Introduction
Reliable cloud-based WMS is a must-have for retailers to stay ahead of the competition in the global supply chain management sector. It will streamline the fulfillment process and offer comprehensive real-time visibility of inventory movement while utilizing the warehouse space.
However, for an experienced warehouse manager implementation of cloud WMS successfully might sound daunting. To achieve a successful WMS implementation, one needs to focus on a detailed planning process.
This article will provide a thorough cloud WMS implementation checklist and essential tips for a successful rollout. The blog will cover everything starting from preparing the warehouse to customizing the WMS while meeting specific needs.
Tips to Follow for a Successful Cloud WMS Implementation
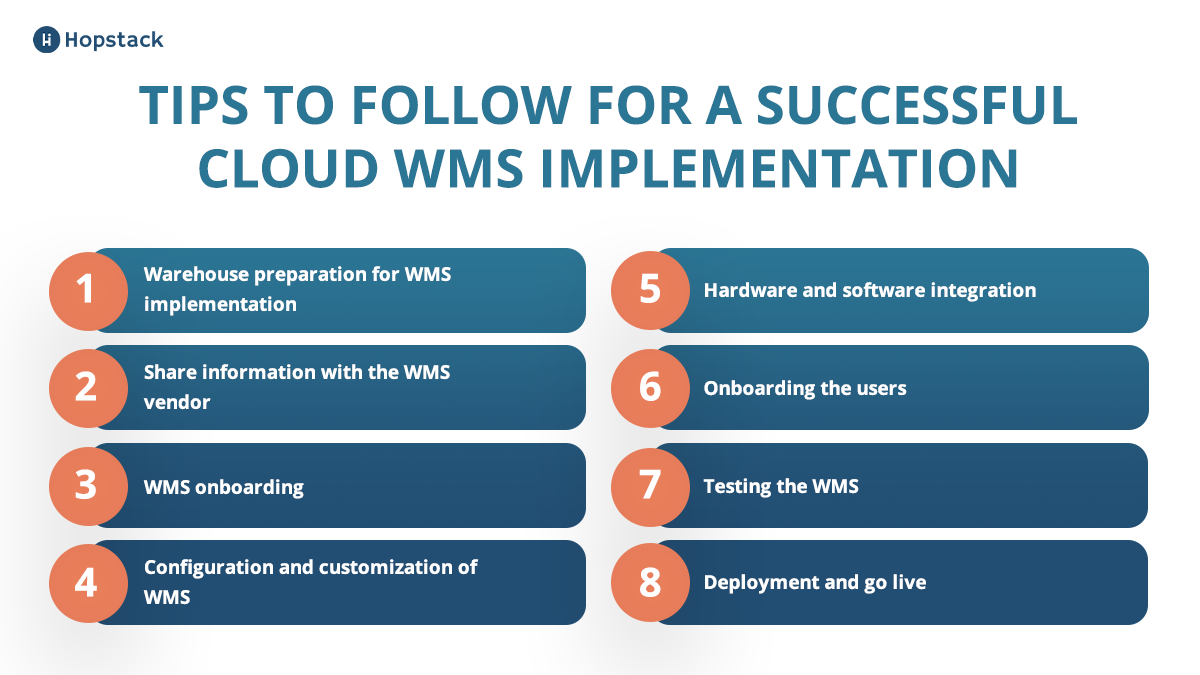
Implementation of Cloud WMS can be a complex and time-consuming process. However, following a few simple WMS implementation steps will ensure a successful deployment of cloud WMS.
1. Warehouse preparation for WMS implementation
The first step for implementing a cloud-based WMS is to make sure whether the warehouse is ready to integrate WMS into its system or not.
Whether a company wants to migrate from its existing system or implement cloud-based WMS for the first time, warehouse preparation is the crucial step. Setting up the warehouse involves:
- A warehouse manager can start preparing the warehouse by defining different warehouse locations (storage areas, paths of travel, works areas, and shelving positions).
- Additionally, he should also properly define multiple warehouse stations like packing, sorting, receiving, and quality check area for a seamless WMS workflow.
- The associate must put barcode labels on pallets, bins, and racks to make them ready for use.
- He should also make sure the availability of hardware devices like scanners, slotters, conveyor belts, forklifts, industrial scales, etc. in the warehouse for seamless movement of inventory.
