Warehouses are the backbone of modern commerce, keeping supply chains running smoothly and ensuring products get where they need to be—fast. But as businesses scale, so do the challenges of managing inventory, streamlining workflows, and maintaining accuracy. In fact, studies show that 43% of small businesses either don’t track inventory at all or use manual methods, leading to inefficiencies and costly errors.
That’s where a Warehouse Management System (WMS) becomes a game-changer. A well-integrated WMS doesn’t just track inventory—it optimizes operations with real-time data analytics, RFID integration, and cloud-based adaptability. The result? Faster order fulfillment, reduced costs, and improved accuracy. With companies that use WMS seeing up to a 25% increase in productivity, investing in the right system isn’t just an option—it’s a competitive advantage.
In this guide, we’ll explore how WMS solutions can transform your warehouse into a high-efficiency powerhouse. Let’s dive in.
What is a Warehouse Management System?
A Warehouse Management System (WMS) is a software solution designed to improve and manage warehouse operations, from the moment goods arrive at a facility to when they are shipped out. It provides real-time visibility into inventory, automates key warehouse processes, and ensures warehouses run efficiently—helping businesses reduce costs, minimize errors, and improve order fulfillment speed.
At its core, a WMS isn’t just about tracking inventory. It’s about optimizing every aspect of warehouse management, including:
- Inventory Control & Tracking – Know exactly what’s in stock, where it’s located, and when it needs replenishing.
- Order Processing & Fulfillment – Automate picking, packing, and shipping to ensure fast, accurate deliveries.
- Labor & Space Utilization – Maximize warehouse layout efficiency and allocate resources effectively.
- Easy & Quick Integration – Connect with ERP, CRM, and Transportation Management Systems (TMS) for a fully synchronized supply chain.
With the rise of omnichannel retail and fast-changing customer expectations, businesses need to be agile. A cloud-based WMS provides real-time access to warehouse data—whether on-site or in transit—allowing companies to adapt to demand fluctuations and improve decision-making.
In a world where 43% of businesses struggle with inventory tracking, and warehouses account for a significant portion of supply chain costs, investing in a WMS isn’t just about efficiency—it’s about staying competitive.
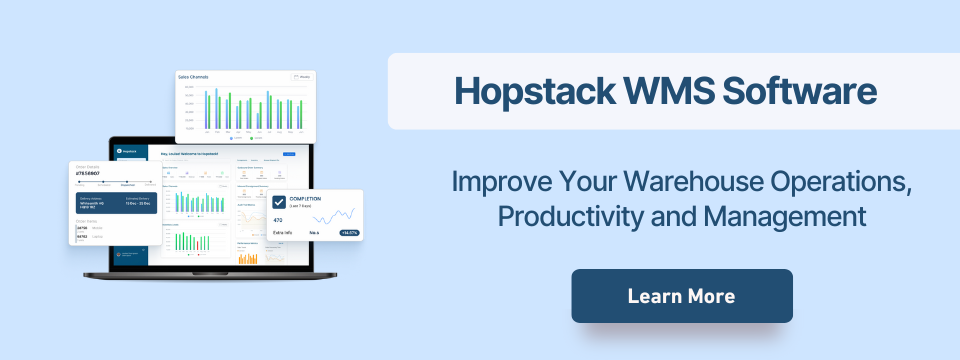
Key Benefits of a Warehouse Management System (WMS)
Explore the key benefits of a Warehouse Management System (WMS), from improved inventory accuracy and cost savings to enhanced automation and scalability. See how a WMS can transform warehouse operations and drive efficiency.
1. Full Digital Transformation = Accuracy and Efficiency
A WMS eliminates outdated, manual warehouse processes by digitizing operations with technologies like RFID tagging, barcodes, and IoT sensors. This means real-time inventory tracking, instant updates, and complete visibility into warehouse operations 24/7.
With accurate, real-time inventory insights, businesses can forecast demand more effectively, optimize stock levels, and run just-in-time strategies—especially critical in cases like recalls or perishable goods management.
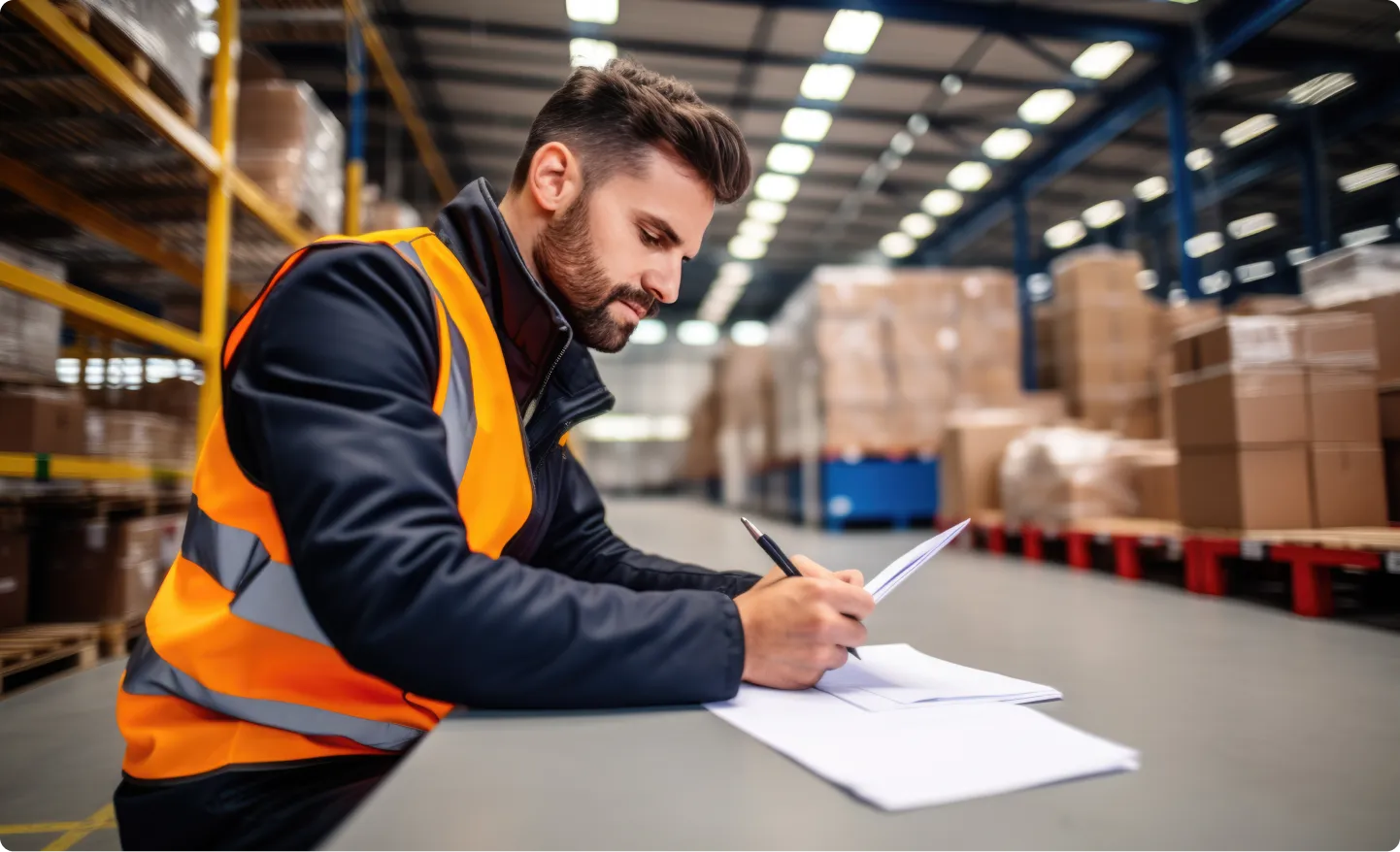
2. Automation That Eliminates Human Errors and Manual Tasks
Traditional warehouse operations relied on spreadsheets, paper logs, and manual data entry—prone to errors and inefficiencies. A WMS automates key tasks such as picklist generation, inventory synchronization, and data validation.
