stored, organized, and managed inside a warehouse can make or break the entire fulfillment process. In fact, smart warehousing isn’t just an operational necessity—it’s a major competitive advantage.
In this guide, we’ll dive deep into warehouse management, breaking down the strategies, technologies, and best practices that keep products moving smoothly from shelf to shipment. Let’s get started!
What is Warehouse Management?
Warehouse management is the process of efficiently handling the storage, movement, and organization of physical goods within a warehouse to ensure seamless order fulfillment.
It involves key operations like inventory tracking, picking and packing, demand forecasting, storage optimization, and security management—all aimed at improving supply chain efficiency and ensuring smooth day-to-day operations.
Usually the warehouse management is done using a WMS. But what’s a WMS?
A Warehouse Management System (WMS) is the technology that powers these operations, providing real-time visibility, automation, and data-driven insights to streamline inventory management and enhance productivity.
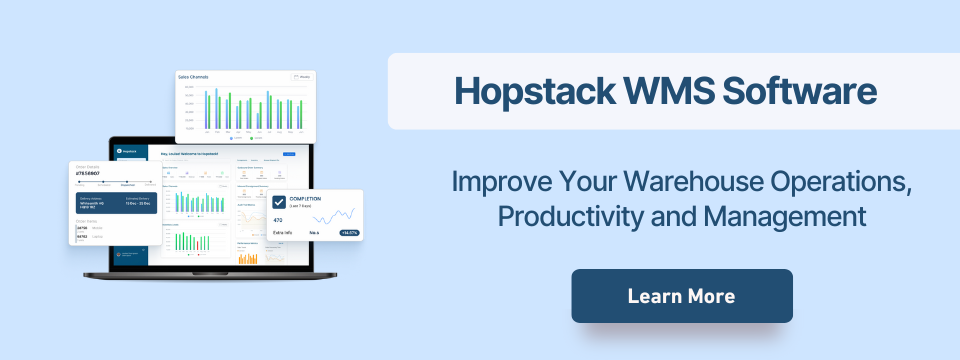
Evolution of Warehousing - 19th Century To 21st Century
Warehouse management has evolved from ancient Egyptian granaries to today’s high-tech fulfillment centers. Early warehouses supported growing trade networks, but the rise of railways and global commerce led to large, decentralized storage hubs near ports and rail stations. The 20th century saw major advancements like forklifts, pallets, and automation, culminating in the first automated storage and retrieval system (AS/RS).
With digitization, improvements in warehouse management systems (WMS) started to support labor-intensive tasks like order management, inventorying, picking and packing, task creation, and more.
Warehouse management tools can integrate with various systems like accounting, enterprise resource planning (ERP) systems, and more to automate communication and carry out warehouse management functions with minimal human intervention.
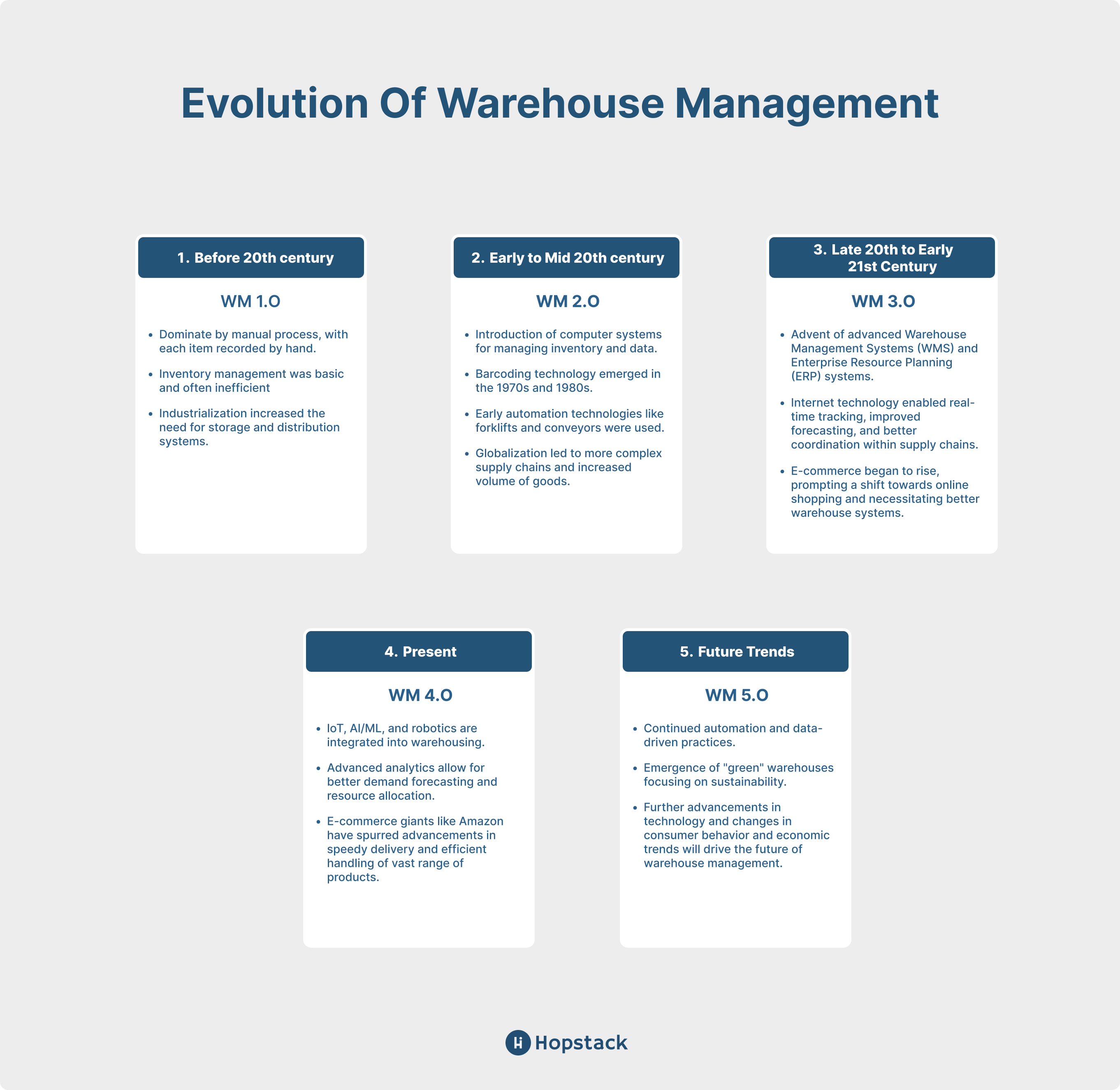
WM 1.0 – Manual Processes
Early warehouse management relied entirely on physical paperwork and human effort. Inventory tracking was slow and error-prone, but manageable due to simpler supply chains and lower trade volumes.
WM 2.0 – Computerization & Automation
With the rise of computers in the 20th century, businesses adopted basic warehouse management systems (WMS). The introduction of barcoding in the 1970s and automation tools like conveyors improved efficiency, driven by industrialization and globalization. This period also saw the first uses of an automated warehouse system, with forklifts and conveyors speeding up operations.
WM 3.0 – Advanced WMS & Connectivity
The late 20th and early 21st centuries saw real-time inventory tracking, improved forecasting, and supply chain visibility through internet-powered WMS. E-commerce growth accelerated these advancements, making warehouses more agile and connected.
WM 4.0 – AI, IoT & Robotics
Today, warehouses are shifting toward AI-driven automation, IoT-based real-time tracking, and robotics for smart inventory management. Predictive analytics optimize demand forecasting, while companies like Amazon showcase seamless tech integrations. Many warehouses still operate under WM 3.0 but are gradually transitioning to WM 4.0.
