What is Warehouse Automation?
Warehouse automation refers to the use of technology to perform tasks traditionally done by human workers, such as sorting, picking, and packing goods. These systems integrate robotics, software, and equipment like conveyors, automated guided vehicles (AGVs), and automated storage and retrieval systems (ASRS) to streamline operations.
In today's fast-paced supply chain environment, where consumer expectations for quick, accurate deliveries are higher than ever, automation is no longer a luxury—it's a necessity. It helps warehouses meet the increasing demands for faster turnaround times, reduced errors, and higher throughput, all while managing rising labor costs.
According to a report by McKinsey & Company, warehouse automation has the potential to increase productivity by 30% or more, helping companies achieve significant cost savings and improved operational efficiency.
This guide aims to provide a comprehensive yet digestible overview of warehouse automation systems, helping you understand how they work, the benefits they bring, and how to implement them in your operations. Whether you're a warehouse manager considering automation for the first time or an industry expert seeking to expand your knowledge, this guide will offer valuable insights to support your decision-making.
From understanding the different types of automation systems to selecting the right solution for your needs, we’ll cover everything you need to know to stay ahead in the competitive world of modern warehousing.
- What is an Automated Warehouse?
Automated Warehouse is same as warehouse automation, in a nutshell, it is the automation of the movement of inventory from the point where it is received into the warehouse to the point where the inventory is shipped out. Every step of the process is directed to reduce human intervention and maximize efficiency. When a business chooses to automate its warehouse, they gain control and visibility of the warehouse operations.
As a result, many companies and warehouse owners looking to improve their efficiency and optimize productivity are turning towards Automated Warehouse to achieve their business needs. As of 2024, research showed that more than 40% of warehouses mainly in United States moved towards technology and automation.
Key Benefits of Warehouse Automation
Improved Efficiency and Productivity
One of the most significant advantages of warehouse automation is its ability to boost operational efficiency. Automated systems, such as conveyor belts, robotic arms, and automated guided vehicles (AGVs), work at a faster pace than human workers, and they can operate 24/7 without fatigue.
This increased speed leads to quicker order fulfillment, which is essential for meeting customer expectations, especially in industries like e-commerce where rapid delivery times are critical.
Example: With automated sorting systems, warehouses can process thousands of packages per hour, dramatically reducing the time needed to prepare orders for shipment.
Reduction in Human Errors
Even the most skilled workers are prone to mistakes, especially in high-volume environments where repetitive tasks and time pressures can lead to errors. Automated systems help minimize these risks by following predetermined processes without deviation. This reduction in errors is especially crucial in industries with high accuracy demands, such as pharmaceuticals, consumer electronics, and medical devices, where mistakes could result in costly recalls or customer dissatisfaction.
Example: In automated picking systems, robots can precisely identify and retrieve the correct items, reducing the risk of incorrect shipments.
Cost Savings in the Long Run
Although the upfront cost of automation can be significant, the long-term savings often outweigh the initial investment. Automated systems reduce the need for manual labor, lower the likelihood of costly errors, and streamline operations to minimize wasted time and resources.
Over time, these factors lead to a substantial reduction in operational costs, particularly labor expenses. In addition, automation allows warehouses to optimize storage space and improve inventory management, which can further contribute to cost savings.
Example: In a study by DHL, companies using automated storage systems reported a 25-30% reduction in operating costs over a five-year period due to improved inventory management and faster processing times.
Automated Warehouse Challenges and Considerations
Initial Investment and ROI Timeline
The primary challenge with implementing warehouse automation is the substantial upfront investment required. Systems like automated conveyors, robots, and ASRS can be costly to purchase, install, and customize. However, the return on investment (ROI) from automation often takes several years to materialize, depending on the scale of the operation and the level of automation being implemented. For companies with limited capital or those with a smaller scale of operations, the initial cost can be a significant barrier.
Consideration: A clear ROI analysis is essential before committing to automation. Businesses should calculate potential savings in labor costs, productivity gains, and inventory improvements to estimate when the system will start paying for itself.
Integration with Existing Systems
Another challenge when adopting warehouse automation is the integration of new systems with existing infrastructure. Many warehouses rely on established Warehouse Management Systems (WMS) and Inventory Management Systems (IMS) to track inventory and manage workflows. Introducing automation requires seamless integration between the new automated systems and these legacy software solutions. This can be complex, especially for older systems that may not have been designed to support modern automation technologies.
Consideration: It’s crucial to choose automation systems that are compatible with existing software and processes. Adequate planning and collaboration with automation vendors are key to ensuring a smooth integration.
Maintenance and Scalability
While automation systems are designed to reduce reliance on manual labor, they still require regular maintenance to operate effectively. Over time, components can wear out, and systems may experience downtime that could affect overall efficiency. Additionally, as your business grows, your automation system must be able to scale to accommodate higher volumes or new operational needs.