With automation, fulfillment errors decrease, inventory accuracy improves, and warehouse teams can focus on higher-value tasks instead of repetitive manual work. The result? Faster order processing, fewer errors, and a more streamlined workflow.
3. Cost Savings Through Process Optimization
A well-implemented WMS significantly reduces operational costs by optimizing labor, storage, and order fulfillment processes. Through intelligent automation, businesses minimize waste, improve picking strategies, and enhance space utilization.
For example, a WMS can help identify date-sensitive or perishable inventory to prioritize picking and avoid spoilage to effectively manage picking challenges in warehousing. Additionally, leveraging warehouse space efficiently—with vertical storage, optimized layouts, and automated stock movement—helps reduce overall operating expenses.
Fact: In 2024, the average warehouse space utilization was ~88%—highlighting the need for businesses to maximize every inch of available space to stay competitive.
4. Real-Time Operational Visibility
A WMS provides warehouse managers with a 360-degree view of warehouse operations, from inventory movement to performance metrics. This data-driven approach helps identify bottlenecks, track resource utilization, and make proactive decisions to improve workflows.
With historical data analysis and predictive analytics, businesses can anticipate demand shifts, minimize errors, and enhance overall supply chain agility.
5. Integration with Key ERPs, Business Systems
A WMS doesn’t work in isolation—it connects with ERP (Enterprise Resource Planning), TMS (Transportation Management Systems), CRM, accounting software, and online sales channels to create a fully synchronized supply chain.
By eliminating data silos and ensuring a two-way flow of information, businesses can improve efficiency, reduce miscommunication, and gain a unified view of all operations across different departments through these WMS integrations capabilities.
Connected Commerce
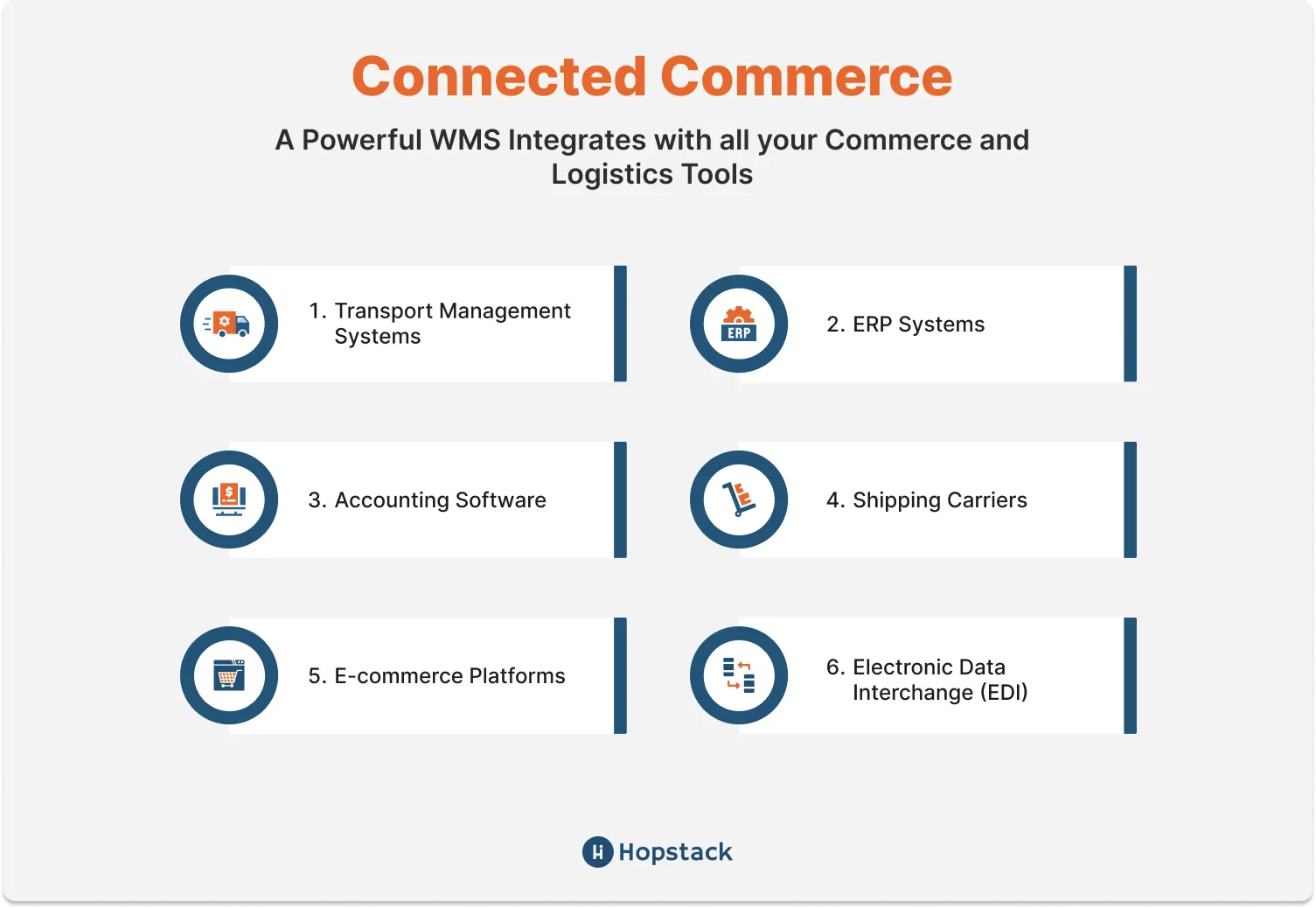
The best warehouse management systems act as the centerpiece in an interconnected network of integrated systems such as TMS (Transport Management Systems), ERP (Enterprise Resource Planning), sales channels, and accounting systems. These WMS integrations facilitate a two-way flow of information. For warehouse managers, this translates to freedom from silos and a unified, single view of truth across all channels and systems.
A connected approach to commerce is essential to adapt to increasing order volumes and capitalize on market opportunities without disruptions.
7. Scalability to Support Business Growth
As businesses expand, manual warehouse processes quickly become unsustainable. A WMS scales effortlessly to accommodate higher inventory volumes, more SKUs, and complex fulfillment demands—without a significant increase in overhead costs.