2. Share information with the WMS vendor
The next step includes sharing critical information with the chosen WMS vendor so that the whole process of warehouse workflow configuration and customization becomes seamless.
The warehouse manager will share the following information with the WMS vendor to accelerate the WMS implementation process.
Below are the basic categories of information list that a WMS vendor should know so that they can include them in the WMS workflow.
- Types of warehouse operations (B2B vs B2C vs both)
- Steps involved in inbound and outbound processes
- Information related to different locations
- Warehouse layout, storage area information
- Hardware device list
- Dimensions of pallets, bins
- Information regarding different stations of the warehouse
- SKU bin mapping
- Information related to inventory
- Different Integrations (System, hardware, carrier, and software)
3. WMS onboarding
The WMS onboarding process starts when a WMS vendor learns about their customer’s business and their requirements for their fulfillment operations
In this stage, the vendor will access the goals, objectives, expectations, technological requirements, warehouse operations process, and other details shared by the customers.
Post assessing every data received from the customer, the WMS vendor will set up a platform instance for the individual customer for WMS onboarding.
4. Configuration and customization of WMS
It is the responsibility of the WMS vendor to configure the Cloud WMS in a way that can cater to unique customer needs. The vendor must focus on the configuration and customization of the WMS along with WMS features as per the workflow and business requirements of the customer.
Below is the list of information that the WMS vendor needs to know before configuring the cloud WMS. These are as follows:
- Information regarding different locations
- Different stations (packing, sorting, receiving, etc.)
- Importing all inventory information (SKUs quantity, product characteristics mapping the SKUs to different bins)
- Various inbound, storage, and outbound workflows
Both the WMS vendor and the customer should work together for configuring the Cloud WMS. The purpose is to cater to the unique inbound and outbound fulfillment needs of the customer.
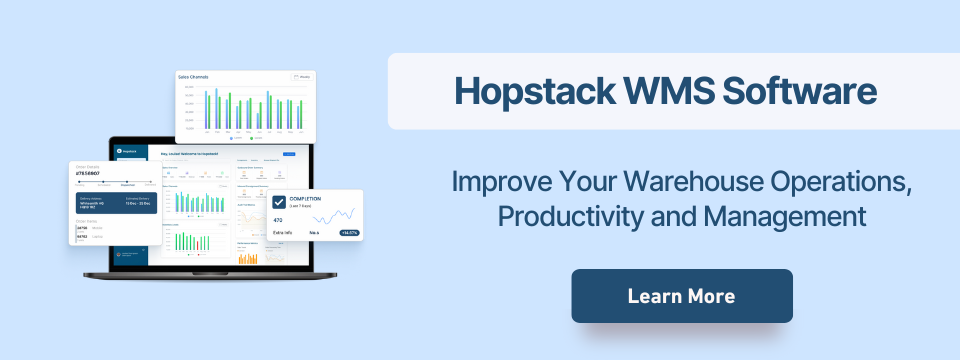
5. Hardware and software integration
For a successful Cloud WMS implementation, the vendor should have a detailed idea about the customer’s account.
There is a multitude of benefits when integrations are added to Cloud WMS. Some are reducing errors, time saving, simplifying fulfillment operations, and consolidating all information in a single database.
Following are the key categories of integrations essential while deploying a WMS.
Hardware Integrations
- Lifting equipment ( forklifts, pallet jacks, hand trucks)
- Conveyors ( belt, vertical, Flexible, Spiral)
- Storage Equipment ( Bins, Totes, Shelves, racks)
- Packing Equipment (Industrial Scales, Packing tables)
- Scanners (RFID, handheld, barcodes)
Software Integrations
- Shipping Software - Integrating shipping software helps in generating shipping manifest automatically, customized workflows, and printing shipping labels.
- E-commerce Platform - Integrating e-commerce platforms help in sourcing order information, syncing SKUs and inventory levels, inventory allocation, and managing catalog and product information.
- E-commerce Marketplaces - e-commerce marketplace integration help in order management, inventory synchronization, catalog and listing management, channel analytics, and reporting, order returns, and reverse logistics management.
- ERP - Integrating ERP solutions help in sourcing orders, syncing inventory information, consignment details, and order details, receiving outbound orders, and creating purchase orders.
- Accounting Software - Accounting software is used for 3PL billing, sales forecast, cash flows, and inventory information.