Consideration: When selecting an automation solution, it's important to evaluate the vendor's support services and maintenance offerings. Long-term scalability should also be a priority, ensuring that the system can adapt to future growth and changes in the business environment.
Types of Warehouse Automation Systems
Warehouse automation systems can be broadly categorized into physical automation systems (such as robots, conveyors, and ASRS) and digital systems (like WMS, WCS, and RFID). These technologies work together to streamline operations, enhance efficiency, and ensure accurate inventory management. Below is an overview of both physical and digital systems used in modern warehousing.
Automated Storage and Retrieval Systems (ASRS)
Automated Storage and Retrieval Systems (ASRS) are highly sophisticated systems designed to store and retrieve products from specific locations in the warehouse. These systems utilize automated machines like cranes or shuttles, controlled by a Warehouse Management System (WMS), to move inventory quickly and efficiently.
ASRS are ideal for high-density storage, utilizing vertical space to maximize storage capacity. They dramatically improve retrieval times by ensuring that items are stored in the most accessible locations, reducing the time spent locating products. By automating this process, warehouses can achieve faster order fulfillment, reduce human errors, and optimize space usage, allowing for more efficient use of the warehouse floor.
Conveyor Systems
Conveyor systems are essential tools in warehouse automation, designed to transport goods from one area to another with minimal human interaction. There are several types of conveyor systems, each suited to specific tasks. Roller conveyors, which rely on gravity, are often used for lighter items, while belt conveyors handle heavier goods over longer distances. Pneumatic conveyors use air pressure to move products and are particularly useful in environments where gentle handling of goods is needed.
These systems accelerate product flow, moving goods across the warehouse at a constant, efficient pace. By automating the transport process, conveyors reduce the need for manual labor, allowing workers to focus on more complex tasks. Conveyor systems also minimize delays and bottlenecks by ensuring that products are consistently moved from one section of the warehouse to the next without interruption.
Robotic Systems
Robotic systems in warehouses include Automated Guided Vehicles (AGVs) and picking robots, both of which play pivotal roles in improving warehouse operations. AGVs are mobile robots that autonomously navigate the warehouse floor to transport materials between various locations. These vehicles follow predefined paths, avoiding obstacles and ensuring safe transport of goods.
Picking robots, equipped with advanced sensors and grippers, are capable of autonomously selecting and retrieving items from shelves. These robots increase picking accuracy and speed, enabling warehouses to fulfill orders faster. By reducing reliance on human labor for repetitive tasks, robotic systems enhance overall operational efficiency and can handle more complex workflows in high-demand environments.
Sortation Systems
Automated sortation systems are designed to quickly and accurately sort products based on pre-defined criteria such as order number, destination, or shipping lane. These systems utilize conveyors, barcode readers, and RFID technology to direct products to specific locations within the warehouse.
Sortation systems are particularly beneficial in high-volume order processing environments, such as e-commerce fulfillment centers. By automating the sorting process, warehouses can manage larger volumes of orders more effectively, ensuring that products are quickly directed to the appropriate shipping lanes. This leads to faster and more accurate order fulfillment, which is critical in meeting customer expectations for timely deliveries.
Voice Picking Systems
Voice-directed picking systems utilize speech recognition technology to guide warehouse workers in real-time during the picking process. Workers wear headsets that communicate with the WMS, providing verbal instructions for locating and picking items.
The main advantage of voice picking is its ability to improve efficiency and accuracy. Since workers don’t need to rely on paper-based systems or handheld devices, they can move through the warehouse hands-free, reducing the time spent on manual checks. Real-time voice instructions ensure that workers are always on track, minimizing picking errors and ensuring that the right items are selected for the right orders.
Goods To Person (GTP)
Goods To Person is one of the most popular techniques to transport inventory within the warehouse by implementing equipment like conveyors, carousels, and vertical lift systems. The concept of Goods To Person is straightforward. It enables inventory to flow through various stages without much human interference. With the proper use of Goods To Person, the picking speed of a warehouse can increase more than double.
Digital Automation Systems
In addition to physical automation systems, digital automation plays a crucial role in optimizing warehouse operations. These systems focus on managing and controlling workflows, tracking inventory, and enabling seamless coordination between automated processes.
Warehouse Management Systems (WMS)
A Warehouse Management System (WMS) is the backbone of digital automation in a warehouse. It is responsible for controlling inventory, managing order fulfillment, and coordinating the activities of physical automation systems. The WMS integrates with all other systems in the warehouse, ensuring that products are stored, picked, and shipped with maximum efficiency.
By automating inventory tracking and order management, WMS systems eliminate manual processes that can lead to human error and inefficiencies. They provide real-time visibility into warehouse operations, allowing managers to make data-driven decisions, optimize workflows, and quickly address issues as they arise.
Warehouse Control Systems (WCS)
Warehouse Control Systems (WCS) work alongside the WMS to manage real-time activities related to automated material handling systems such as conveyors, sorters, and automated cranes. The WCS acts as the coordinator, ensuring that these systems work together smoothly and efficiently.