Cloud-based WMS solutions offer modular flexibility, allowing businesses to add new features and capabilities as needed, ensuring long-term adaptability to market changes, seasonal fluctuations, and evolving consumer demands.
8. Enhanced Security and Compliance Management
Warehouses deal with high-value inventory, regulated goods, and sensitive supply chain data—making security and compliance a priority. A WMS enhances security by implementing user access controls, audit trails, and real-time monitoring to prevent fraud and unauthorized stock movements.
Additionally, businesses handling regulated goods (such as pharmaceuticals or food items) can maintain strict compliance with industry regulations by ensuring proper storage, handling, and tracking of products in line with government requirements.
9. Reduced Shipping and Delivery Times
A WMS speeds up order fulfillment by optimizing picking routes, automating sorting processes, and integrating with carriers for seamless shipping coordination.
By improving warehouse efficiency, businesses can achieve faster turnaround times, reducing lead times and meeting growing customer expectations for same-day or next-day delivery
10. Cloud-Based WMS – Always Up-to-Date, No Upgrades Required
Unlike on-premises systems that require costly updates and IT maintenance, a cloud-based WMS automatically receives regular updates, keeping your system running on the latest software version—without disruptions.
With Software-as-a-Service (SaaS) pricing, there are no expensive upgrades, no infrastructure costs, and no IT maintenance required. It works just like the apps on your smartphone—always up to date, always optimized.
The Evolution of Warehouse Management Systems (1900 to 2025)
From ancient storage houses to today’s high-tech distribution centers, warehouse management has evolved dramatically. The 1960s saw the first Automated Storage and Retrieval Systems (AS/RS), followed by the first real-time WMS in 1974, pioneered by J.C. Penney. Barcoding, introduced in the same era, revolutionized inventory tracking, reducing errors and speeding up fulfillment. By the 1990s, global trade growth fueled the rise of software-driven WMS solutions, enabling businesses to optimize operations like never before.
Today, cloud-based WMS platforms are reshaping logistics, offering real-time visibility, seamless integration, and scalable efficiency—without costly infrastructure. AI, robotics, and predictive analytics are now driving the next wave of innovation. As e-commerce surges, warehouses must adapt with smarter, automated solutions to stay ahead in an increasingly digital supply chain.
Types of Warehouse Management Systems (WMS)
Choosing the right WMS depends on a company’s size, operational complexity, and integration needs. Here’s a breakdown of the four main types of WMS solutions:
1. Standalone WMS
A standalone WMS is a specialized system built solely for warehouse management. It provides essential functions like inventory tracking, picking and packing, and shipping management. While these systems offer strong warehousing capabilities, they typically require separate integrations with other business software, such as Enterprise Resource Planning (ERP) or Transportation Management Systems (TMS). Standalone WMS solutions are ideal for small to mid-sized businesses that need a focused, cost-effective warehouse management tool.
2. WMS Modules in Supply Chain Management (SCM) Systems
A WMS within an SCM system extends beyond warehouse operations to optimize the entire supply chain. These modules enable businesses to coordinate inventory, transportation, and procurement under a unified platform. Ideal for large-scale distribution networks, this type of WMS ensures seamless communication across multiple touchpoints, improving order fulfillment and demand forecasting.
3. WMS Modules in Enterprise Resource Planning (ERP) Systems
For businesses needing an all-in-one operational solution, ERP-integrated WMS modules are the go-to choice. These systems merge warehouse management with finance, HR, procurement, and sales operations, ensuring a synchronized workflow across the entire organization. Best suited for large enterprises, ERP-based WMS solutions provide a single source of truth, streamlining data flow and reducing silos between departments.
4. Cloud-Based WMS
Cloud-based WMS solutions offer real-time access, scalability, and cost efficiency without the need for extensive IT infrastructure. Unlike on-premises systems, cloud WMS eliminates software maintenance costs, ensures automatic updates, and allows businesses to scale as needed. With integrations across multiple platforms and accessibility from anywhere, this type of WMS is ideal for businesses of all sizes, especially those looking to expand or optimize omnichannel fulfillment.
Key Features of Warehouse Management Systems
The following key features of warehouse management systems facilitate efficient order fulfillment, adapt to evolving warehousing demands, and enhance overall efficiency, accuracy, and order fulfillment while sustaining connectivity across the supply chain.
1. Space and Layout Management
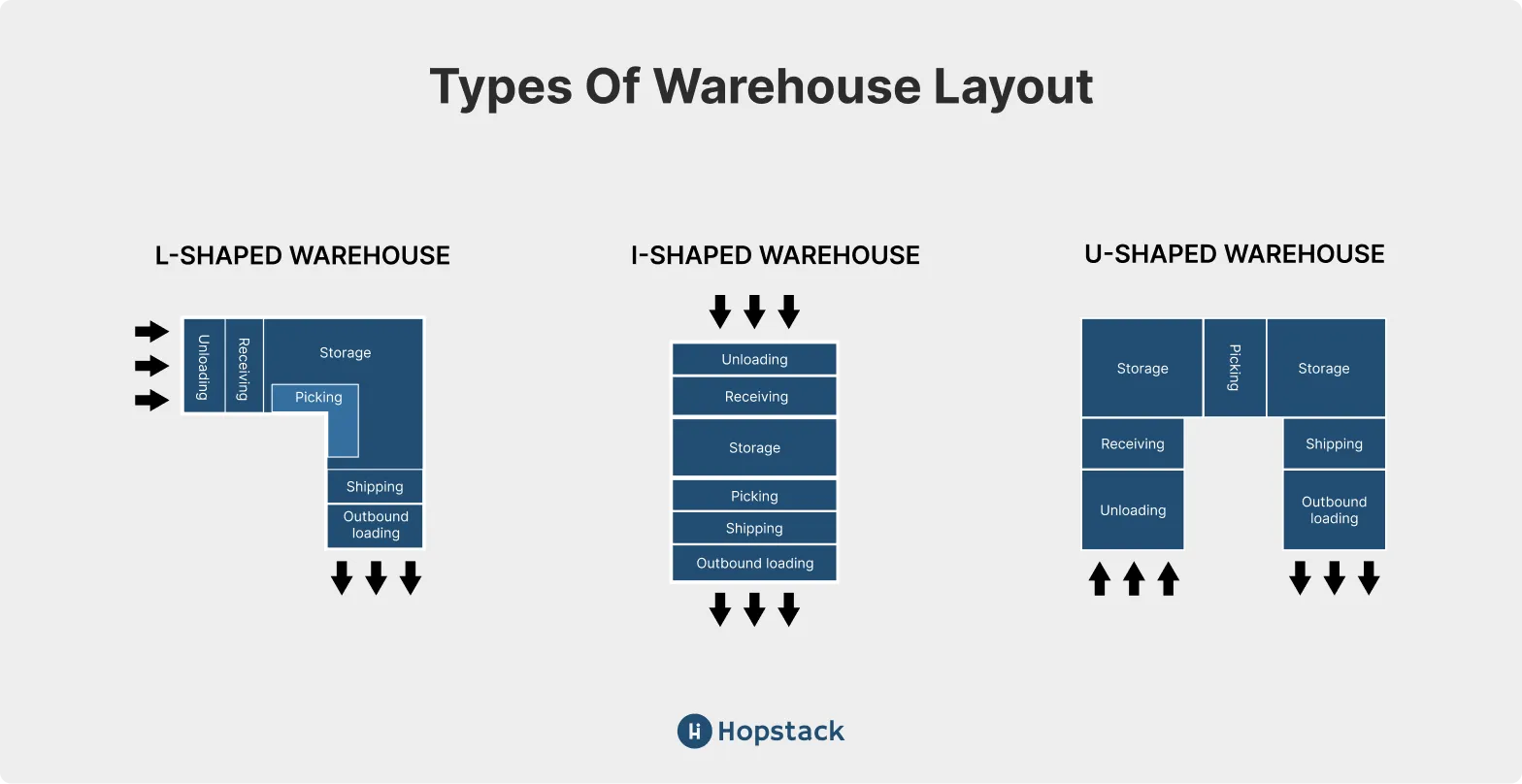
It’s not possible to expand the available volume of warehouse space without additional investment in procurement. However, it is possible to maximize storage yield through precise configuration of the warehouse space.