6. Onboarding the users
Onboarding the users is a crucial Cloud WMS implementation step that will involve all the warehouse associates in the platform.
In this stage, the WMS vendor will onboard all warehouse staff, such as warehouse managers, admins, packers, pickers, sorters, receivers, etc. to the platform.
The staff will be assigned to their designated role in this onboarding process. Their scope of work will be defined properly and translated into multiple permissions. The platform will help to configure and customize the permissions.
For instance, if an associate is allowed to pack items from a certain packing station, then these permissions will be configured and customized in the platform.
WMS should provide a lot of flexibility around defining the roles for each warehouse associate.
7. Testing the WMS
Once the Cloud warehouse management system has been configured and customized as per the customer's requirements, now it's time to perform thorough testing before deploying.
It includes testing all the hardware, software, user profiles, workflows, etc. in a virtual environment.
The WMS vendor will be simulating the entire process to ensure that everything is working properly as intended.
They will be simulating the inbound process, storage process, and outbound processes. A dry run on cycle counts can also be done in this testing phase.
They might also simulate the process of getting orders from different sources and the ways of fulfilling orders.
8. Deployment and go live
Once the Cloud warehouse management system has been thoroughly tested and is functioning as intended, now it’s time to go live.
It includes making sure that every warehouse associate has received the necessary training and is accustomed to the new system and procedures.
Additionally, it is essential to test the system in a real-world environment as this will reveal any potential problems before they occur.
Once every issue has been addressed and everything has been approved by all warehouse employees, then the Cloud WMS can be deployed.
If all the processes, integrations, and configurations seem to be working accurately, then at this project launch stage, the company can start using the WMS for its actual warehousing and fulfillment operations.
The Bottom Line
A business may ensure that the sales channels, inventory reports, and financials are consistently updated with each shipment, delivery, and warehouse transfer by implementing a cloud-based warehouse management system.
The success of the WMS implementation will be ensured by careful planning before, during, and after implementation.
The WMS vendor and the customer must collaborate as a single team to ensure a successful Cloud WMS implementation.
WMS Implementation Checklist For Your Warehouse
Don't miss out on our downloadable WMS implementation checklist, meticulously crafted to ensure a seamless transition. From assessing your current processes to post-implementation optimization, this WMS implementation checklist empowers you every step of the way. Download it now to unlock the full potential of your warehouse management system and maximize efficiency like never before!
Download WMS Implementation Checklist by Hopstack
Seamless WMS Implementation with Hopstack
Hopstack’s cloud-based warehousing and fulfillment platform provides highly customizable and flexible setup options that make the implementation seamless. The platform can be tailored to fit customers’ specific needs, making it easy to integrate into existing operations.
With Hopstack’s rule engine and workflow designer, warehouse managers can create different warehouse management workflows for various inbound, storage, and outbound processes and set up rules for exception handling and fostering specialization.
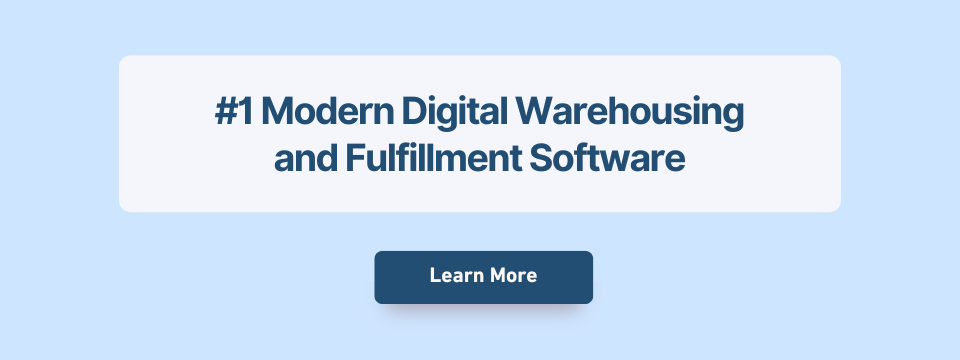
The platform also comes with 60+ plug-and-play software and hardware integrations helping warehouses connect all their devices and sync information such as orders, inventory, shipping data, tenant data, product details, and more in a matter of minutes.
Speak with Hopstack’s product specialist to learn more about how the platform’s capabilities can help uplevel your fulfillment operations.