While the WMS handles higher-level management tasks, the WCS focuses on the execution of real-time activities. It ensures that items are directed to the right place at the right time, reducing delays and improving the overall flow of goods. The WCS is essential for maximizing the performance of automated systems and ensuring that they are operating at their full potential.
Inventory Management Systems (IMS) and RFID
Inventory Management Systems (IMS) are critical for keeping track of stock levels and managing the flow of goods within the warehouse. When combined with RFID technology, which uses radio waves to track the movement of goods, IMS provide real-time visibility into inventory. RFID tags are placed on items, and readers installed throughout the warehouse automatically track and record their movements.
The use of RFID and IMS enhances the accuracy of inventory management by eliminating manual scanning and reducing human error. Real-time tracking allows warehouse managers to quickly assess stock levels, identify discrepancies, and ensure that inventory is always accurately recorded.
Artificial Intelligence (AI) and Machine Learning (ML)
AI and Machine Learning algorithms are increasingly used in warehouse automation to optimize decision-making processes. These technologies analyze vast amounts of data to identify patterns and predict future trends. For example, AI can help forecast demand, optimize stock levels, and improve inventory allocation, ensuring that warehouses are prepared for fluctuations in demand.
Additionally, AI and ML can be used to optimize routes for automated picking and sorting systems, reducing the time it takes for workers and robots to locate and process items. Over time, these systems learn from past data, continually improving their performance and adapting to changes in the warehouse environment.
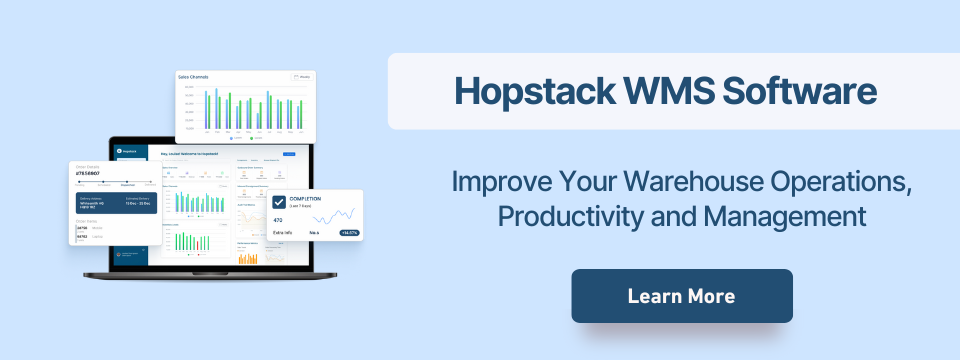
When Should You Consider Warehouse Automation?
The Pressing Need for Automation in Warehouse Settings
In a world dominated by instant gratification, businesses face mounting pressures to deliver goods faster, more accurately, and with a greater degree of transparency.
With increasing competition, tight margins, and the unpredictable nature of global supply chains, relying on traditional manual warehousing methods can quickly become a bottleneck.
For many companies, their warehouses become a reflection of their commitment to customer satisfaction. Late shipments, mismanaged inventories, and the inability to scale operations can tarnish a brand's reputation in no time.
Thus, automation stands as a beacon of hope for those looking to overcome these challenges. By automating tasks, businesses can ensure consistency, speed up processes, and reduce errors – all translating to happier customers and more efficient operations.
Before we dive deeper into the how-tos of Warehouse Automation, it is best to start with this question. Suppose you or your warehouse team is often caught up with handling warehousing tasks manually and spending excessive time analyzing data using spreadsheets and paperwork, you could be paying exorbitant amounts of money on labor costs. It is believed that labor costs constitute almost 65% of the overall warehouse operational budget. In any case, it is time you consider using a modern Automated Warehouse system like a Warehouse Management System.
There are a few other signs you should look out for when you want to know if it is time to Automate your Warehouse:
- Is Your Order Fulfillment Lagging? Are you finding it challenging to fulfill orders on time?
- Is Your Inventory Data Unreliable? Are you struggling with inaccuracies in tracking inventory data and order information?
- Are Wrong Picks Elevating Order Errors? Is incorrect picking causing your order error rate to surge?
- Is Task Allocation a Challenge? Do you find it difficult to assign tasks to your warehouse staff effectively?
- Are Your Cycle Counts Off? Do you notice inaccuracies in inventory cycle counts?
- Is Overstaffing Straining Your Budget? Have you overstaffed your warehouse to cope with the incoming orders?
- Are Labor Costs Spiraling? Are you hiring more staff just to handle peak seasons?
- Is Space Utilization a Concern? Are you struggling to optimize your warehouse's spatial configuration?
- Are Packaging Failures Leading to Returns? Are your packaging methods causing orders to be returned due to damages?
- Are Repetitive Shipments Spiking Costs? Have overhead costs surged because of repetitive order shipments?
- Is Customer Engagement a Hurdle? Do you find it daunting to engage with your customers and ensure their satisfaction?