A WMS allows users to create and define specific storage types, such as bin storage, pallet storage, buffer zones, and more. With access to CAD software for layout design, insights into warehouse layout and optimal space utilization, and IoT sensors for real-time space monitoring, it’s possible to maximize the value of your warehouse space.
Effective space management is crucial to maximize storage capability, streamline the movement of goods, and ensure that products are accessible and easily retrievable.
2. Inventory Optimization
A warehouse management system in logistics offers real-time visibility into a warehouse’s inventory and stock levels, from inbound shipments to storage. Below, we have included a high-level overview of the role of warehouse management system in inventory optimization:
- WMS provides an uninterrupted view of stock levels. This continuous monitoring ensures that inventory is stored appropriately, considering factors like product perishability and priority.
- By leveraging artificial intelligence, the best warehouse management systems can predict future inventory requirements. This forecasting assists warehouses in preparing for demand surges or lulls, ensuring they neither overstock nor run out of essential items.
- Analytics-driven insights assist in maintaining the right balance of stock. Not only does this prevent costly overstocking or stock-outs, but it also ensures products are available when customers need them, boosting overall satisfaction.
- In instances where overstocking does occur, a WMS can recommend strategies for effective liquidation, ensuring minimal losses. Research by Avery Dennison Corp indicates that $163 billion worth of inventory is discarded each year due to expiry or overproduction.
- With a WMS, the tracking of perishable goods becomes streamlined, ensuring products are dispatched and consumed before their expiration. This optimization not only reduces waste but also enhances order fill rates and efficiency.
Inventory optimization is essential to track perishable goods and improve order rates. With rules-based logic tailor-made for your warehouse, you can ensure your orders reach the end consumers on time and without errors.
3. Order Management
A WMS centralizes orders from various sales channels and sets specific fulfillment protocols based on their source and type, ensuring uniformity and accuracy. Integration with order management systems (OMS), EDI for order synchronization, billing, and automated sorting systems can capture and consolidate billables based on a built-in rules engine. This ensures accuracy and transparency in capturing your billables.
Streamlined order management reduces processing time, minimizes errors, and ensures timely delivery to clients. You can retain order history to benchmark product performance and efficiency metrics.
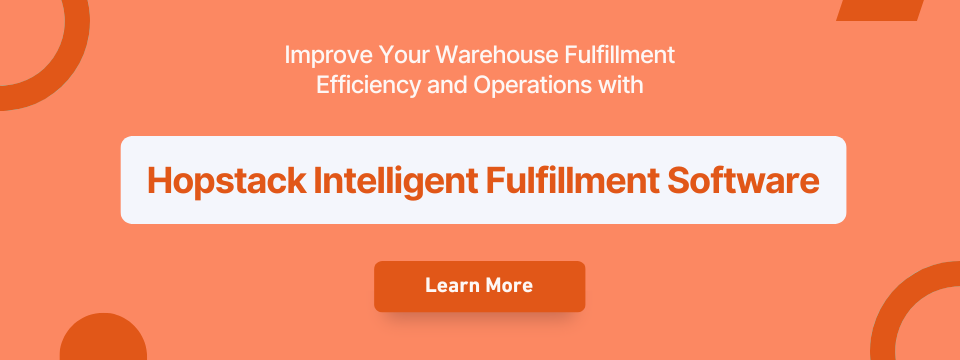
4. Inbound and Outbound Orchestration
The best warehouse management systems orchestrate the entire lifecycle of products in the warehouse, from the receiving phase to shipping. Upon receiving the products, the WMS generates tasks for unloading, prints the appropriate warehouse labels, and guides workers to assigned storage locations. It optimizes the putaway process by identifying suitable locations based on product attributes and storage availability.
The warehouse management system process flow integrates with automated guided vehicles (AGVs) for material movement, conveyor systems for swift transfers, and barcoding systems for accurate tracking. A streamlined process increases throughput, reduces errors, and shortens lead times.
Advanced recommendation engines determine optimal picking strategies based on order characteristics and warehouse layout. Intelligent picking paths and routing systems can guide pickers to the relevant products, reducing errors and inaccuracies. It can communicate with transportation management systems and carriers for accurate rate shopping and shipping coordination.