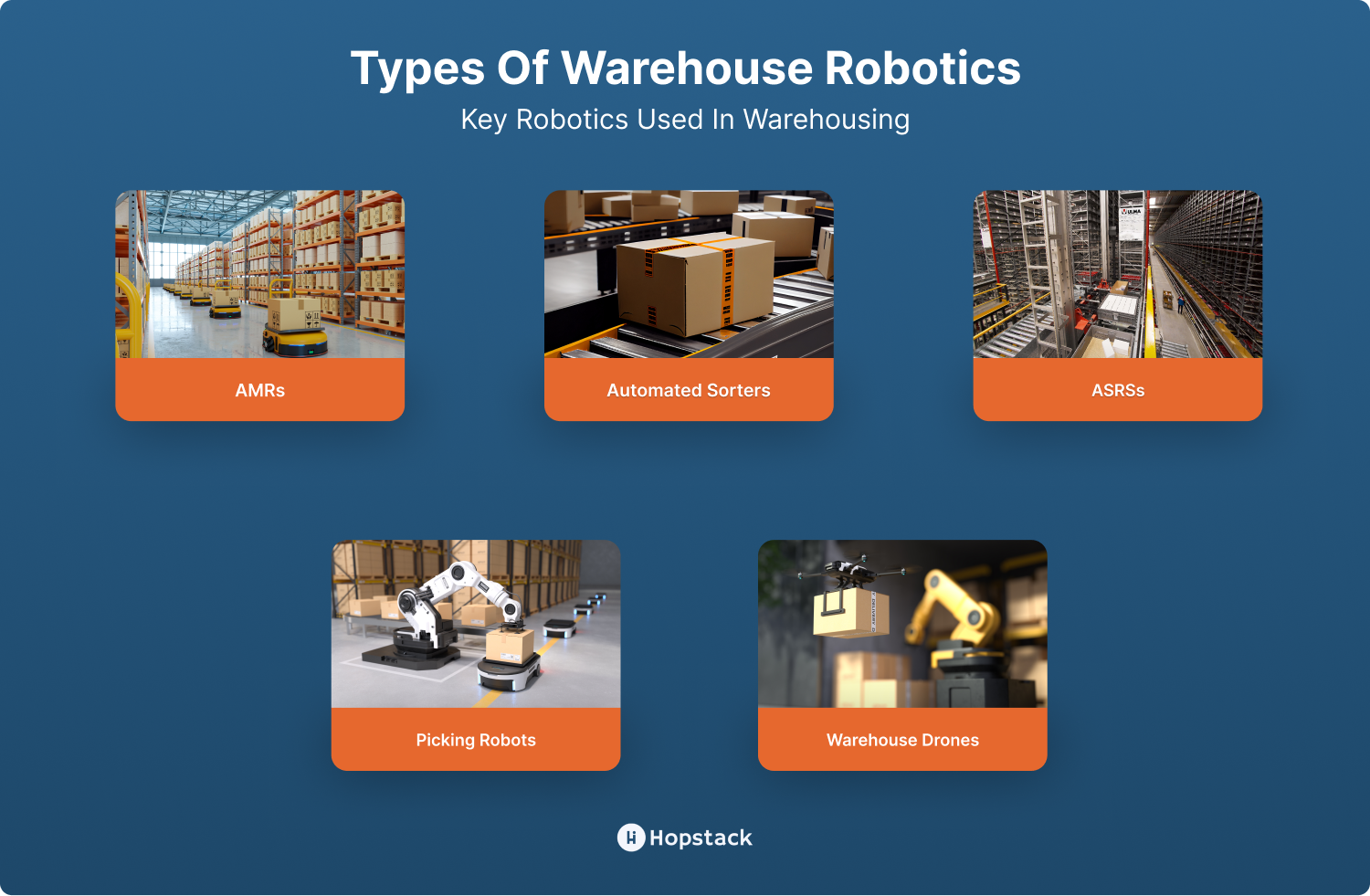
10 Steps Advanced Warehouse Management Process
A warehouse is not just a storage space—it’s a complex system that ensures products move efficiently from suppliers to customers. Here’s a detailed 10-step process that covers the entire warehouse workflow, ensuring speed, accuracy, and efficiency
1. Receiving: The First Checkpoint
Receiving is the foundation of warehouse operations, as any mistake here—like incorrect counts, damages, or missing goods—creates a ripple effect that disrupts inventory accuracy and order fulfillment. This warehouse process involves verifying shipments, checking for damages, tagging items, and updating records in the Warehouse Management System (WMS).A smooth receiving process reduces errors, prevents bottlenecks, and ensures inventory moves efficiently into storage.
- Match received goods with purchase orders for accuracy
- Inspect items for damage or defects before storage
- Label and tag shipments for seamless tracking
- Update inventory records in real-time
2. Quality Control (QC): Ensuring Product Integrity
Quality control ensures only defect-free, compliant products enter the supply chain. Poor QC leads to increased returns, wasted space, and dissatisfied customers. This step involves random checks, defect detection using AI scanners, and logging rejected items. By catching problems early, warehouses prevent inventory shrinkage and improve overall efficiency.
- Conduct random sample inspections to ensure quality
- Use AI-driven scanners for high-volume defect detection
- Set supplier compliance standards to reduce quality issues
- Flag defective items for repackaging, return, or disposal
3. Yard Management: Optimizing Truck & Dock Flow
A warehouse yard can become a bottleneck if trucks are left waiting or dock doors are mismanaged. Efficient yard management optimizes vehicle flow, prevents congestion, and ensures shipments move quickly. Using real-time GPS tracking and dock scheduling tools, warehouses reduce delays, lower fuel costs, and improve overall logistics efficiency.
- Use real-time dock scheduling to reduce truck wait times
- Implement RFID-enabled dock doors for automatic tracking
- Prioritize high-demand goods for faster unloading
- Optimize truck movements using a Yard Management System (YMS).
4. Putaway: Storing Inventory for Maximum Efficiency
A disorganized putaway process leads to misplaced stock and longer retrieval times. Smart putaway strategies use slotting optimization and automated storage systems to place high-demand items in easy-to-access locations. Warehouses can minimize worker movement, reduce picking errors, and optimize space usage by storing fast-moving SKUs upfront and slow-moving items further back.
- Use AI-based slotting tools to adjust storage dynamically
- Store frequently picked items closer to fulfillment zones
- Implement automated conveyors and robotic storage for efficiency
- Label all storage areas for quick retrieval
5. Location Assignment: Organizing for Speed & Accuracy
Strategic location assignment improves warehouse efficiency by minimizing picking time and optimizing space. Items are stored based on turnover rate, perishability, and retrieval patterns. Perishables require climate-controlled areas, while fast-moving items should be placed near picking zones. Dynamic storage strategies ensure warehouses adapt to changing demand.
- Assign fixed or dynamic storage based on demand
- Use heat maps to identify and optimize high-traffic areas
- Store temperature-sensitive goods in controlled environments
- Integrate barcodes and RFID tags for location tracking
6. Inventory Management: Maintaining Stock Accuracy
A warehouse without accurate inventory tracking faces stockouts, overstocking, and fulfillment delays. Real-time inventory monitoring prevents discrepancies and optimizes reordering. Advanced WMS software and RFID trackingprovide live updates on stock levels, ensuring precise forecasting and efficient storage utilization.
- Conduct cycle counting to maintain inventory accuracy
- Use RFID and barcodes for real-time stock tracking
- Implement demand forecasting to optimize stock levels
- Set automated reorder alerts to prevent stockouts
7. Order Picking: Ensuring Fast & Error-Free Retrieval
Order picking is one of the most labor-intensive and time-sensitive processes in a warehouse. Inefficient picking leads to delays and incorrect orders. Zone, batch, or wave picking methods can optimize workflows, reduce unnecessary movement, and improve accuracy. Automated picking systems—like voice-directed or robotic picking—enhance speed and reduce errors.
- Implement batch, wave, or zone picking based on order volume
- Use barcode scanners to confirm order accuracy
- Reduce picker travel time by organizing items strategically
- Leverage automation for high-demand products
8. Packing: Securing Goods for Safe Shipment
Packing determines whether an item arrives at its destination intact. Poor packaging increases returns and damages. Automated packing solutions ensure efficient material usage, while smart packaging minimizes shipping costs. Custom-fit packaging prevents waste and protects fragile goods.
- Use eco-friendly, cost-efficient packaging materials
- Implement automated weighing and dimensioning systems
- Apply smart packaging techniques to reduce damage
- Ensure all packages are correctly labeled for shipping
9. Shipping: Delivering Orders on Time
Shipping is the final step before a product reaches the customer. Efficient sorting, labeling, and carrier selection can lower shipping costs and improve delivery speeds. Warehouses use automated sorting systems and route optimization tools to dispatch goods faster.
- Sort shipments based on delivery zones and carriers
- Use automated systems for warehouse label printing and tracking
- Optimize carrier selection for cost and speed efficiency
- Monitor shipments in real-time for proactive issue resolution
10. Reverse Logistics: Handling Returns & Exchanges
Returns are inevitable, but a well-structured reverse logistics process minimizes losses and improves customer satisfaction. Efficient return handling involves quality inspection, restocking, or refurbishing returned items. Data from returns can also help businesses identify recurring product issues and refine inventory management.
- Inspect returned items for damage and resale potential
- Automate refund or exchange processing to improve speed
- Track return reasons to identify product quality issues
- Minimize waste by reselling, repackaging, or recycling returned goods
Read More: Top Returns Management Softwares 2025
6 Most Important Benefits of Warehouse Management
A warehouse is more than just storage—it’s the heartbeat of an efficient supply chain. When managed strategically, it reduces costs, speeds up fulfillment, and turns logistics into a competitive advantage. By optimizing workflows and inventory, businesses don’t just meet demand—they stay ahead of it.
1. Faster Order Fulfillment & Improved Customer Satisfaction
When warehouse operations run smoothly, orders move faster from storage to shipping, ensuring customers receive their purchases on time—or even earlier than expected. This efficiency reduces delays, prevents shipping errors, and enhances overall customer experience, leading to stronger brand loyalty.