- Do You Face Scalability Issues? Can your current processes handle an increase in order volume?
The most important thing to keep in mind is that the challenges mentioned above are pretty standard, and it is very natural to face them if you are an e-commerce business owner. But once you can successfully identify them, you can take appropriate steps like automating your warehouse operations to keep them at bay.
If you need more help identifying and understanding these challenges, we recommend getting in touch with our industry experts.
How Does an Automated Warehouse Work?
When you automate your warehouse, advanced software tools like Warehouse Management System and hardware technologies like Robotics and sensors work in synchronization to automate almost every step in the warehouse process. If you already have an existing software tool, you can easily integrate it with the automation system and enhance your workflow.
Automating Warehouses can ensure you are always ready to meet the market's rising demands and provide your customers with the best service possible. In any business, data is absolutely critical. The same goes with warehousing as well. With the automation system capturing real-time data, you can easily analyze data most efficiently.
How to Implement an Automated Warehouse Model?
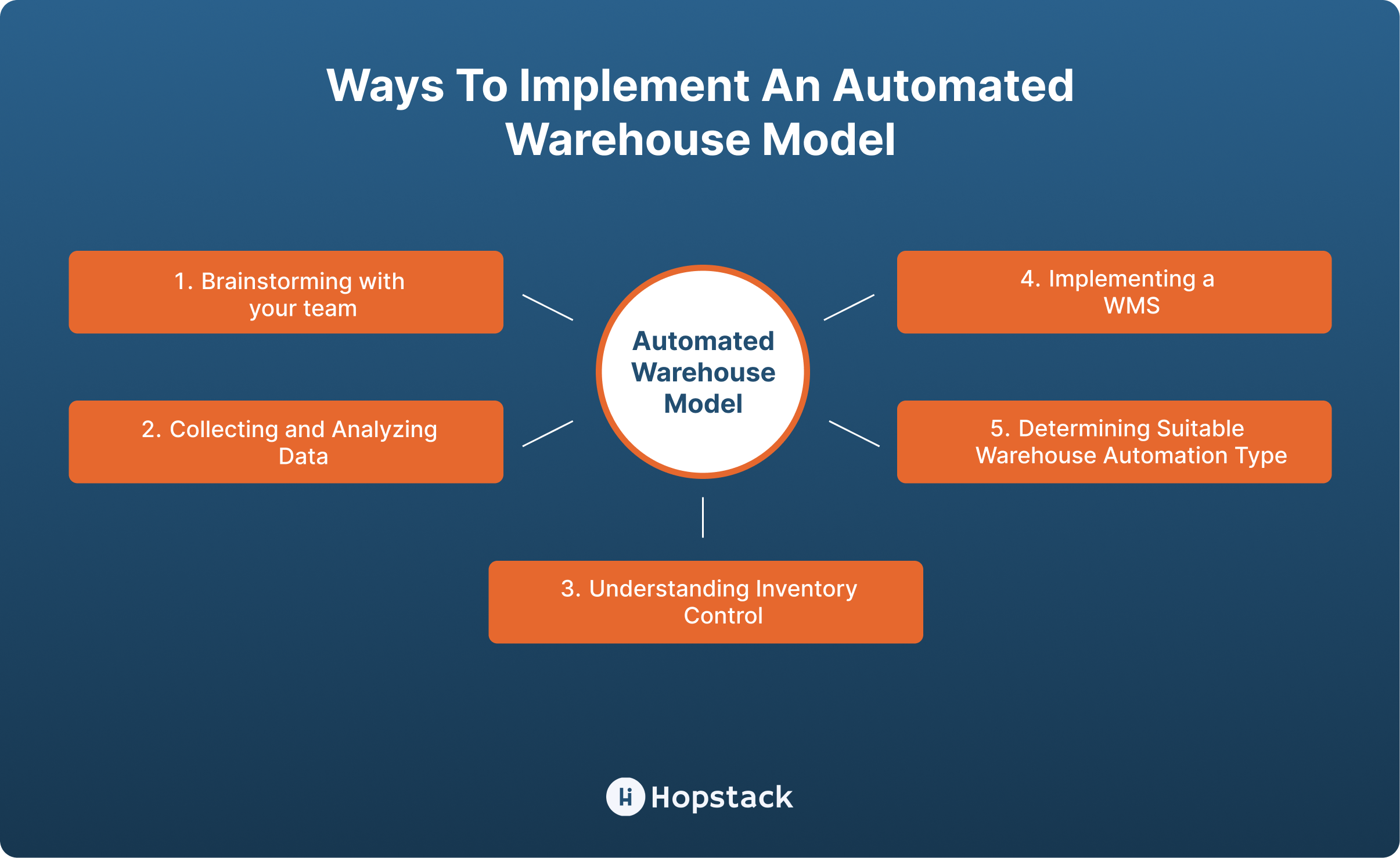
Like any business model, even the Automated Warehouse Model requires a solid project plan. When developing your Automated Warehouse Model plan, there is no one plan for all ideologies. You will have to understand where your business stands and develop a plan accordingly. But, here are some things you should not miss when planning to Implement an advanced Automated Warehouse Model.