5. Single Control Tower
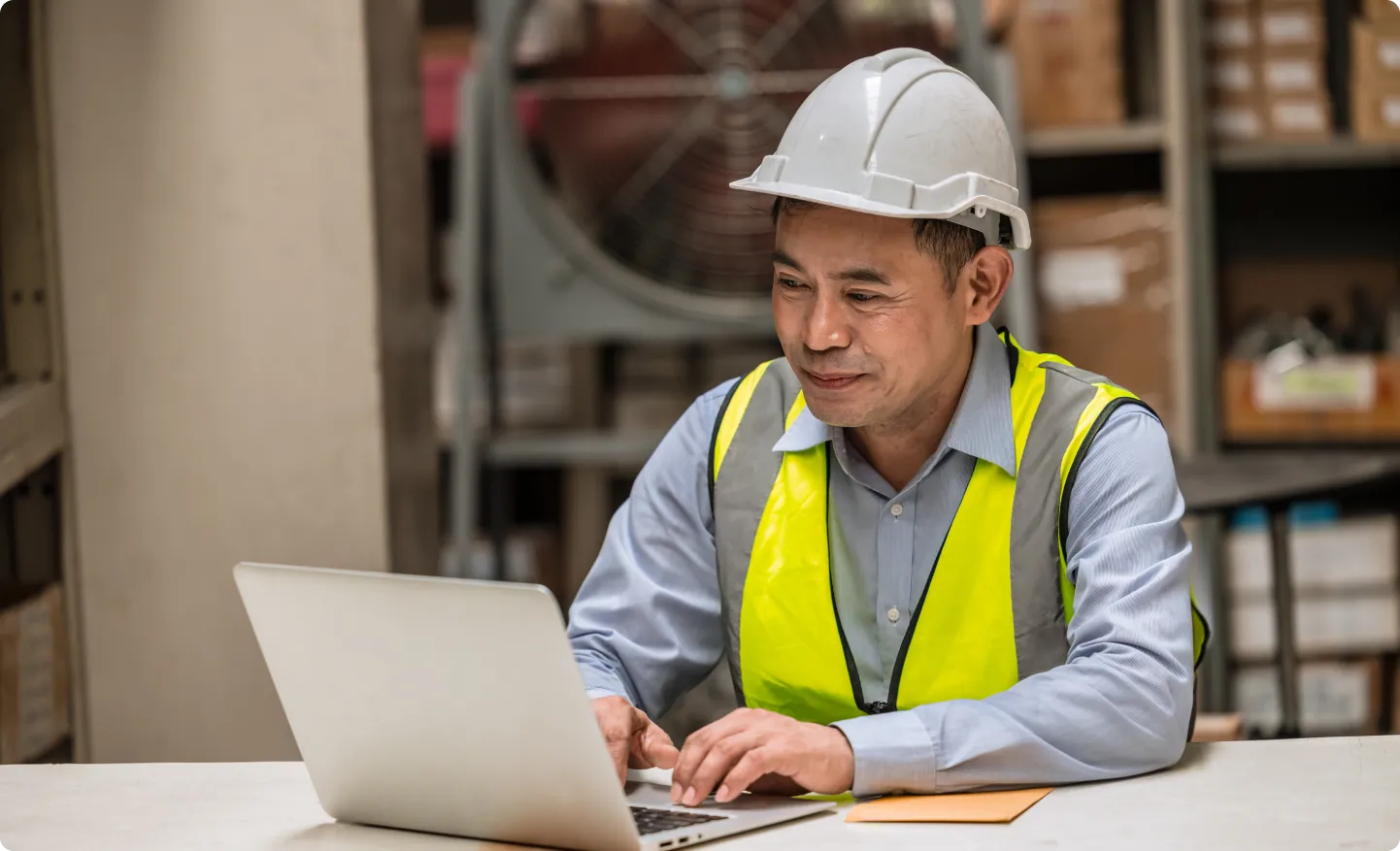
A warehouse management system in logistics functions as a control tower with a 360-degree view of all warehouse activities. It allows managers to monitor, identify, and address bottlenecks and exceptions centrally. Advanced analytics platforms, real-time dashboard visualization tools, and alert systems make for exceptional handling of warehouse operations, both from management and execution standpoints.
A smart WMS is the best warehouse management system; it can combine granular visibility with reporting and analytics to enhance decision-making capabilities, optimize resource allocation, and improve response time.
6. Workforce Management and Performance
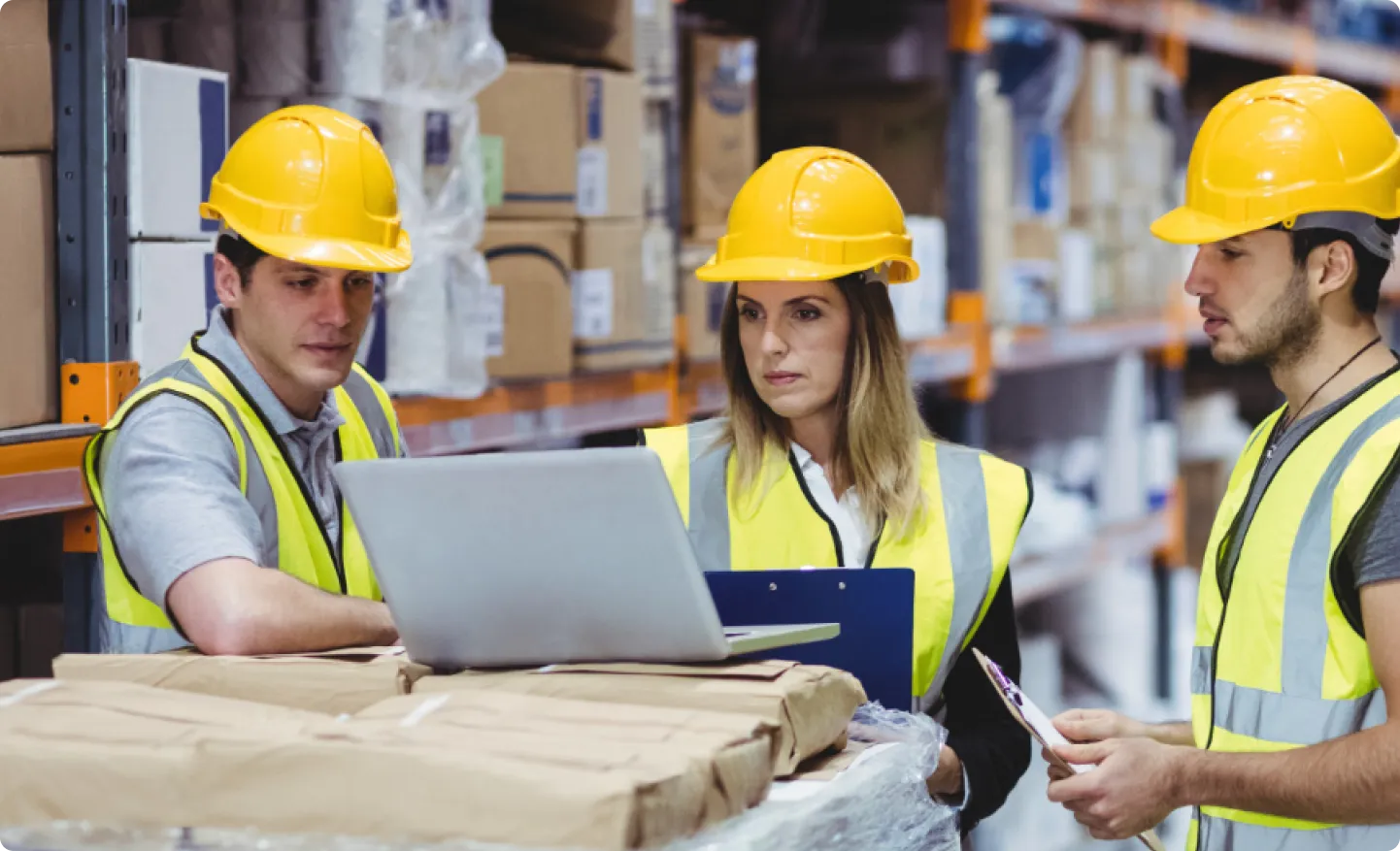
Warehouse management systems can streamline worker onboarding, task allocation, performance tracking, and continuous feedback. Efficient workforce management is key to leaner and more efficient warehouse operations. A centralized control system can allow you to match your warehouse workers with their areas of expertise, dynamically adjust task scheduling, and minimize productivity gaps.
Integration with time-tracking tools, performance analytics software, and task management platforms can help you identify potential areas of improvement. These metrics can also inform labor allotment decisions for optimal workforce management during seasonal peaks.
7. Vendor and Customer Management
Modern warehouse management systems simplify data exchange and communication with suppliers and customers. It provides a centralized hub for vendor interactions and order integration. Built-in connectors and ESBs can simplify integration with the vendor’s systems, leading to faster onboarding and an improved partner experience.