Optimized picking, packing, and inventory tracking also minimize order processing time. This means businesses can handle higher order volumes without compromising speed or accuracy, giving them a competitive edge in fast-moving markets.
2. Reduced Operational Costs & Better Space Utilization
A cluttered, disorganized warehouse leads to wasted space and unnecessary expenses. Effective warehouse management focuses on smart storage solutions, ensuring that every inch of space is used efficiently. This prevents overstocking, reduces handling costs, and keeps operations running lean.
By implementing strategic inventory placement and automation, businesses can also cut down on labor inefficiencies. Employees spend less time searching for products, reducing overall operational costs and maximizing productivity.
3. Accurate Inventory Tracking & Stock Control
Nothing hurts a business more than stockouts of best-selling items or excessive inventory of slow-moving products. Proper warehouse management ensures real-time inventory tracking, preventing costly mistakes and improving demand forecasting. With better visibility into stock levels, businesses can make informed purchasing decisions.
Advanced tracking tools like barcodes, RFID, and warehouse management systems (WMS) help maintain inventory accuracy. This reduces errors, enhances order fulfillment rates, and prevents revenue loss due to mismanaged stock.
4. Stronger Supply Chain Resilience & Efficiency
Warehouses are a critical link in the supply chain, and disruptions can have ripple effects across the entire operation. Efficient warehouse management ensures a well-coordinated flow of goods, reducing delays and optimizing inbound and outbound logistics. This makes supply chains more agile and responsive to demand fluctuations.
By improving supplier coordination and implementing proactive problem-solving strategies, businesses can mitigate risks such as delivery bottlenecks, unexpected shortages, or supply chain disruptions. This resilience is essential in today’s unpredictable market conditions.
5. Increased Workforce Productivity & Workplace Safety
A well-organized warehouse minimizes unnecessary movement, making tasks easier and faster for employees. Optimized workflows, clear labeling, and automated systems reduce the time spent locating, picking, and packing products, allowing workers to focus on efficiency rather than overcoming logistical obstacles.
Additionally, effective warehouse management prioritizes safety by ensuring proper training, equipment use, and adherence to safety regulations. Fewer workplace accidents lead to a healthier workforce and fewer operational disruptions, contributing to long-term business success.
6. Efficient Multi-Warehouse Management for Scalability
As businesses grow, managing multiple warehouses becomes essential for optimizing inventory distribution and reducing shipping times. A well-structured multi-warehouse strategy ensures stock is strategically placed across locations, allowing orders to be fulfilled from the nearest facility. This minimizes transit times, lowers shipping costs, and improves delivery speed—critical factors for meeting customer expectations.
With centralized inventory tracking and automation tools, businesses can synchronize stock levels across multiple warehouses, preventing overstocking in one location while another runs out of stock. Effective multi-warehouse management enhances operational flexibility, supports expansion into new markets, and ensures a seamless supply chain, even during peak demand periods.
Modern Strategies For Warehouse Management in 2025
Warehouse management is evolving faster than ever, and in 2025, efficiency isn’t just an advantage—it’s a necessity. The key to staying ahead? Smarter automation, sharper inventory control, and a efficiet workforce. Here’s how you can turn your warehouse into a well-oiled machine this year:
1. Let AI and Automation Do the Heavy Lifting
Robots and AI aren’t just futuristic buzzwords—they’re the secret to faster, error-free operations. AI-powered demand forecasting, automated picking systems, and smart sorting can drastically cut labor costs and improve accuracy.
- Predict demand spikes before they happen to avoid stockouts
- Use robots to handle repetitive tasks like sorting and picking
- Automate barcode scanning and order processing to speed things up
2. Master the Art of Multi-Warehouse Management
Juggling multiple warehouses? Keeping inventory in sync is no easy task. A smart warehouse management system (WMS) can help balance stock, route orders faster, and reduce storage costs across all locations.
- Sync inventory in real-time to prevent overstocking or shortages
- Ship from the nearest warehouse to cut delivery times
- Optimize storage layouts to free up space for high-demand items
3. Stop Guessing—Use Data to Keep Inventory in Check
Running out of bestsellers or sitting on slow-moving stock? Real-time analytics, IoT sensors, and AI-driven demand forecasting make inventory control smarter, reducing waste and freeing up capital.
- Track stock levels with IoT-enabled sensors for real-time updates
- Use AI to predict reorder points and optimize restocking
- Prioritize high-value items using ABC analysis for smarter stocking
4. Make Every Square Foot Count with Smarter Layouts
A poorly organized warehouse slows down workers and wastes space. Slotting optimization, vertical racking, and smart storage solutions can improve efficiency and reduce travel time inside your facility.
Store fast-moving products where pickers can grab them quickly
Use vertical storage to maximize space without expanding footprint
Reduce congestion by designing better picking routes and workstations
5. Upgrade Your Workforce with Smart Tech
Warehouse labor is expensive—so why not make every shift more productive? Wearable devices, voice-directed picking, and augmented reality (AR) can boost worker efficiency and reduce training time.
- Equip workers with AR glasses for hands-free picking instructions
- Use voice-picking systems to increase speed and minimize errors
- Automate shift scheduling to improve productivity without burnout
6. Fix Returns Faster and Save on Reverse Logistics
With online returns at an all-time high, an efficient returns process is a must. AI-powered assessments and automated sorting systems help reduce losses, recover value, and improve resale potential.
- Automate quality checks to speed up return processing
- Resell or refurbish returned items to reduce waste
- Streamline return workflows to minimize costs and delays
7. Go Green and Cut Costs with Sustainable Warehousing
Sustainability isn’t just good for the planet—it’s good for business. Energy-efficient warehouses, smarter transportation routes, and waste reduction can slash costs and future-proof operations.
- Switch to LED lighting and energy-efficient HVAC systems
- Use eco-friendly packaging to reduce waste and shipping costs
- Adopt carbon-neutral shipping options to meet sustainability goals
8. Use Predictive Maintenance to Prevent Downtime
Broken equipment or unexpected failures can bring warehouse operations to a halt. Predictive maintenance uses AI and IoT sensors to track equipment health and prevent costly breakdowns before they happen.
- Install IoT sensors on forklifts, conveyors, and machinery
- Use AI-driven maintenance scheduling to fix small issues early
- Minimize downtime and avoid costly emergency repairs
9. Streamline Last-Mile Delivery for Faster Fulfillment
A fast warehouse means nothing if last-mile delivery is slow. Route optimization, real-time tracking, and local fulfillment hubs can make sure customers get their orders on time.
- Use AI-powered route planning to cut down delivery times
- Offer real-time tracking updates for better customer experience
- Set up micro-fulfillment centers in high-demand areas
10. Tighten Security with Smart Access Control & Monitoring
Warehouses handle valuable inventory, making security a top priority. AI-powered surveillance, biometric access control, and real-time tracking can prevent theft and unauthorized access.
- Install AI-driven cameras for real-time monitoring
- Use biometric access for restricted warehouse zones
- Track high-value items with RFID for extra security
The Components of Warehouse Management
On the surface, the warehouse management process can seem straightforward; it begins with receiving a product in the warehouse and ends with shipping it to the end consumer. However, once you peel back all the layers, there are lots of moving parts working in tandem.