Brainstorm with Your Team
Regardless of the size of your business, you must involve your team and all the stakeholders. Doing so will help you gather insights into what parts of your warehouse need special attention. That is not all; it is also essential to include people with the necessary expertise who can help you ideate in the right direction. It is wise to have third-party industry experts who can help you understand your warehouse needs and recommend suitable business tools to make the Warehouse Automation process smoother.
When you brainstorm with your team, defining your business goals and objectives is vital. If you do not know what you want to achieve, it can get challenging to track your progress after you have automated your warehouse.
Collect and Analyze Data
Data is a valuable resource in any business. Effective Automation of your Warehouse depends on the data you have already gathered from your operations and workflow. It is vital to analyze this data and derive critical takeaways to know precisely where your business stands. Once you get a clearer understanding of what needs your attention, you can strategically plan the automation process for your warehouse by considering various factors like infrastructure and budget.
Understanding Inventory Control
One of the main functions of a warehouse is Inventory Control and Management. Before you begin the Automated Warehouse systems process, you need to understand the operation flow of your inventory management. Data points like inventory cycle count, inventory loss, inventory damages, and inventory movement are essential to systematically planning a model that can amplify your throughput. At this point, analyzing your ecommerce order fulfillment Key Performace Indicators or KPIs can be beneficial as they give you insights into some of the most critical metrics of your business.
In all of the above cases, implementing a powerful Warehouse Management System that includes a top-of-the-line Inventory Management System can do wonders for your business and warehousing model.
Implementing a Warehouse Management System or WMS
A modern Warehousing Management System includes a feature set specially designed to enhance your warehouse workflow. Every step can be systematically carried out from the inbound stage to ensure efficiency and reduced costs. When you implement a feature-rich Warehouse Management System, you gain the ability to automate your warehouse to a whole new level.
In case you already have an existing enterprise software, a modern Warehouse Management System should be able to integrate with your system effortlessly, giving you maximum control and visibility all in one place.
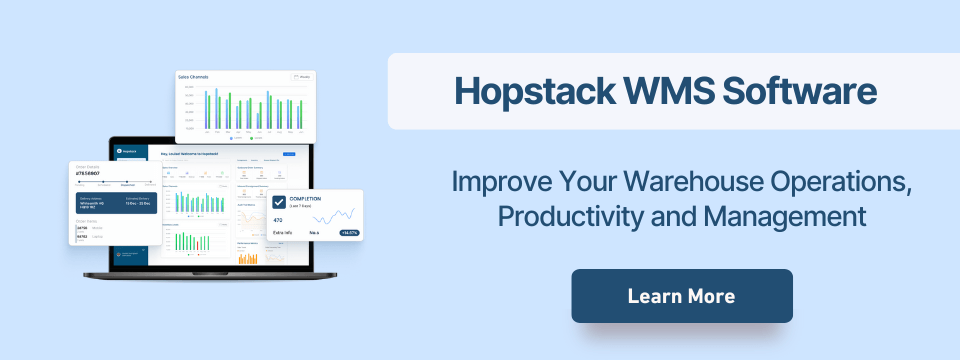
Determining Suitable Warehouse Automation Type
Once you have gathered enough information and defined your goals, the next step is to determine the most suitable automated warehouse systems type. You will have to understand if your objective is to reduce labor costs or expand your warehouse operations. Suppose you want to automate the manual data entry process or implement effective task assignments; you will have to determine what type of Automated warehouse system is optimal for your business. In some instances, choosing a combination of automated warehouse management systems can also be beneficial.