Building strong vendor and customer relationships is essential for ensuring consistent supply and demand fulfillment. A streamlined vendor experience translates to a better customer experience, especially in e-commerce. The WMS can consolidate orders from various sales channels and prioritize based on fulfillment rules and other predefined criteria.
Warehouse management systems provide end consumers with self-service capabilities for a better customer experience. Expedited delivery timelines, accurate deliveries, order tracking, and returns management improve engagement and brand recognition. The WMS provides a centralized hub to identify and resolve customer issues at the earliest, improving relationships with both vendors and customers.
8. Shipping and Freight Management
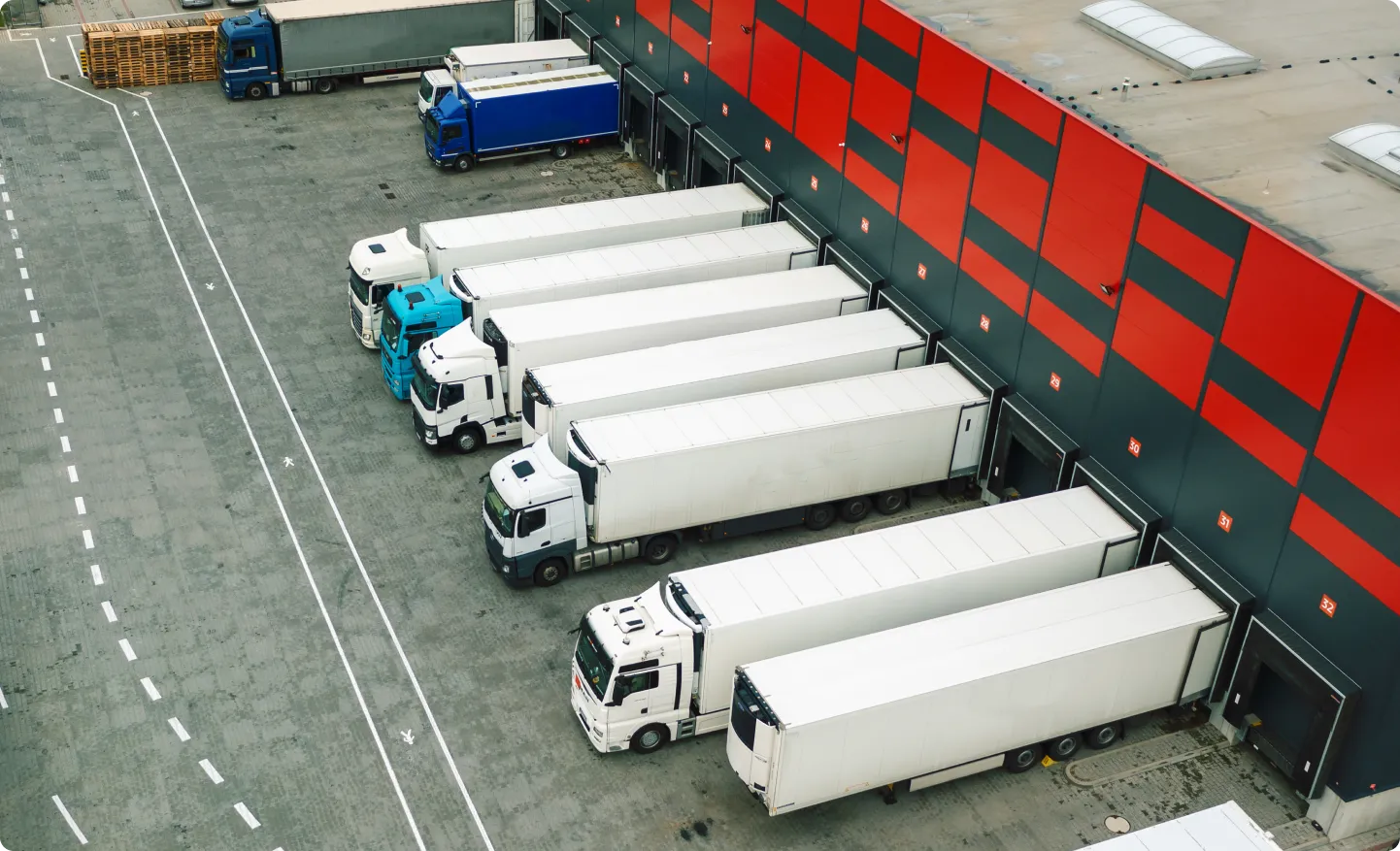
The warehouse management system can integrate with transportation management systems to perform rate shopping and provide comprehensive tracking for the delivery process. Carrier performance analytics means you can negotiate better rates and SLAs for your warehouse. Efficient shipping is crucial for timely deliveries, cost savings, and maintaining carrier relationships. The WMS integration can automate a large chunk of daily tasks, like billing and generation of packing lists and shipment invoices.
A variety of shipping options provides more flexibility for the customers to choose between delivery timelines, schedules, and delivery charges. The WMS can track the exact location of the packages and automatically notify the relevant parties of any unexpected delays.
9. Device and Robotic Control
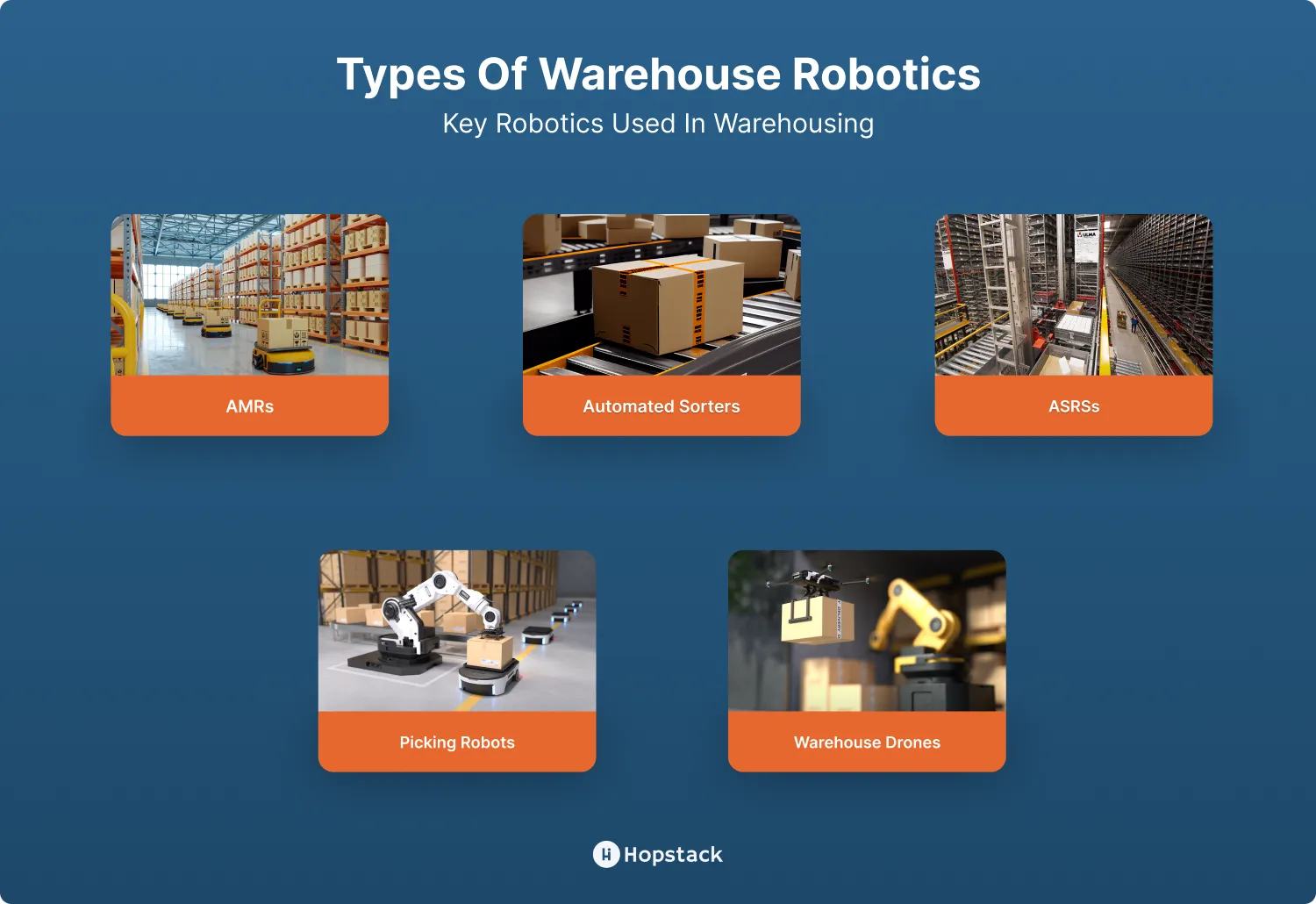
A WMS integration provides a hub to manage and control automated devices and robotics within the warehouse, from autonomous mobile robots (AMRs) to sorter belts. IoT integration for real-time device monitoring can centrally track device health and schedule preventive maintenance.