The most important components of warehouse management can be broken down into the following:
1. Warehouse Operations
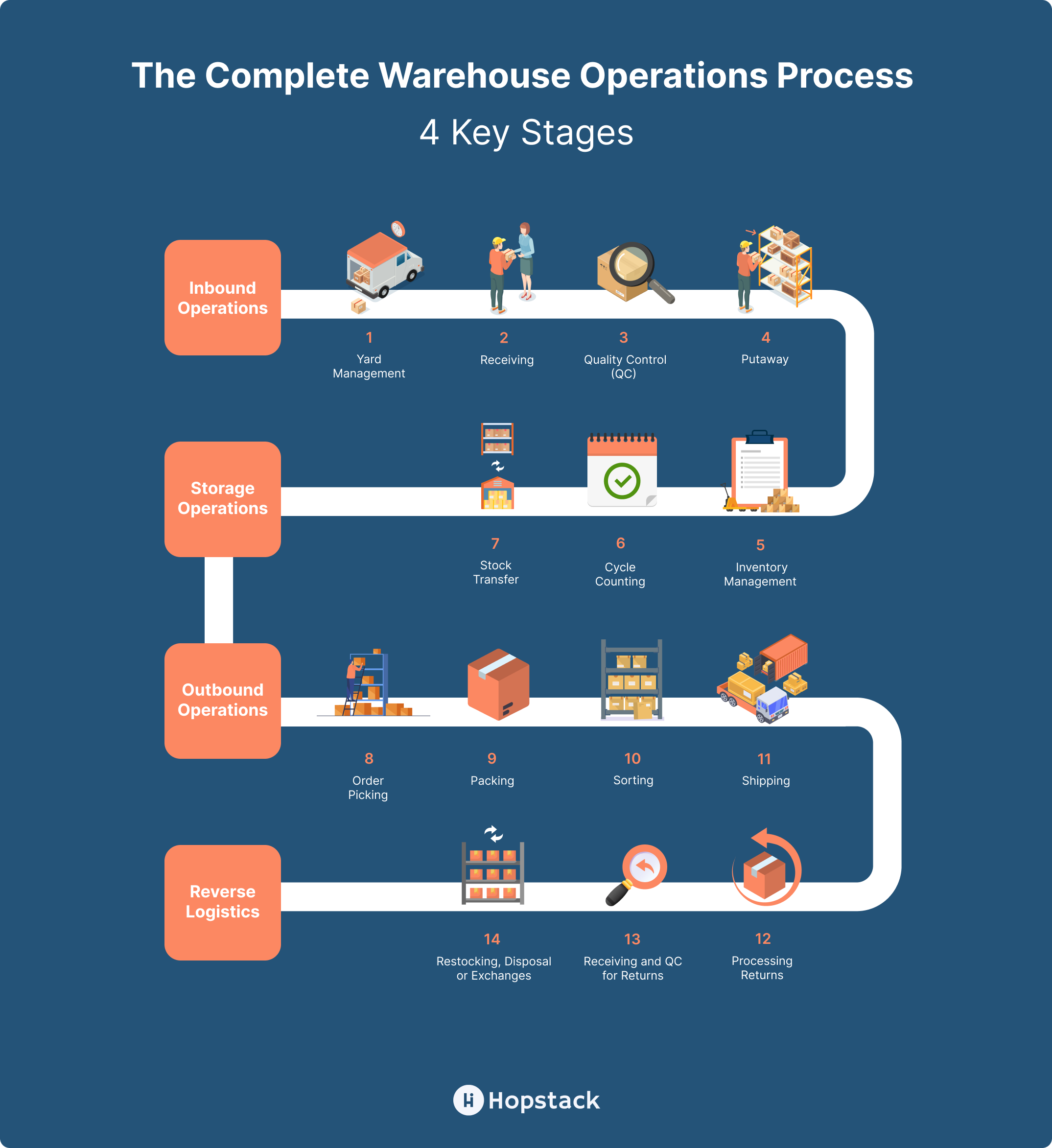
Warehouse operations include a wide range of tasks and activities that facilitate the day-to-day functionalities within a warehouse. These activities can be broadly categorized within inbound, storage, and outbound operations. While we will go deeper into these individual operations later on in the guide, let’s first understand the process itself.
Inbound Operations
Inbound operations serve as the entry point of a warehouse’s role in the supply chain, focusing on the seamless and accurate integration of products. This phase involves receiving goods from suppliers or manufacturers, conducting inspections for quality and accuracy, and strategically placing these items in designated storage locations through a process known as putaway.
Effective inbound operations are foundational, laying the groundwork for accurate inventory levels and optimal storage configurations. This is essential for enabling efficient, error-free warehouse operations that are critical for swiftly and reliably meeting customer demands.
Storage Operations
Storage operations in a warehouse are designed to maintain optimal inventory levels, striking a balance between space utilization and the quick, accurate retrieval of products. Key activities include regular cycle counting to verify inventory accuracy, strategic stock transfers to optimize space and picking routes, and comprehensive inventory management to balance product availability with the costs of holding inventory.
Storage operations are pivotal to warehouse efficiency, ensuring that goods are accessible and ready for fulfillment, thereby preventing stockouts or overstock situations.
Outbound Operations
Outbound operations in a warehouse are centered around the accurate and timely delivery of products to the end customer or the next stage in the supply chain. In combination with the inbound and storage processes, outbound operations contribute directly to customer satisfaction.
Core activities include picking products based on customer orders, securely and efficiently packing those products, sorting them according to their final destination, and ultimately shipping them out of the warehouse.
Outbound operations are paramount, as they deliver tangible results to the end customer through precise, timely, and undamaged shipments. The success of the entire warehouse operations chain depends on the effectiveness of outbound processes.
2. Layout and Design Principles
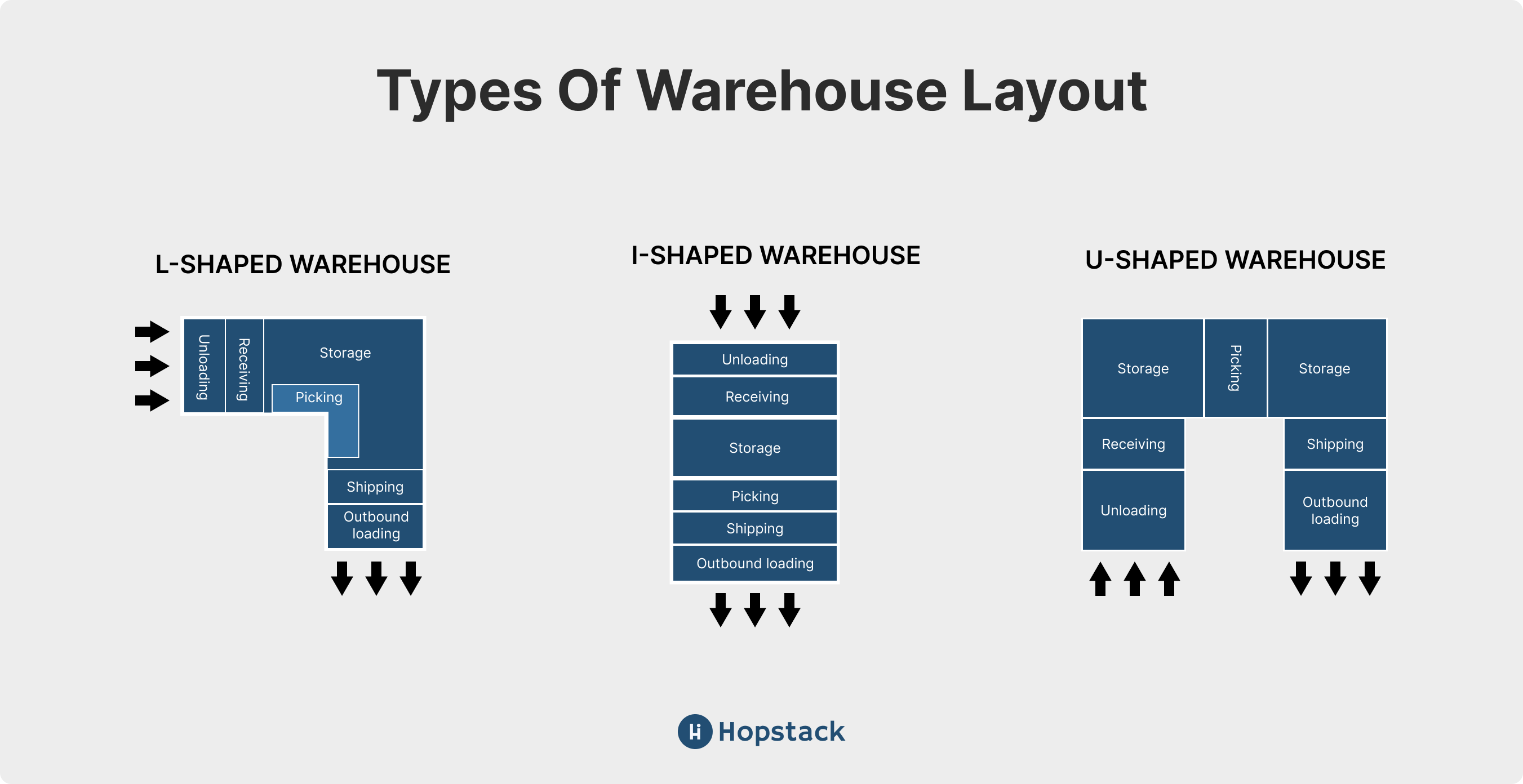
The layout and design of a warehouse are fundamental to maximizing its efficiency. A well-designed warehouse can improve productivity by reducing travel time between different operations, improving the flow of goods, and making the best use of available space.
1. Maximizing Storage Yield
The primary function of a warehouse is storage. The layout should utilize the vertical and horizontal space efficiently to maximize storage capacity without hampering the movement. According to a survey by Modern Materials Handling, the average warehouse space utilization for 2022 was 85.6%.
While the available space within a warehouse will always be constant, the goal is to maximize the economic benefit from that space. Adjustable racking systems, multi-tier racking, and modular shelving can be deployed. It's also important to consider the type of goods stored, their sizes, weights, and frequency of access.
2. Facilitating Smooth Flow of Goods
A logical flow reduces travel times, minimizes potential bottlenecks, and speeds up receiving, storing, picking, and shipping processes. Place receiving and dispatch areas close to each other but without interference. Organize aisles and pathways to allow for intuitive movement and consider a U-shaped flow for goods.