Best Practices for Warehouse Automation System
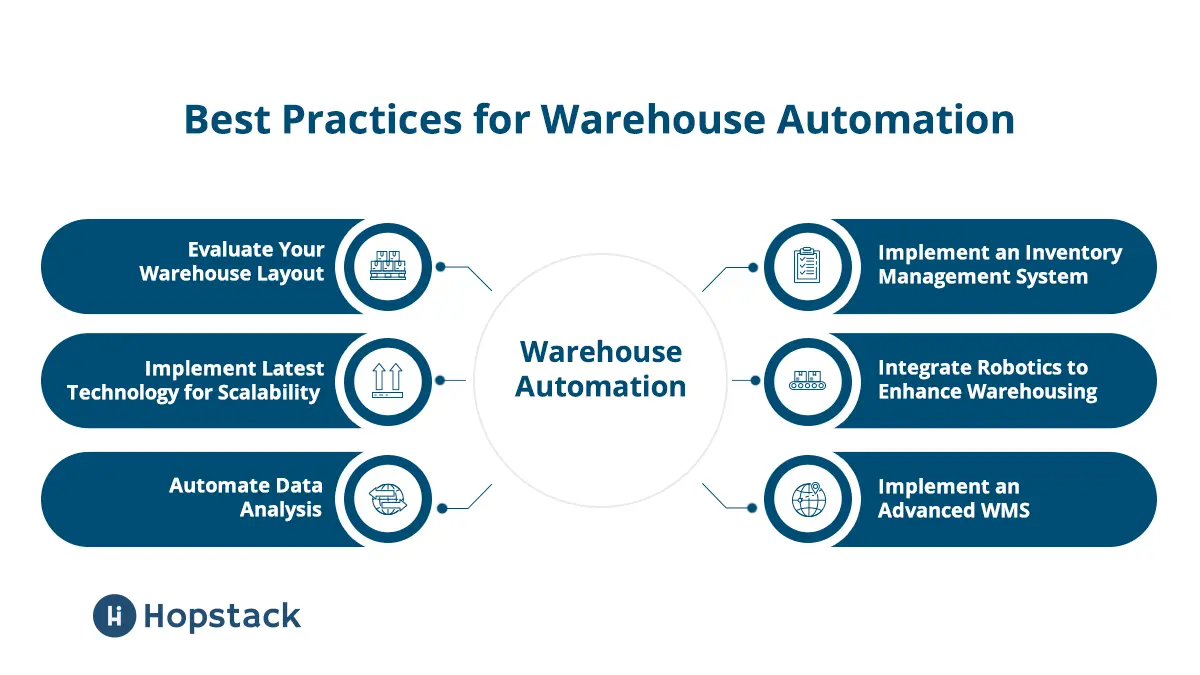
At this point in history, it is evident that warehouses are an essential component of the supply chain. Be it any Conglomerate or a Small and Medium-sized e-commerce business, having a well-planned warehouse will help drive commerce forward. Warehouse Automation is no doubt a step that could benefit you massively. Here are a few best practices you should follow to make the most of an automatic warehouse:
Evaluate Your Warehouse Layout
Automating your warehouse can easily help you streamline your workflow and improve productivity. But, if there's a flaw in your Warehouse Layout, you will not be able to make the most of your automated warehouse system. Every Warehouse is unique and will require you to intervene differently. You will have to systematically assess the space and understand your warehouse's throughput to know where the gap is in processing. Once you know what is going on, you can then make the necessary changes to your Warehouse Layout that is logistically optimal for your business needs.
We recommend you consider different layout configurations when evaluating your Warehouse Layout. Go through our article on optimizing your Warehouse Layout to know more.
Implement Latest Technology for Scalability
Regardless of where you invest your resources, it should always focus on scaling your business to the next level. And modern technology can be one such asset. Technology has given rise to many innovative solutions that you can implement to transform warehouse operations. In particular, the Internet of Things (IoT) is one of them. With the ability to communicate virtually with one another, IoT devices can be a great addition to the Warehouse Automation process that can streamline and help you scale your warehouse for improved efficiency.
Take a look at our article to learn more about how the IoT transforms warehouse operations.
Automate Data Analysis
Analyzing Data in any business is critical. If you run an e-commerce business, you already know the importance of tracking specific metrics. Key Performance Indicators or KPIs are sure shot metrics that provide significant insights into how your e-commerce business is performing and where you should shift your focus to make the most of your automatic warehouse process. This is only possible when you have employed a system that captures real-time data actively. That is why it is essential to implement a Warehousing Software that keeps track of these metrics to give you recommendations that could help you increase efficiency.
Implement an Inventory Management System
The fundamental function of a warehouse is to store inventory. As inventory in any business is one of the essential assets, managing it as effectively as possible is critical. When you implement an Inventory Management System, you automatically gain control and visibility of how your inventory is stored in the warehouse. One of the most vital tasks of inventory management is performing cycle counts. When you have automated your warehouse, you can systematically use RFID barcode scanners to perform cycle counts.
An article to learn more about Inventory Optimization.
Integrate Robotics to Enhance Warehousing
Implementing Hi-tech Robots can do wonders for the Automated Warehouse system process. It is no surprise that the Robotics Industry is skyrocketing. It is estimated that the Robotics industry will grow by 26% annually to value at over $190 billion by 2025. Almost every other sector employs Robotics in their production line or their warehouses to help them achieve the efficiency and productivity needed to beat their competition. If you want to make the most of your Warehouse Automation, investing in modern Robotics can be game-changing.
We recommend you read our take on how Robotics can enhance your warehousing operations
Implement an Advanced Warehouse Management System
If you've made it here, you probably might have guessed already that automatic warehouse is only as good as your Warehouse Management System. As of 2020, over 72% of warehouse managers and owners believe the Warehouse Management System is the preferred software for streamlining warehouse operations. That is why it is critical to implement an advanced Warehouse Management System that can help you streamline your warehouse operations.