AMRs work side by side with warehouse workers to minimize errors and exponentially increase productivity. Introducing robotics and automated devices like conveyor belts, AS/RS, and drones can also improve safety and working conditions for the labor force, reducing instances of burnout, fatigue, or workplace accidents.
10. Multi-warehouse Management
A warehouse management system functions as a critical enabler in managing multi-client warehouse operations. This process involves connecting multiple warehouses, intelligently routing orders, optimizing inventory distribution, and ensuring cohesive resource allocation. The best warehouse management systems provide a range of services that include:
Managing multiple warehouses or a warehouse network:
- Centralized Management: A warehouse management system in logistics provides a unified platform to manage inventory, workforce, and equipment across different warehouse locations. This helps in coordinating operations and ensuring uniformity in practices across all the warehouses.
- Streamlined Processes: It automates tasks, minimizes human errors, and streamlines processes such as receiving, put-away, picking, and shipping across all warehouses.
Centralized and localized view depending on user level and use case:
- Centralized View: Administrators and top-level management can get a holistic view of the entire warehouse network. They can monitor inventory levels, workflow, and operational performance of all warehouses from a single dashboard.
- Localized View: Features of warehouse management systems allow local managers and supervisors to get a detailed view of their respective warehouse operations, allowing them to focus on day-to-day tasks, troubleshoot issues, and manage their teams more effectively.
Multi-warehouse operations:
- Order and Consignment Routing: WMS can automatically determine the best warehouse to fulfill a particular order based on factors like proximity to the delivery point, stock availability, and cost of shipping.
- Stock Transfer: In cases where a particular product is out of stock in one warehouse but available in another, a WMS can facilitate inter-warehouse stock transfers. This ensures efficient stock rotation and minimizes the chances of stock-outs.
- Synchronized Inventory Management: It helps in tracking inventory levels across all warehouses in real time, thus aiding in replenishment decisions and reducing holding costs.
Performance analytics:
- Key Metrics Tracking: WMS provides insights into critical performance metrics such as order accuracy, order fulfillment time, inventory turnover rate, and equipment utilization rate, among others.
- Individual Warehouse Performance: Businesses can gauge the performance of each warehouse in terms of productivity, efficiency, and accuracy.
- Overall Network Analysis: By aggregating data from all warehouses, organizations can assess the overall health and efficiency of their warehouse network. This helps in making strategic decisions, forecasting, and long-term planning.
11. 3PL Warehousing
A 3PL WMS can address the various complexities within 3PL warehousing operations through tailor-made integrations and adaptable, modular architectures. The centralized warehouse management solution enables real-time data flow in a multi-client warehousing setup. These out-of-the-box 3PL integrations are especially effective for e-commerce operations, as they unify sales and fulfillment channels with ERP, accounting, TMS, and shipping systems. 3PL billing capabilities improve the timeliness and transparency of your invoices and ensure all billables have been accurately captured.
Various types of warehouse management systems provide multi-client capabilities to ensure organized management of client-specific operations. In addition, performance metrics and reporting tools provide a clear overview of each client's supply chain performance.
The combined results allow 3PL providers to effectively manage diverse client requirements, streamline operations, and deliver exceptional service levels within a unified framework.
12. Dock Scheduling and Yard Management
Various features of warehouse management systems streamline dock scheduling and efficient yard management to ensure smooth inbound and outbound operations. This includes everything from coordinating truck appointments to optimizing resource allocation, ultimately enhancing operational efficiency and overall warehouse productivity.
Dock Scheduling:
- Truck Appointments: WMS enables the scheduling of inbound shipments, ensuring organized truck arrivals and preventing congestion.
- Dock Door Allocation: The system intelligently allocates dock doors based on real-time resource availability and shipment priorities.
- Resource Planning: WMS considers receiving personnel and equipment availability for efficient dock utilization.
- Inbound Visibility: Real-time tracking of inbound shipments allows for accurate scheduling and minimizes delays.
Yard Management:
- Asset Movement Optimization: WMS tracks, organizes, and optimizes the movement of vehicles and assets within the yard, reducing congestion and improving overall flow.
- Cross-Docking Support: For products like fresh groceries, WMS supports cross-docking by immediately placing goods into outgoing shipments without interim storage.
- ASN Integration: WMS seamlessly integrates electronic Advanced Shipping Notices (ASNs) sent by suppliers to match with shipments, ensuring efficient cross-referencing and verification.
- Efficient Receiving: The system streamlines receiving operations by accepting, inspecting, and recording inbound shipments accurately.
13. Analytics and Reporting
A smart WMS can reshape how warehouses harness data for informed decision-making. This data-driven approach lays the groundwork for meaningful insights via automated data collection, seamless integration with analytics, and dynamic visual reporting.
You can run reports at the ERP level for a comprehensive understanding of vital warehouse metrics like on-time shipping, inventory accuracy, distribution costs, and order fill rate. Different types of warehouse management systems can generate visually engaging reports that stakeholders can readily access, enabling strategic adjustments and improved operational outcomes.
Real-time inventory tracking empowers proactive management by revealing stock levels and ensuring prompt restocking or resource optimization. Workflow management tools offer an in-depth look into warehouse activities, identifying inefficiencies and anomalies. Various types of warehouse management system vendors extend their support across national boundaries, featuring multi-location tracking and accommodating diverse languages, tax structures, and currencies.