3. Flexible Design
Warehouses need to be adaptable to changing business needs, seasonal demand fluctuations, and evolving inventory profiles. Modular shelving and racking that can be easily reconfigured, scalable storage solutions, and zones that can be repurposed based on demand.
4. Safety Considerations
Safety is paramount in warehouse operations. A well-designed layout minimizes the risk of accidents, protects employees, and ensures regulatory compliance. According to the U.S. Bureau of Labor Statistics, private industry employers reported 2.6 million nonfatal workplace injuries and illnesses in 2021. Out of these, transportation and warehousing industries reported 253,100 cases of nonfatal workplace injuries.
Consider implementing wide aisles to prevent congestion, proper signage, designated areas for equipment charging or maintenance, and clear evacuation routes.
5. Technology Integration
Modern warehouses increasingly rely on technology, from warehouse management systems (WMS) to robotics. The layout should facilitate the smooth integration and operation of these technologies. Ensure that the design allows for the movement of robots or automated guided vehicles (AGVs). Factor in spaces for charging stations, and ensure WiFi coverage is uniform throughout the warehouse for real-time inventory tracking.
3. Inventory Control Techniques
Optimal inventory management is crucial to the success of any warehouse. This involves ensuring inventory velocity (the speed at which items move through the warehouse), regular replenishment of stocks, and maintaining an accurate record of inventory levels. There are various techniques to help achieve this, such as ABC analysis, Just-in-Time (JIT), and Economic Order Quantity (EOQ) — these can be used to supplement existing inventory management processes.
A few critical factors that influence inventory management are:
- Inventory Storage and Tracking: Proper inventory storage ensures that products are accessible, reducing retrieval times and enhancing operational efficiency. Efficient tracking, on the other hand, ensures real-time updates on stock levels, enabling accurate replenishment forecasts and reducing the chances of stockouts or overstock situations. Effective storage and tracking lead to optimized inventory levels, faster order fulfillment, and reduced wastage due to expired or obsolete inventory.
- Stock Supervision: Supervising stock involves monitoring current stock levels and understanding stock movement patterns. A clear grasp of which products move quickly (and which don't) allows warehouse managers to adjust storage strategies, ensuring that high-turnover items are more accessible. Proper stock supervision results in reduced carrying costs and decreased chances of dead stock.
- Creating and Validating Purchase Orders: Purchase orders (POs) dictate what inventory comes into the warehouse. Creating accurate POs ensures that only the necessary stock is ordered. Validating these orders ensures that discrepancies between ordered and received goods are minimized, keeping inventory levels accurate.
- Receiving and Putaway: The process of receiving determines how the new stock is integrated into the existing inventory. Efficient putaway ensures that items are stored in the right locations, making future retrievals faster and more accurate. An organized and error-free receiving and putaway warehouse process ensures that inventory levels in the management system match the physical stock in the warehouse.
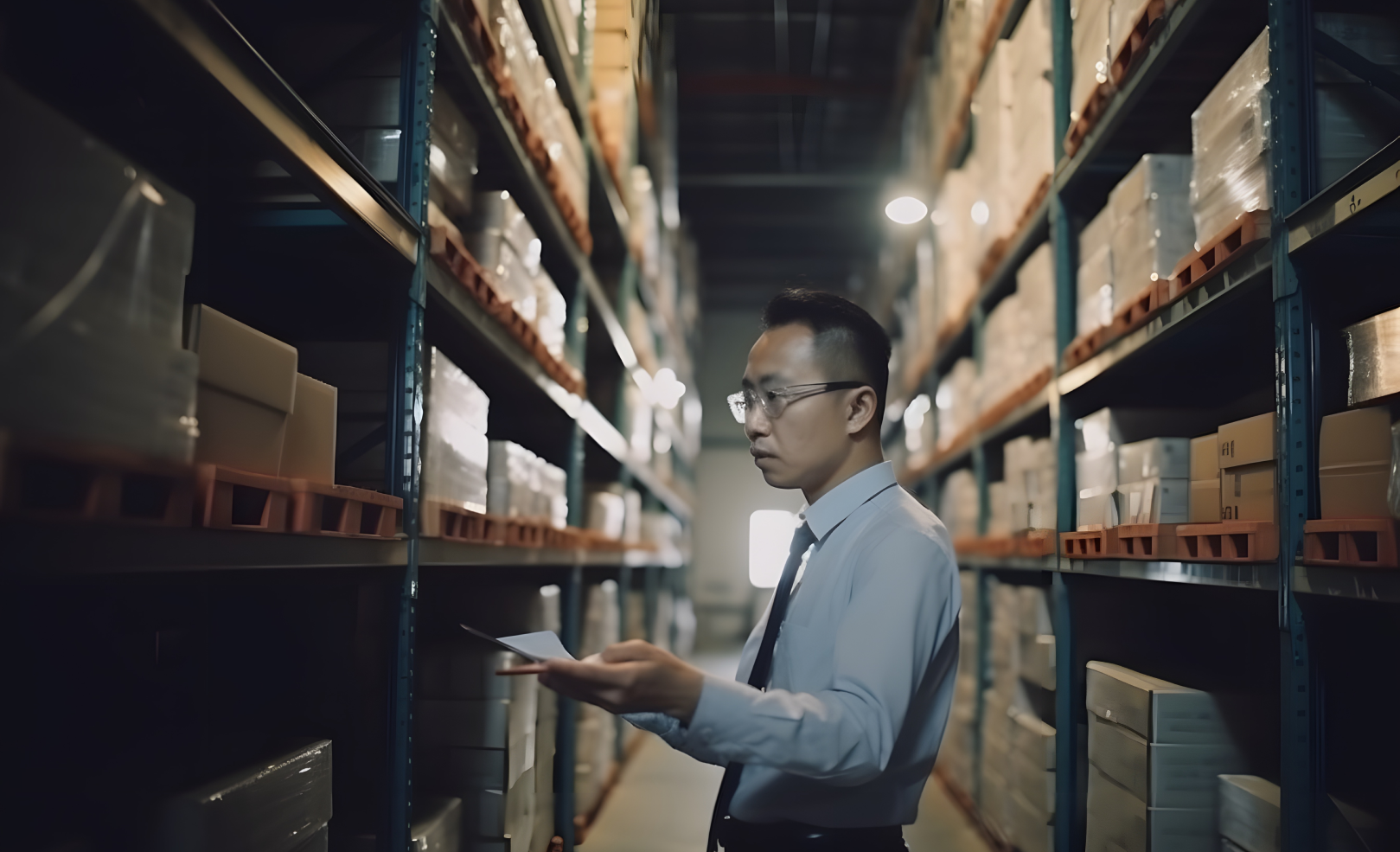
Inventory management is like a well-orchestrated dance, where each factor plays a role in ensuring the movement flows seamlessly. From knowing where items are stored, to ensuring the right items are in stock, to ordering and receiving new stock efficiently—each step affects the overall efficiency, accuracy, and profitability of the overall warehouse management system.
4. Labor Management
The labor force is often the largest expense in a warehouse, and its productivity directly affects the bottom line. This involves ensuring that there is enough staff to handle the workload, that they are well-trained and productive, and that they are compensated fairly.
Matching Labor to Demand: Labor needs can fluctuate based on seasonal demands, promotional activities, and other market variables. Proper planning ensures that there's neither a shortage nor an excess of labor at any given time. By aligning the workforce size with the operational demand, costs can be optimized, overtime reduced, and worker fatigue minimized, leading to increased overall productivity.
Skill Development and Training: As warehouse technologies and processes evolve, workers need to adapt and upgrade their skills to stay relevant and efficient. Trained workers make fewer mistakes, are more efficient, and can handle a wider range of tasks.
Effective Task Allocation: Not all warehouse tasks are the same; some might require specific skills or expertise, while others are more generic. Running a forklift might require more training and expertise than effectively using barcode scanners. Properly matching tasks to workers based on their skills and strengths optimizes productivity. Similarly, continuous and intelligent task allocation should factor in individual worker productivity levels to ensure there are no lulls in performance.
Safety and Well-being: A safe warehouse is not just a regulatory requirement but also a productivity booster. Fewer accidents mean less downtime, reduced compensation costs, and higher morale among workers. A focus on well-being can also reduce turnover and associated hiring and training costs.
Interoperability in Warehousing: Technologies like warehouse management systems (WMS), wearables, and labor management software can simplify warehousing activities and help in task allocation. On the other hand, these technologies can assist in monitoring worker performance, identifying bottlenecks, and reallocating resources in real time. However, there should be a seamless handshake between warehouse technologies and workers to maximize their effectiveness within the warehousing ecosystem.
5. Safety and Compliance
Safety is a critical concern in warehouses, which often involve heavy goods and machinery. Warehouses should be designed with safety in mind and equipment such as forklifts and conveyors must be properly maintained and used correctly.