A modern automated Warehouse Management System should have the ability to manage inventory effectively and analyze real-time data while giving you the power to customize based on your business needs efficiently. An advanced Warehouse Management System gives you the ability to integrate the latest technology, such as the Internet of Things and Robotics, with minimal effort. It should give you complete control and visibility of all your warehouse operations, all in one place.
More Benefits of Warehouse Automation
Efficiency and Speed: Faster Operations, Reduced Manual Errors
The primary allure of warehouse automation lies in its promise of increased efficiency. With machines taking on repetitive tasks, processes become swifter, and the margin for manual error dwindles.
Whether it's the automated sorting of products or the use of drones for inventory checks, each facet of automation contributes to speeding up the warehouse's daily operations. A fully integrated automated warehouse system can process orders in a fraction of the time it would take a manually operated one. Many warehouses in the US have already implemented these automation technologies.
Cost Reduction: Labor, Waste, and Other Overheads
One of the biggest expenses in warehousing is labor costs. By automating repetitive and time-consuming tasks, businesses can redirect their workforce towards more value-added roles, thereby optimizing labor expenses.
Additionally, automation reduces waste stemming from errors, which can lead to unnecessary costs. Whether it's a wrong shipment or over-ordering a product, these mistakes add up. Automated warehousing systems, with their precision, can significantly diminish such instances, ensuring a more cost-effective operation.
Improved Inventory Management: Real-time Tracking and Optimized Storage
Inventory management is the backbone of any warehousing operation. An automated warehouse system ensures real-time tracking of products, from the moment they enter the warehouse to the time they're dispatched.
With tools like IoT sensors and automated warehousing software, businesses can get accurate stock levels, anticipate product demand, and reduce the risk of overstocking or stockouts. Furthermore, advanced systems can suggest optimal storage solutions, ensuring that the warehouse space is used to its maximum potential.
Enhanced Safety: Fewer Accidents and Safer Working Conditions
Warehouses can be fraught with hazards. Manual lifting, transportation, and storage can sometimes lead to accidents. Automation, however, offers a safer alternative.
Robots and automated vehicles are programmed to operate with precision, reducing the risk of accidents due to human error. They can also handle tasks in environments not suitable for humans, such as those involving hazardous materials or extreme temperatures.
Scalability: Future-proofing Warehouse Operations
Perhaps one of the most compelling advantages of warehouse automation is its scalability. As businesses grow and order volumes increase, there's a pressing need for processes that can scale accordingly.
Manual operations have a threshold, beyond which efficiency starts to wane. Automated systems, on the other hand, can be easily scaled up or down based on demand, ensuring that the warehouse remains agile and responsive to market dynamics.
Sustainability: Eco-Friendly and Energy-Efficient Operations
With a rising emphasis on green practices, warehouse automation stands out as a sustainable solution. Automated systems, especially those that are energy-optimized, often consume less power and operate more efficiently than their manual counterparts. By reducing waste, optimizing energy usage, and decreasing the carbon footprint, automation supports eco-conscious warehousing.
Data-Driven Decision Making: Insights and Analytics
The digital components of warehouse automation systems continuously collect and analyze data. This information provides valuable insights into performance metrics, peak demand times, and process bottlenecks. With this data at their fingertips, managers can make informed decisions, anticipate challenges, and strategize for future growth.
Customer Satisfaction: Meeting Evolving Consumer Demands
In today's fast-paced world, consumers expect swift and accurate deliveries. Warehouse automation, with its rapid order processing and reduced error rates, ensures that orders reach customers on time and as expected. This efficiency directly enhances customer satisfaction and loyalty, giving businesses a competitive edge in the market.
Reduced Product Damages: Precision Handling and Storage
Automated systems are meticulously designed for precise handling. Robots, conveyor systems, and automated storage solutions handle products with care, reducing the chances of damages that can occur with manual handling. This precision ensures products remain in pristine condition, leading to fewer returns and increased customer trust.
Flexibility in Operations: Adapting to Market Changes
Warehouse automation systems are not rigid; they are designed to adapt. Whether it's adjusting to seasonal demand fluctuations, introducing new product lines, or adapting to market disruptions, automation ensures that warehouses can swiftly pivot their operations without significant downtimes or disruptions.
Integration with Modern Technologies: Seamless Connectivity
Warehouse automation systems can be seamlessly integrated with other modern technologies like AI, machine learning, and blockchain. Such integrations further enhance the capabilities of the warehouse, from predictive analytics to transparent and secure supply chain operations.
Hopstack as Automated Warehouse Management System For Warehouse Automation
At Hopstack, we believe in adapting modern technology to automate every stage of the warehousing process. We understand the challenges warehouse owners have to face when running a business. We provide companies with robust Warehouse Management Systems that help them take their warehousing game to a whole new level.