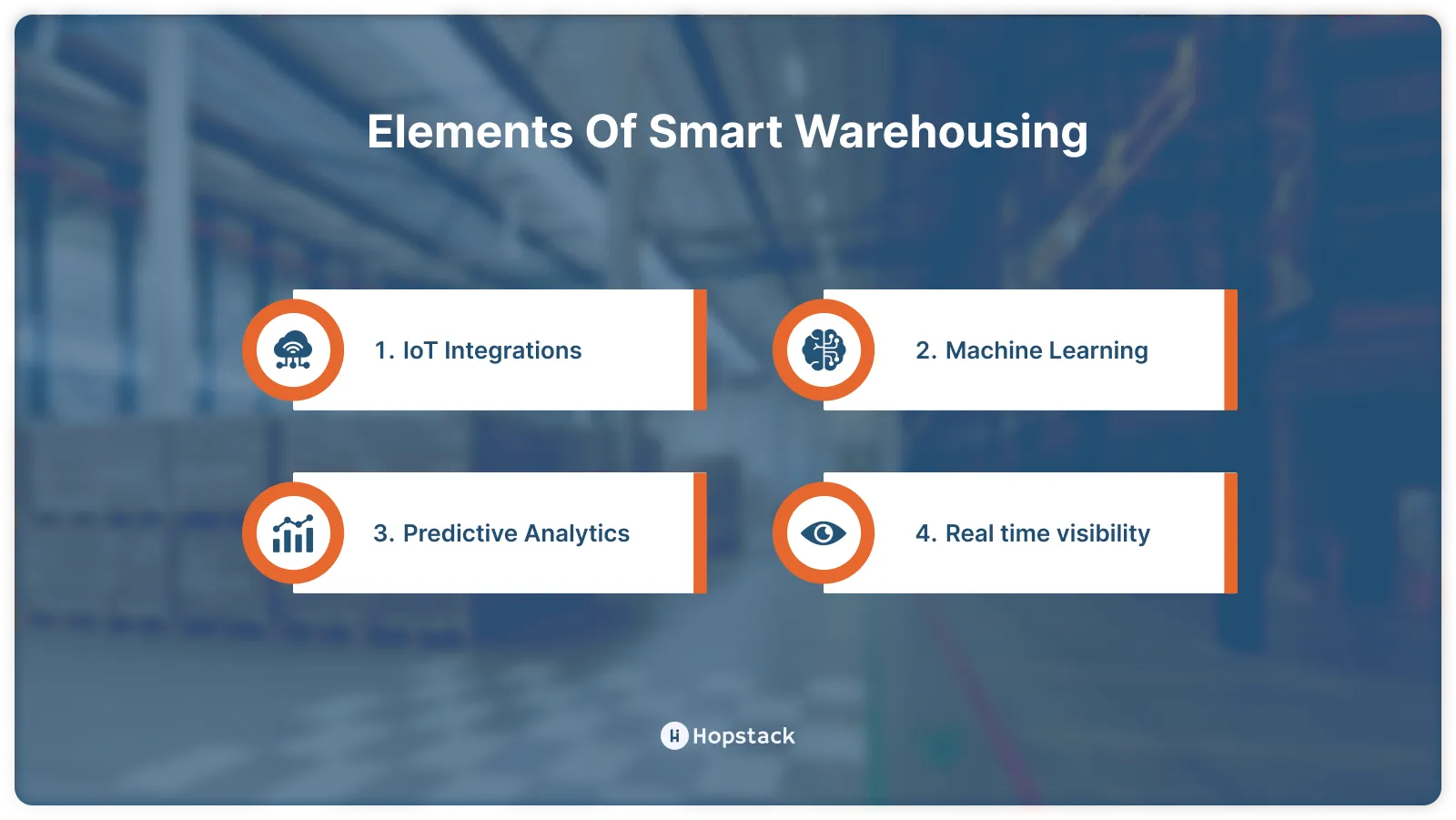
WMS with AI in 2025: The Future of Smart Warehousing
As warehouses become increasingly complex, AI-driven WMS solutions are transforming operations in 2025, making them smarter, faster, and more autonomous. With machine learning, predictive analytics, and robotics integration, AI-powered WMS is redefining efficiency, accuracy, and adaptability in supply chain management.
1. Predictive Inventory & Demand Forecasting
AI-driven WMS can analyze historical sales data, market trends, and real-time demand signals to accurately predict inventory needs. This reduces overstocking, minimizes waste, and ensures warehouses are stocked with the right products at the right time.
2. Automated Picking & Robotics Integration
In 2025, AI-powered robotics are handling a significant portion of warehouse picking, packing, and sorting. Autonomous mobile robots (AMRs) and AI-driven vision systems enhance speed and precision, cutting down fulfillment times and reducing human error.
3. Dynamic Route Optimization for Warehouse Operations
AI optimizes warehouse layout and worker routes in real-time, ensuring pickers take the most efficient paths, minimizing congestion, and increasing throughput. This is especially crucial for high-volume e-commerce warehouses where every second counts.
4. Intelligent Decision-Making with AI Insights
AI-powered analytics provide warehouse managers with real-time insights and prescriptive recommendations to enhance efficiency. Whether it’s reallocating labor based on demand spikes or identifying bottlenecks before they impact operations, AI ensures smarter, data-driven decision-making.
5. AI-Powered Chatbots & Virtual Assistants
AI chatbots integrated into WMS help warehouse staff with voice-activated commands, instant troubleshooting, and real-time inventory lookups—reducing delays and improving productivity.
By 2025, AI-powered WMS isn’t just an upgrade—it’s a necessity. With growing e-commerce demands and labor shortages, warehouses must leverage AI for automation, predictive analytics, and real-time decision-making to stay competitive in the future of supply chain management.
Unveiling WES and WCS
As the warehousing industry evolves, warehouse management systems are becoming increasingly specialized. In today’s hyper-fast commercial landscape warehouse execution systems (WES) and warehouse control systems (WCS) have emerged as the software solutions of choice to address very specific stages within the order fulfillment journey.
WES focuses on orchestrating order fulfillment processes and intelligently directing tasks to optimize efficiency. WCS, on the other hand, focuses on managing material handling equipment, ensuring smooth equipment operation and flow.
While a warehouse management system benefits broad processes like inventory, order management, and resource allocation, WES and WCS enhance the synergy. They complement different types of warehouse management systems by driving specific aspects of warehouse operation, ultimately creating a trifecta of efficiency.
Next Steps
The rapid growth of trade and commerce operations has put supply chain operations through the grinder. Modern warehouses must step up to the challenge by using the right technology or risk being left behind. Today, the features of warehouse management systems represent the best of automation, robotics, and process optimization, making them the best option for managing warehouse operations.
While technology is key for success in the hyper-competitive logistics and supply chain landscape, even the best warehouse management system will never be a guarantee for success unless it’s placed in the context of your business needs. In an ideal warehouse environment, technology seamlessly integrates with the people and processes to streamline warehouse operations at scale. At Hopstack, we specialize in identifying your warehousing needs and helping you realize business objectives with our specialized warehouse management system.