1. Prevention of Accidents and Injuries
Warehouses can be high-risk environments, with heavy machinery, elevated platforms, and constant movement of goods. Proactively addressing safety issues and providing labor training reduces the frequency of accidents, leading to fewer workplace accidents and minimal operational disruptions, leading to greater morale among warehouse associates.
2. Enhanced Productivity
A safe warehouse environment ensures that employees can work without fear of injury. When they trust that their safety is a priority, morale and productivity improve. According to a survey by YouGov on behalf of StrongArm Technologies, almost 50% of respondents working in the manufacturing, warehousing, construction, and transportation industries feel stressed in their current job.
3. Regulatory Compliance and Avoidance of Penalties
Regulatory compliance is also crucial, with businesses needing to adhere to regulations related to aspects like fire safety, hazardous materials, and worker protection. Compliance avoids costly penalties, legal ramifications, and potential shutdowns. Moreover, a compliant facility can often negotiate better terms with insurers, leading to reduced insurance premiums.
Key Stakeholders in Warehouse Management
The warehousing management ecosystem engages a great many stakeholders that oversee and participate in everyday activities and overall decision-making. We can group them into a few broad categories:
1. Logistics and Warehousing Leadership
This team is typically responsible for formulating and driving the overall logistics strategy, which includes decisions on warehouse locations, the structure of the warehouse network, supplier partnerships, and more. They're often involved in high-level planning and decision-making, such as budgeting, investment in technology, risk management, and strategic partnerships.
2. Warehouse Managers
The warehouse manager oversees and executes daily operations within the warehouse. They allocate tasks to warehouse associates, ensure that operations run smoothly, and solve any issues that might arise. They identify bottlenecks in processes, ensure workforce productivity, and maintain standards of safety and compliance. They are also often involved in worker training, inventory management, and customer service.
3. Warehouse Associates
These are the individuals who carry out the day-to-day operations within the warehouse. Roles may include receivers who accept incoming goods, pickers who collect items for outgoing orders, packers who prepare items for shipment, and workers who carry out tasks like cycle counting and stock transfers. Their efficiency and accuracy are critical to the warehouse's overall performance.
4. Freight Companies and Carriers
These stakeholders are crucial as they provide the transportation that links the warehouse to suppliers and customers. They can be responsible for both inbound (delivery of goods from suppliers to the warehouse) and outbound (shipment of goods from the warehouse to the customers) logistics. Their reliability and efficiency can greatly affect the warehouse's ability to maintain inventory levels and meet customer delivery expectations.
5. 3PL Clients (Only Relevant for 3PL Providers)
Third-party logistics (3PL) providers offer outsourced logistics services, including warehouse management services. For these providers, the clients who send their inventory for storage and fulfillment are key stakeholders. These clients require high visibility into their consignments, inventory levels, orders, and more, necessitating effective communication and data sharing between the 3PL provider and the client.
.png)
6. Consumers
While not directly involved in warehouse management, the end consumer is an important stakeholder as they are the final recipient of the goods and their experience can be greatly impacted by warehousing activities.
Factors such as delivery speed, accuracy of orders, reverse logistics, and the condition of goods upon arrival are all influenced by the efficiency and accuracy of warehouse operations. Furthermore, consumers' buying habits and expectations can drive changes in warehousing and logistics strategies.
In conclusion, each of these stakeholders plays a critical role in the warehousing and fulfillment lifecycle. Effective warehouse management involves not only the efficient execution of operations within the warehouse but also effective interaction and cooperation between these various stakeholders.
Essentials of Effective Warehouse Management
This takes us to the big question — what does it take to effectively manage warehouse operations at scale? In order to be effective, any warehouse management solution or system has to be capable of supporting the various components and activities that we have discussed so far.
Process Optimization
A core capability of any warehouse management solution is to streamline both inbound and outbound processes. This includes everything from goods receipt and storage to order picking, packing, and shipping.
Why is it important: Process optimization is critical for extracting the highest possible yield from labor, resources, and time. This heightened efficiency is critical in today's fast-paced commerce landscape, where swift, precise, and error-free operations are non-negotiable for meeting increasingly high customer demands.
Real-time Performance Analytics
The ability to track and measure performance in real time allows warehouse managers to make informed decisions on-the-fly. Metrics can be viewed at various levels — from the overall warehouse down to individual products and worker performance.
Why is it important: Insights at the warehouse, station, associate, sales channel, and product levels allow for immediate identification of bottlenecks, inefficiencies, or other issues, enabling warehouse managers to adopt a proactive approach to warehouse management.
Labor Productivity
Labor is the heart of your warehouse operations. It’s crucial to ensure that employees are efficient and effective in their roles and simultaneously identify potential areas of improvement.
Some essential metrics and KPIs to measure labor productivity include:
- Pick Rate: Number of items picked per hour
- Dwell Time: Time taken from order receipt to dispatch
- Utilization Rate: Percentage of time an employee is productive
Why is it important: The productivity of the human workforce directly impacts the warehouse's throughput, cost-efficiency, and profitability.
Software and Robotic Automation
Automation has been a game changer across most industry verticals even more relevant for warehouse management. Traditionally, warehouse management processes have been labor-intensive — this drove the adoption of process-driven automation at scale.
Why is it important:
- By automating tasks like data entry and inventory tracking, warehouse management solutions ensure data accuracy, faster processing, and reduced manual errors.
- Robotic solutions such as Automated Storage and Retrieval Systems (ASRS), picking robots, Automated Mobile Robots (AMRs), and conveyor belts enhance speed, accuracy, and safety. These systems complement the human workforce, leading to more efficiency through synergy.
Optimal Space Utilization
Warehousing space is expensive, and maximizing its utility is crucial for profitability.
Why is it important: An intelligent warehouse management solution can determine optimal storage solutions, considering factors like product demand, size, and perishability. It can also analyze the warehouse design and layout to recommend smart pick paths and storage recommendations for maximum speed and efficiency.
Cost and Overhead Reduction
With the intense competition and thin margins in logistics, cost-efficiency is paramount.
Why is it important: Through the combined effects of labor productivity, automation, and space utilization, a modern WMS directly contributes to a significant reduction in operational costs.
Ecosystem Capabilities
Warehousing does not operate in isolation. It's a cog in the larger machine of the supply chain. A warehouse management solution can integrate with ERP, TMS, or BI software to provide insights into the health of your warehouse management processes. This includes:
- Predicting stock levels
- Demand forecasting
- Guidance on storage practices
- Support for warehouse pickers and packers
Why is it important: A successful WMS integrates seamlessly with other systems in the supply and commerce chains. Real-time synchronization of inventory, orders, labor, billing, and transport manifests ensures that the entire ecosystem operates in sync, reducing errors, delays, and costs.
Warehouse Management Systems (WMS): What to Expect
As we have already seen, embracing technology has become essential to streamline operations, enhance accuracy, and meet the increasing demands of today’s global commerce. Technologies in warehouse management are designed to integrate, automate, and optimize the complex array of functions that a modern warehouse performs.
Warehouse management systems (WMS) are a central piece of this technological puzzle — engineered to optimize the end-to-end journey of order fulfillment. These systems provide unparalleled visibility at every step of the warehouse management process, from the moment a product enters the warehouse until it is shipped to the end consumer.
Depending on the type of deployment or operational model, there are various types of WMS in use today, each tailored to meet specific warehousing needs.
Types of Warehouse Management Systems
Functions of a Warehouse Management System
- Inventory Control: Monitoring and managing inventory levels, locations, and turnover.
- Order Fulfillment: Handling the entire order-to-shipment process, including picking, packing, and shipping.
- Receiving and Putaway: Managing the intake of goods, their inspection, and placing them in appropriate storage locations.
- Labor Management: Allocating and optimizing human resources for various warehouse tasks and tracking productivity.
- Space Utilization: Optimizing storage space for efficient product placement and retrieval.
- Yard Management: Coordinating the movement and storage of vehicles and trailers in the warehouse yard.
- Reporting and Analytics: Providing insights into warehouse operations, performance metrics, and trends.
- Integration Capabilities: Integrating with other systems like ERP, TMS, and e-commerce platforms for end-to-end visibility into order fulfillment.
- Safety and Compliance: Ensuring all operations adhere to industry regulations and safety standards.
- Reverse Logistics: Managing the process of returns, repairs, recycling, and disposal.