Schedule a demo with our industry experts to know more!In the present day and age, automation in almost every industry and organization is considered to be revolutionizing. The idea behind automating your workflow is simple. It is to reduce operational costs and improve efficiency. But when it comes to automating a warehouse, things can get complicated. A warehouse is a significant component of the supply chain. There are so many moving parts and a lot to keep in mind before you know where or which part of the warehouse needs automating.This article will take you through everything you need to know about Automated Warehouse in detail. It will also include the latest trends in technology and the challenges in Automated Warehouse you might encounter.
Frequently Asked Questions (FAQs)
What factors should I consider when selecting a warehouse automation system?
When selecting a warehouse automation system, consider factors such as your warehouse's volume of orders, space constraints, workflow, and specific operational needs. Additionally, assess the long-term costs, scalability, and integration capabilities of the system to ensure it will grow with your business and provide a solid ROI over time.
How do I calculate the return on investment (ROI) for a warehouse automation system?
To calculate ROI, consider both the initial investment and the long-term savings. Factor in upfront costs for hardware, software, installation, and training, as well as ongoing maintenance and operational costs. Then, estimate the efficiency gains, labor savings, and error reduction the system will bring, and calculate how quickly those benefits will offset the initial costs.
What are the challenges of integrating a new automation system with existing warehouse processes?
Integration challenges can include compatibility with existing software systems (like Warehouse Management Systems), potential downtime during the installation process, and the need for training staff to work with the new automation tools. It’s crucial to assess your current systems and ensure that the new automation solution can seamlessly integrate without disrupting daily operations.
How long does it take to implement a warehouse automation system?
The implementation timeline varies based on the complexity of the system and the scale of your warehouse. Simple systems may take a few weeks to implement, while larger, more complex systems could take several months. Consider factors such as system installation, integration with existing software, testing, and staff training when determining the timeline.
What types of automation systems are easiest to implement?
Conveyor systems and automated guided vehicles (AGVs) are generally easier to implement than more complex systems like ASRS or robotic picking systems. These systems typically require less structural change and can be deployed with minimal disruption to existing warehouse operations.
How do I ensure my automation system can scale with my business?
To ensure scalability, choose systems that offer modular design or flexible configurations. For example, look for warehouse management systems (WMS) and automated solutions like ASRS, conveyors, or robots that can be expanded or adjusted to accommodate growing order volumes or changes in product types. Be sure the system integrates smoothly with other technologies you may add in the future, such as AI, machine learning, or advanced robotics.
How do I measure the performance of a warehouse automation system after implementation?
Performance can be measured through various metrics such as order fulfillment speed, accuracy rates, inventory turnover, and labor savings. Real-time data from the Warehouse Management System (WMS) and other automation components will help track these metrics. Regular audits and performance reviews will allow you to assess whether the system is meeting your operational goals.
What ongoing maintenance is required for a warehouse automation system?
Warehouse automation systems require regular maintenance to ensure optimal performance. This includes software updates, hardware inspections, and troubleshooting of any issues that arise. Some systems also have preventative maintenance schedules to avoid unexpected breakdowns. Many companies offer service contracts to handle ongoing maintenance, and in-house staff may need to be trained to manage certain maintenance tasks.
Can I integrate a new automation system with my existing Warehouse Management System (WMS)?
Yes, many modern warehouse automation systems are designed to integrate with existing WMS, Warehouse Control Systems (WCS), and Enterprise Resource Planning (ERP) systems. However, integration complexity can vary depending on the age and capabilities of your current systems. It’s essential to work with your automation system provider to ensure seamless integration and data synchronization between systems.
What are the most common mistakes to avoid when implementing a warehouse automation system?
Common mistakes include failing to thoroughly assess the warehouse’s specific needs, selecting a system that doesn’t scale with future growth, overlooking employee training, and not accounting for the total cost of ownership (TCO), which includes maintenance and operational costs. Additionally, inadequate testing before going live can lead to operational disruptions.
How do I ensure that my staff adapts to the new automation system?
To ensure smooth adoption, involve staff in the selection and implementation process by clearly communicating the benefits of automation. Provide comprehensive training sessions tailored to different roles and encourage hands-on experience with the system. Ongoing support and feedback channels will also help staff feel more comfortable and empowered to use the system effectively.
What kind of support will I need from my automation system provider?
Ensure that your automation system provider offers robust technical support, including installation assistance, troubleshooting, software updates, and training. Providers should also offer post-installation support in case of system errors or when modifications are needed as your business evolves. Ideally, support should be available 24/7 to minimize downtime.
How do I stay updated on new trends in warehouse automation?
Stay updated by attending industry conferences, webinars, and trade shows where new automation technologies and trends are showcased. Subscribing to industry publications and following thought leaders in warehouse automation on social media can also keep you informed. Additionally, your automation system provider may offer updates and new features that can further improve your operations.
How do I ensure my automation system complies with industry regulations?
Ensure that your automation system provider adheres to all relevant industry regulations (e.g., OSHA standards for workplace safety). Regular audits and consultations with experts on compliance issues can help you stay ahead of regulatory changes. It’s important to stay informed about regulations related to data security, especially if you are using RFID or other tracking technologies.