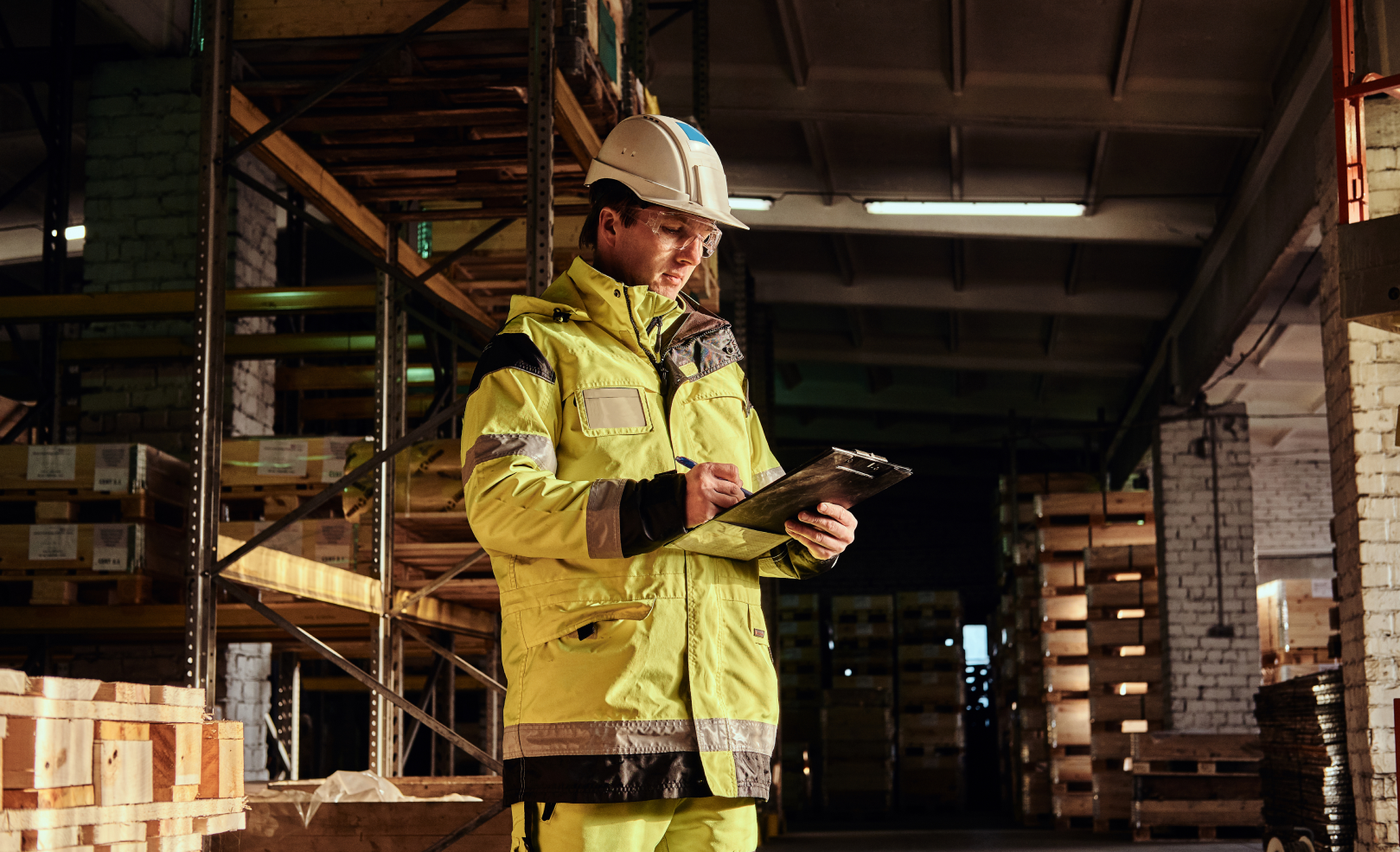
Future of Warehouse Management
Both warehouse management and warehouse management systems have come a long way in quite a short period of time. So let’s take a look at what to expect in the future from warehouse management solutions.
Smarter Warehouse Management Through Automation
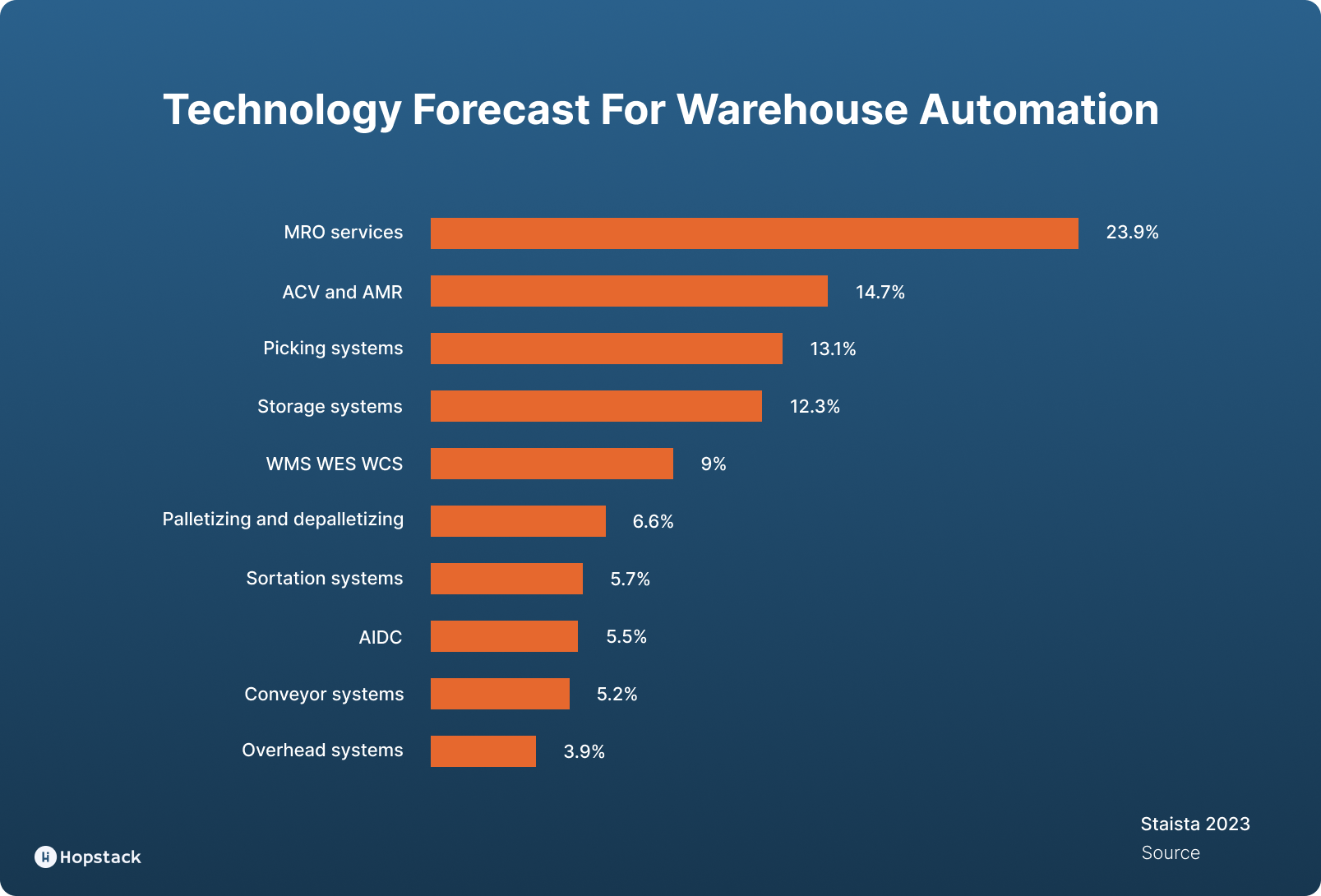
Slowly, but steadily, Smart warehouse technology has been seeping into traditionally labor-intensive processes. It’s no longer limited to simple product tracking or recordkeeping tasks. Today’s warehouse management systems can integrate with automated guided vehicles, autonomous mobile robots, drones, and cobots to assist in day-to-day warehouse activities.
Even as we speak, there are autonomous drones capable of using geolocation data to prepare a real-time digital image of the warehouse. Scanned barcodes and inventory storage data will provide your warehouse associates with smart insights into inventory analysis and picking paths and order picking strategies in warehouse for maximum productivity.
Similarly, robots that work alongside humans, or cobots, can learn to understand human gestures for greater collaboration inside the warehouse.
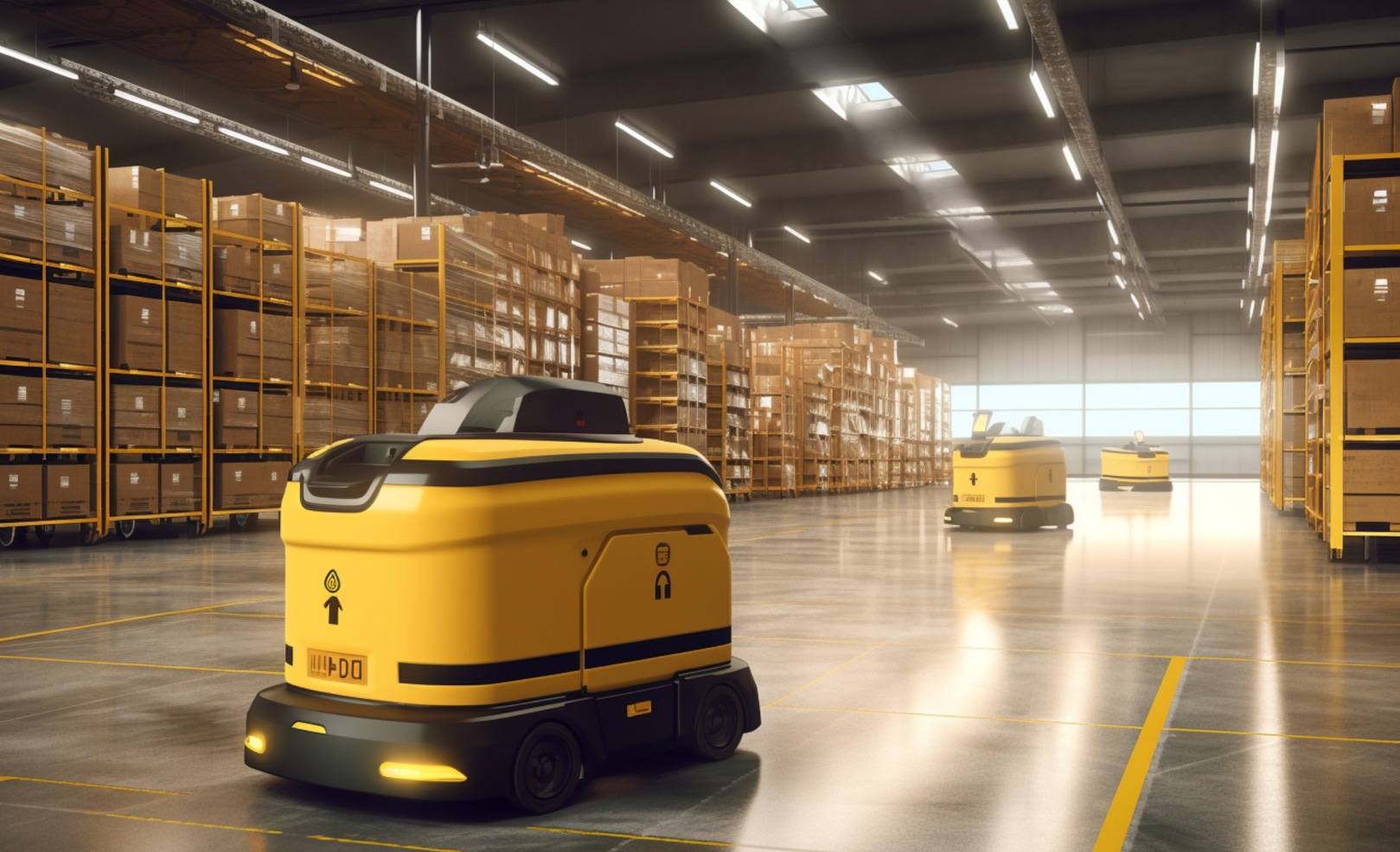
Artificial Intelligence and Machine Learning in Warehousing Environments
The use of AI/ML in the warehouse environment is not a new development in warehouse management. For quite some time, modern warehouse management systems have been capable of using AI/ML for data analysis and predictive insights. These include recommendations for storage practices, inventory tracking, workforce management, predictive maintenance, demand forecasting, and more.
However, the recent focus on AI is leading to significant advancements in warehouse management services. It’s now possible to extract even more granular insights from real-time evaluation of warehouse data and product performance. This includes predicting future demand patterns and using algorithms to improve labor productivity.
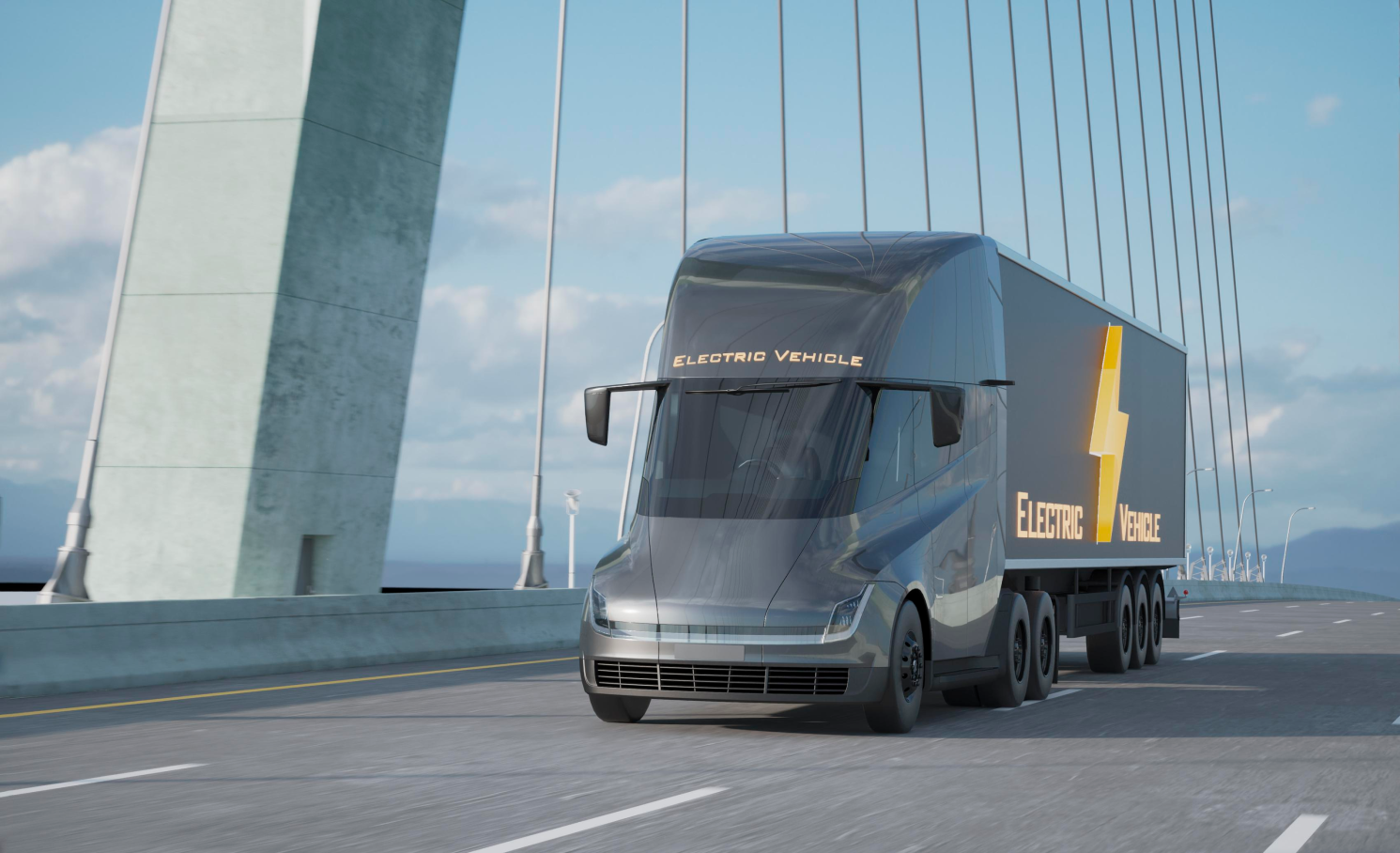
The shift towards sustainability and environmental stewardship is featuring very prominently within self-regulating business models and CSRs. With businesses focusing more on transparency and accountability, sustainability has become a measure of trust to key stakeholders.
Next Steps
Warehouse management is a task of massive proportions. However, with the right technology, it’s possible to address many of the pain points and ensure all the different components are working in conjunction with each other.
While technology has been making things easier, the increased demand has been creating more problems and bottlenecks as well. Therefore, the key is to not become complacent. It’s a matter of securing buy-in from the various stakeholders and using warehouse management systems to pave your road to success. Some warehouse management tips before we conclude — set the right culture, implement the appropriate workflows and learn and innovate continuously.
Warehouse Management FAQs
1. What is warehouse management and why is it important?
Warehouse management is the process of efficiently storing, organizing, and moving inventory to ensure smooth order fulfillment. It’s crucial for reducing costs, improving accuracy, and speeding up deliveries.
2. What are the key components of warehouse management?
The core components include inventory management, order fulfillment, warehouse layout optimization, labor management, and technology integration for automation and tracking.
3. How does a warehouse management system (WMS) work?
A WMS helps track inventory, manage picking and packing, optimize storage, and streamline logistics using automation, real-time data, and AI-powered forecasting.
4. What is a warehouse control system (WCS) vs. a warehouse management system (WMS)?
A WCS focuses on real-time control of automated equipment (conveyors, robots), while a WMS manages overall warehouse operations, inventory, and fulfillment processes.
5. How do I manage inventory across multiple warehouses?
A centralized WMS can help track stock levels across locations, optimize order routing, and balance inventory based on demand trends